Meeting tightened emission limits in record time at CIECH Soda Polska S. A.
Time definitely flew when Valmet carried out a wet flue gas desulfurization project in just 24 months at CIECH Soda Polska’s Inowroclaw combined heat and power (CHP) plant in Poland.
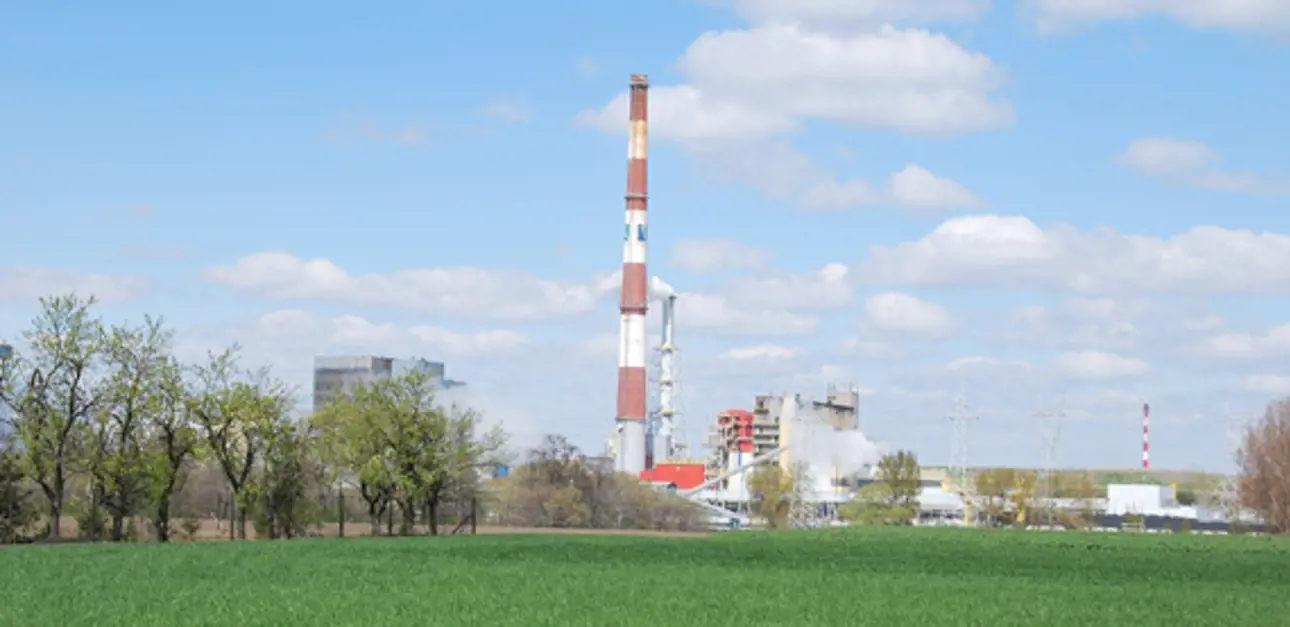
A few years ago, CIECH Soda Polska S. A., owned by the leading chemicals group CIECH in Poland, had to take action. Its combined heat and power (CHP) plant was in the national transition plan for compliance with the Industrial Emissions Directive (IED). The IED aims to achieve a high level of protection of human health and the environment by reducing harmful industrial emissions across the EU, in particular through better application of Best Available Techniques (BAT). Annual emission limits for sulfur dioxide, nitrogen oxides and particulates would tighten, and CIECH Soda Polska S. A. couldn’t reach them with the four OP-110 pulverized coal boilers dating from the 1970s.
There were two flue gas desulfurization (FGD) alternatives for the boilers that produce steam and electricity for the Inowroclaw Chemical Plant – either a semi-dry method or Valmet’s wet solution.
“We selected Valmet as the supplier because the solution was the most competitive overall. It provides the lowest operational cost. We were also pleased that Valmet managed to optimize the duration and timing of the boiler outages required during construction, thereby minimizing the production losses of the chemical plant,” says Marcin Małek, Director of Investments of CIECH Soda Polska.
The advantage of the FGD solution based on wet limestone is the relatively low cost of the limestone sorbent and the production of commercial-grade gypsum that can be used in a wide variety of applications in the building industry. A major technology benefit is flexibility. It is possible to utilize waste lime or semi-dry FGD end product in the process, lowering the operating costs further.
A full and fast EPC delivery
The contract was signed in July 2015. Valmet’s turnkey delivery included a flue gas desulfurization (FGD) installation and a selective catalytic reduction (SCR) system for each boiler to denitrify flue gases. Each boiler was equipped with a new rotating air preheater and new flue gas fan to further extend the boilers’ lifetime.
“By combining the SCR and wet FGD systems, it is possible to minimize ammonia slip and remove mercury, which is not possible with a semi-dry system,” points out Tarja Korhonen, Solution Sales Manager, Valmet.
Valmet acted as the engineering, procurement and construction (EPC) contractor in the delivery. The extensive FGD project scope included design and engineering, purchasing and delivery of equipment, construction and erection, project management, permitting, commissioning and customer training.
![]() |
Valmet carried out a wet flue gas desulfurization project in just 24 months
“The project was carried out in record time and on budget in just 24 months. Typically, a wet FGD project takes anywhere from 32 to 36 months,” Korhonen goes on. “This was possible thanks to the fast-track method in which various project stages overlapped. It made both engineering and project management highly efficient.”
For example, building permit design was carried out in parallel with basic engineering, while purchasing, execution design and site execution work overlapped.
“Additionally, there were weekly and monthly meetings with the customer, resulting in close cooperation and transparency,” she continues. The project schedule and progress were closely followed up online. Site coordination and change management were effective with an up-to-date 3D plant model.
Target reached and exceeded
The flue gas desulfurization (FGD) process handover took place in July 2017. The first selective reduction catalyst (SCR) installation was started up in June 2016, and the last one will be installed in October 2018.
With Valmet’s FGD solution based on wet limestone, the Inowroclaw combined heat and power (CHP) plant has been able to achieve its main investment target. The plant meets BAT emission levels and goes well below the IED limits for sulfur dioxide – with the lowest life-cycle cost. SO2 emissions are now under 100 mg/Nm3 and dust particle emissions under 10 mg/Nm3.
“It was a good decision to select Valmet’s wet FGD and SCR technologies for our application. Thanks to Valmet’s professional and experienced project team, good cooperation between the parties and hard work on the construction site, the project proceeded in a timely manner. The plant is performing in line with the requirements given, and we have achieved our emissions targets,” says Grzegorz Bielawski, Energy Director, CIECH Soda Polska.
Currently, Valmet is delivering a similar FGD installation to CIECH Soda Polska’s Janikowo CHP plant and also modernizing the flue gas desulfurization process for three coal-fired boilers at PCC Rokita S.A’s CHP plant in Poland.
Related articles