Yara invests in the future
Yara has invested MEUR 75 in the Siilinjärvi mine in the form of a paste plant for the tailings treatment plant. Outotec was in charge of the overall delivery, from the planning stage to device deliveries, construction and spare parts. In the paste plant, the process is being controlled using the Valmet DNA automation system.
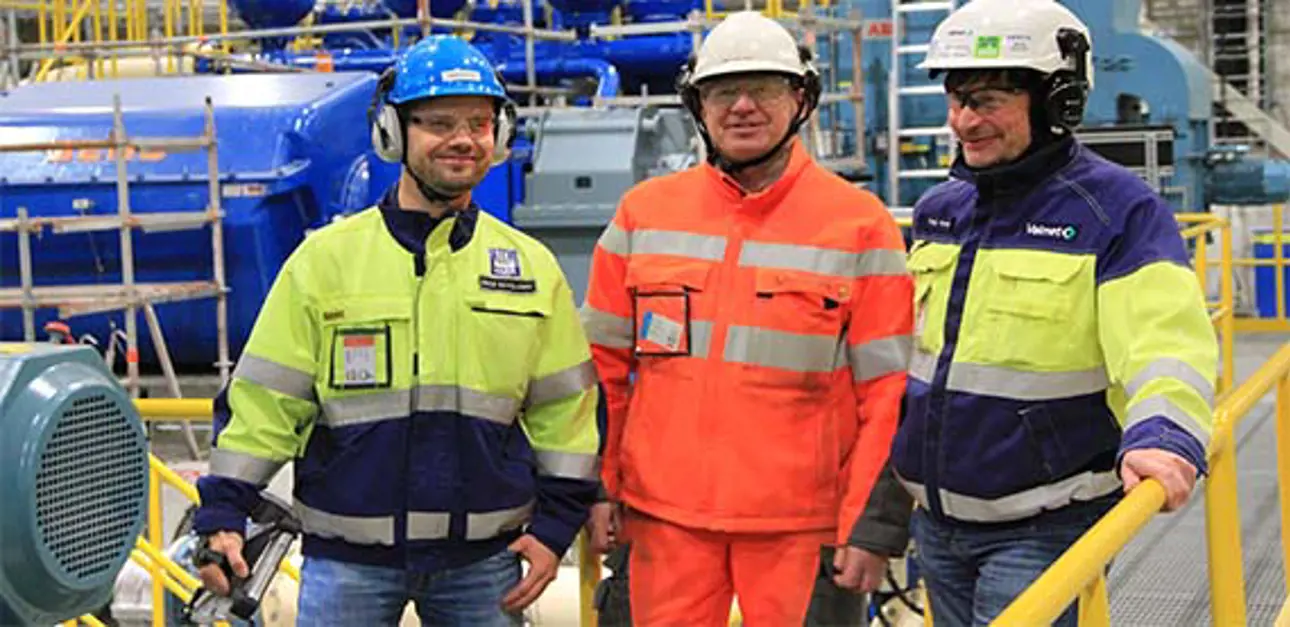
A unique implementation on this scale
The Yara mine produces approximately one million tons of apatite a year, which is used for manufacturing phosphoric acid and fertilizer. 10 million tons of tailings are produced on the side. The solid content of the tailings is elevated from 45 percent to 70 percent in the new plant. At the same time, the banking properties of the sand are improved, which means that more sand can be banked in the area. The water separated from the sand is returned to the process in the concentrating plant.
Outotec was the EPC supplier of the plant, with responsibility for plant engineering, procurement, construction and spare parts. This is the largest ever project implemented in the Siilinjärvi mine since it was established. First, a pilot plant was constructed, and with the help of the experience gained from it, the actual production plant was constructed. The paste plant is unique in all of Europe in terms of size.
Yara demands a high level of automation
The paste plant has been in use for a year now. Automation specialist Mikko Savolainen was in charge of automation and instrumentation at Yara. From Outotec, project engineer Harri Multanen was in charge of automation design and implementation as well as instrumentation from the point of view of the EPC supplier. Eemeli Ruhanen acted as the Yara process expert and Olli Siltala was in charge of Outotec process expertise.
Caption: From left Eemeli Ruhanen, Reijo Simonen, Mikko Savolainen and Harri Multanen
Valmet DNA automation systems have been used by Yara plants for a long time. In 1986, the concentrating plant was equipped with a Damatic Classic, which was updated to the Damatic XD in the 1990s. More recently, the system has been updated to cutting edge Valmet technology. Due to usability and maintenance issues, the paste plant requires a high level of automation.
Careful preparations were made ahead of the project, and initial data and specifications were considered carefully. Mikko Savolainen says: “We had strict demands for the equipment. We wanted an automation system that was as compatible with the concentrating plant as possible in terms of functionality. The concentrating plant has been using Valmet automation, which made Valmet DNA a natural choice.”
Harri Multanen: “Valmet DNA is clearly above average with its integrated condition monitoring. In addition, the Outotec upper level control system ACT was integrated into the system using the OPC interface to optimize thickener operation.”
