Remote support ensures timely start-ups also during the COVID-19 outbreak
Global COVID-19 travel restrictions have not reduced Valmet’s commitment to serving our customers in the best possible way. Thanks to remote connections and the active use of digital tools, we’ve been able to help papermakers all over the world with their recent machinery start-ups.
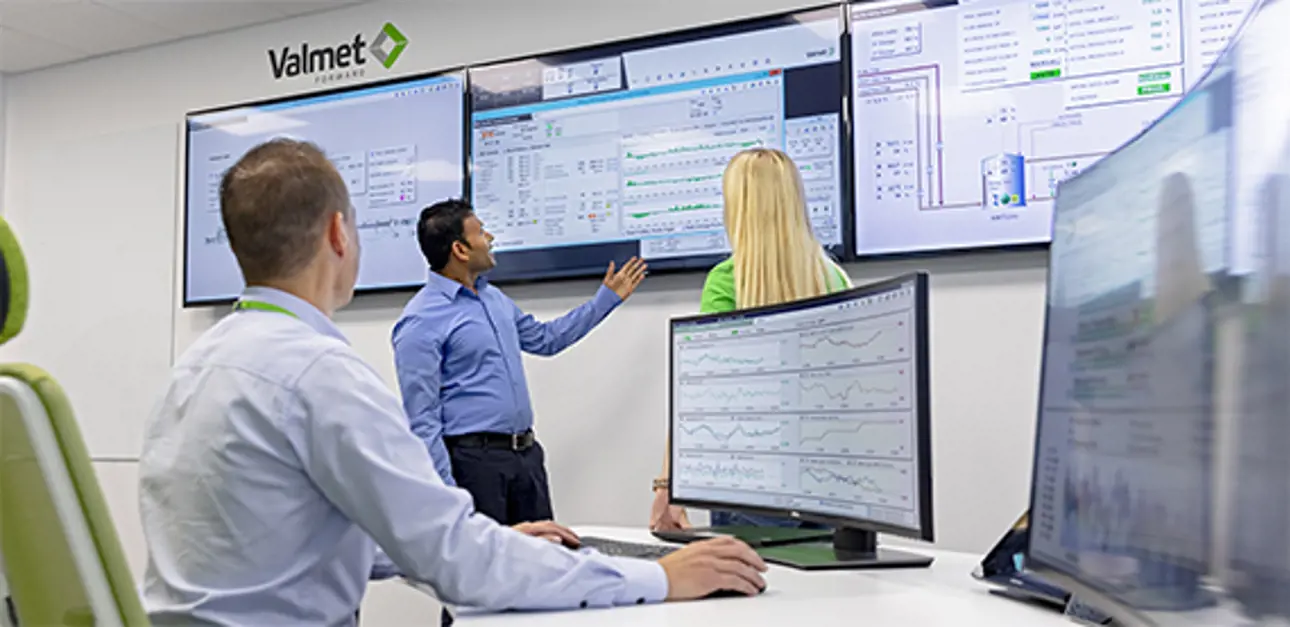
From the Performance Center, Valmet’s remote experts have been able to offer increased remote assistance to paper and board makers all over the world at a time when onsite visits have not been an option. This has ensured that both rebuilt machines and totally new production lines have been starting up as planned.
“We’re taking every possible step to help our customers through this challenging period. With good planning, persistent work and efficient collaboration using digital tools, we’ve been able to remotely support several projects, both in commissioning and during start-ups, as well as continuing to provide process support services from the Performance Center,” says Jukka Savolainen, Technology Manager at the Board and Paper Performance Center.
Case 1: Successful remote support for winder start-up in China
The start-up of the third winder for a customer in China was about to begin when the COVID-19 situation began to deteriorate. It was quickly decided that the start-up would be handled as a joint venture by a remote team in Finland and a local team in China. Naturally, all the physical work like the testing of winder movements was undertaken on-site by local experts. Controls and parameters were tested remotely from the Performance Center, and daily communication was established to ensure real-time information flow.
“For the first project of its kind, the remote start-up performance was excellent, and the team did a great job”, says Harri Lindberg, Manager, Project Automation Engineering.
Close cooperation between local and remote experts in winder delivery enabled remote commissioning and start-up support. In the picture is Valmet’s site team, Kay Zhang, Fengming Lei, Fangqi Xiong and Yongqiang Zhang.
For the first project of its kind, the remote start-up performance was excellent.
Case 2: Remote support for a board machine conversion start-up in the USA
A customer’s existing paper machine was converted to produce white top liner. Both the commissioning and start-up were supported remotely from the Performance Center. There was also a local team at the site. Two shifts were working at Performance Center to carry out the I/O, circuit, functional, and movement testings.
“In many ways, this is a new situation for everyone. Cooperation is definitely the key,” says Senior Chief Engineer Timo Kupari. “My eyes are here, and the machine is there. The colleague at the site is my hands,” says Ari Edwards in summarizing the big change in the remote start-up crew’s daily work.
“There’s a really big difference in our tasks compared to normal onsite activity now that we’re working remotely. We’ve learned the importance of communication. It’s a good thing that both teams – we at the Performance Center and the onsite guys – are really committed to making things work for the customer and getting the machine up and running,” says Start-up Engineer Simo Suortti, who credits the entire team.
We’ve learned the importance of communication.
Ari Edwards, Simo Suortti and Timo Kupari run the remote start-up support for a board machine in the USA from the Valmet Performance Center in Jyväskylä, Finland.
Case 3: Remote support for a SymBelt shoe press roll change in Germany
The press section at a customer site in Germany recently underwent a press section upgrade. The existing shoe press’s second roll was replaced with Valmet’s latest shoe pressing roll technology. The new roll improves the performance and reliability of the press section. It’s lighter but endures higher press loads, and it’s more user-friendly and easier to maintain. The commissioning and testing tasks were divided between a local team and remote experts at the Valmet Performance Center.
“We performed the normal commissioning and testing for the new SymBelt roll. The only difference was that the team was split between two places,” explains Timo Ikävalko, Senior Industrial Internet Process Specialist. “Thanks to the DNA system and remote connections, I feel there’s no difference whether you’re working on-site or remotely. The start-up went well and the customer was supportive with the remote work,” he continues.'
How does the paper machine remote start-up support work?
In remote start-up support, Valmet's expert team leads and guides the testing and commissioning remotely from Valmet Performance Center. The local on-site team carries out control actions in co-operation with the customer.
Related articles