New BFB Boiler delivers significant savings
Jun 26, 2024
Having commissioned Boiler 5, a Valmet BFB Boiler that runs on sludge and paper rejects, WEIG saves fuel and waste disposal costs, as well as generating more energy. A long-term service agreement with Valmet also ensures optimal operation.
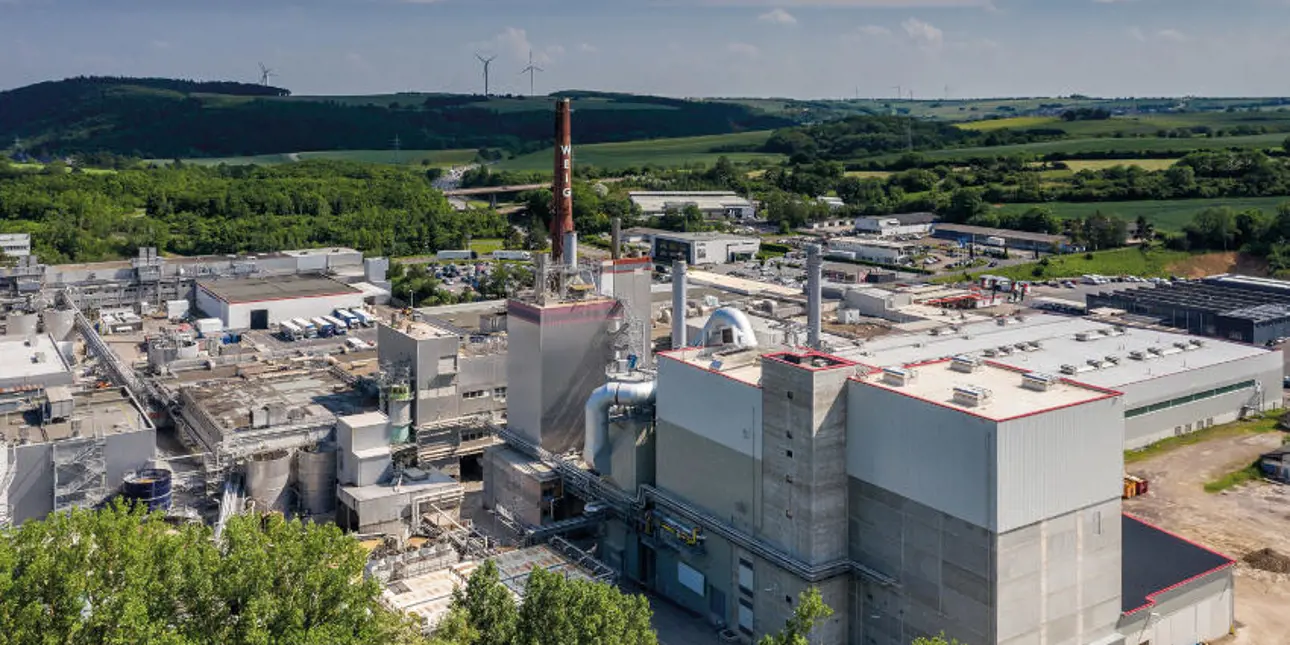
When WEIG’s old waste boiler, Boiler 3, in Mayen, Germany, was reaching the end of its lifespan, the mill decided to replace it. WEIG, a renowned family-owned business group
in the international paper and cardboard industry, is a major supplier of cartonboard in Europe and a leading global manufacturer of plasterboard liner, making both from recovered fibers. Employing 1,800 people across locations in Europe and South America, WEIG emphasizes sustainability and innovation in all its operations.
We wanted a boiler that featured high reliability and high efficiency.”
“Our investment target was to save energy costs by reducing the use of natural gas, as well as to reduce CO2 emissions and waste disposal costs,” explains Stefan Behmer, Deputy Project Manager for the Boiler 5 project at WEIG. “We wanted a boiler that featured high reliability and high efficiency. We were looking for a supplier with experience of such boilers. Valmet was one of them.”
Although WEIG uses Valmet paper machine equipment in their board processes, they were unfamiliar with Valmet’s energy solutions. Behmer continues: “During the sales phase, we met a lot of Valmet’s boiler and air emission control experts and were impressed by their references. We were confident that Valmet would execute the project successfully. ”
An optimized boiler plant concept
Valmet’s turnkey delivery included a 44 MWth Valmet BFB Boiler utilizing bubbling fluidized bed technology, a flue gas treatment plant, new buildings for the equipment, and a connection to an existing automation system.
WEIG, Valmet, and independent consultant Eproplan worked closely to integrate various technical specialties into an optimized concept. It includes a residue/waste fuel boiler design, an integrated biogas-fired final superheater, a hot electrostatic precipitator (ESP) for fly ash pre-separation, and a tail-end Selective Catalytic Reduction (SCR) system with flue gas reheating and heat recovery.
The multi-fuel boiler runs on a mix of paper sludge (65%), pulper rejects (30%), and biogas/natural gas (5%). The fuel mix can be adjusted flexibly. The boiler generates 15 kg/s of high-pressure steam at a pressure of 82 bar and a temperature of 530 °C, and it has an incineration capacity of approximately 200,000 tonnes of residues per year, with a combustion output of 49 megawatts.
According to Behmer, the erection and commissioning phases went well despite the challenges posed by the Covid-19 pandemic. “We had productive discussions with the Valmet staff and always found mutually acceptable solutions,” he says.
Major fuel cost savings and emissions reductions
WEIG’s Boiler 5 has been fully operational since 2020. “The boiler plant has met our expectations. It has saved us a lot of money during the current energy crisis and enabled us to continue production normally,” Behmer remarks.
According to WEIG’s sustainability report, the investment has enabled the company to save around 150 GWh of the primary fossil fuel (natural gas) per year.
A more modern maintenance approach
To ensure smooth operation in the years to come, WEIG signed a long-term service agreement with Valmet in 2023. This lays a firm foundation for long-term cooperation with the aim of cost-effectively maintaining and further improving the plant’s availability, efficiency, process, and maintenance.
The service agreement covers visual inspection services, shutdown planning, and onsite advisory support, as well as regular and on-demand expert support for the BFB boiler, ash handling, sand feeding, ESP, and baghouse filter (BHF). Spare part management is also included.
It’s really important for us that Valmet experts inspect our equipment status.”
“With Boiler 3, we used to do only whatever was necessary. With Boiler 5, we’ve taken a different and more modern maintenance approach. We want to be aware of what will be happening during the next few months or year so we can plan better and not be surprised by unplanned shutdowns,” Behmer says. “It’s really important for us that Valmet experts inspect our equipment status and give us an estimate of when something needs to be repaired or replaced.”
Boiler 5 is a complete optimized BFB boiler concept that enables WEIG to reduce their use of natural gas.
Looking at connected support
There are ongoing discussions about building a remote connection between the plant and the Valmet Performance Center. “Connectivity would be beneficial for us in troubleshooting, for example. We could ask Valmet experts to look at our process data and advise us about how to get the boiler running optimally again.”
The Valmet staff have also enjoyed the positive teamwork with WEIG. “It’s always a pleasure to visit the Weig power plant. Our cooperation has been very good, with honest and constructive communication. We’ve always worked very well together on problems and found solutions that satisfy both sides,” says Domenico Viccica, Service Manager, Energy, Recovery and Environmental Services, Central Europe North, EMEA, Valmet.
Text: Marjaana Lehtinen