Caption: Yara's team with Valmet's Reijo Simonen
Mikko Savolainen offers some reasons for this: “An additional challenge is posed by the fact that the paste plant is located seven kilometers from the concentrating plant. In the future, we want to achieve an unmanned plant, which requires a great deal of automation.”
Runnability with Valmet DNA
We achieved the desired high level of automation with the Valmet DNA automation system. In order to ensure usability, the process, alarm and operating stations as well as networks have been duplicated. The process itself is not dangerous, but a power cut would cause problems, because the slurry must be in constant movement.
According to Harri Multanen, Valmet DNA functions in all situations, which ensures runnability and process control. In addition, the interlocks of the system ensure the operation of the process in exceptional situations. The motor center and motor actuators are connected using the Profibus DP fieldbus and the power supply utilizes the IEC-61850 bus.
In terms of developing the system, interlocks and up-to-date technical descriptions are very important, representatives from both Yara and Outotec emphasize. Most descriptions and operating displays are bilingual. The project utilized the new Valmet interlock windows that could be implemented directly from the application.
Pumps integrated into the automation system
Slurry is pumped by three massive PD piston pumps, each equipped with a 2.3 MW main motor. Auxiliary motors in each pump consist of 11 motors and several valves. The pumps have been supplied by Weir Minerals in Holland, and the pump application has been developed in cooperation with suppliers.
Mikko Savolainen says: “Piston pumps are essential to the paste plant. We wanted to integrate the pumps to the automation system, which meant that we had to replace the separate logics of the supplier with Valmet DNA. In the future, this will benefit maintenance and operators.
All parties agree that using simulation in testing was significant. Harri Multanen says: “We worked hard to have the pumps function seamlessly, and it paid off.” According to Eemeli Ruhanen, focus was placed on the sequences of the pumps and the functionality of the controls. Simulation was used to envision process situations that could fail, while making actual changes to improve operation.
Reijo Simonen, Project Manager at Valmet, says: “Factory testing was used to transfer program data from Weir Minerals to Valmet. The programming language of the pumps was changed to suit our system, and all of the functions were tested using simulation. Good functionality was achieved in cooperation with the pump supplier, and their representative was involved in the testing. During water testing, we could see that everything functioned as planned.”
Condition monitoring anticipates any faults
Condition monitoring is integrated into the automation system using the Valmet DNA Machine Monitoring (DMM) solution. It monitors the operation and possible faults of electric motors, gearboxes, pumps, compressors and large back-pressure valves, among others. Nearly 180 acceleration sensors have been placed in the plant for machine monitoring.
In addition, the oils of gearboxes and hydraulics are condition monitored. The equipment is used to measure the characteristics of oil comprehensively, which enables early intervention in case of any faults. At the same time, the system alerts if the oil has become dirty for some reason. The Valmet DNA Field Device Manager is also in use. It transmits field device diagnostics to the automation system via HART communication.
Mikko Savolainen: “The goal of condition monitoring is to monitor the operation and condition of the process machinery, devices and field instrumentation as well as locate any faults in time in order to fix them in a controlled manner during scheduled downtime. This helps us optimize the life cycle of the equipment.” Yara has set its goal at zero unforeseen faults.
Wireless connection
A WLAN connection and a wireless operating station enable remote connections from the field. Primarily, one operator works in the control room. If necessary, operators may work in the field using wireless tablet computers. Maintenance and tuning operations utilize this option the most, including special displays, which was optimized for the tablet.
“A comprehensive WLAN network enables operating in the paste plant, and the operator is not tied to the control room. Similar wireless connections are also available at the concentrating plant,” Mikko Savolainen (in picture) says.
“Piston pumps pumping slurry, in particular, are especially suited for operating from the field. We are now able to monitor the process when we move through the field,” Eemeli Ruhanen chimes in.
Careful factory testing - > Quick commissioning
Factory testing was conducted in Tampere in cooperation with Yara, Outotec and Valmet. Maintenance personnel from Yara also participated in the testing, which enabled them to see the system in advance and get to know the new process.
Water testing was conducted in the plant prior to commissioning, after which the process was run on slurry, says Eemeli Ruhanen. Harri Multanen says that commissioning went smoothly. “I have never seen such a quick commissioning in my life. All the participants were very motivated and really involved in the process. The plant was commissioned to full capacity after water testing in practically four days in the heart of winter in January. Automation caused exactly zero problems for us.”
Mikko Savolainen agrees and stresses that they had exact plans that they followed precisely. Careful factory testing enabled a quick commissioning process, which was completed practically within one month.
Project finished faultlessly
The paste plant functions well thanks to strong expertise. Mikko Savolainen says: “The automation is exactly what we ordered. The entire project went smoothly, and we can be very satisfied with the end result. This combination of cooperation partners worked well: Outotec, Yara and Valmet.”
Harri Multanen from Outotec agrees: “I am positively surprised that Valmet DNA has no shortcomings whatsoever. In my role as EPC representative, I am rarely involved in specifications to this degree as in this project. The system has been integrated well, and we had excellent people working on program specifications together with Valmet. Communication is key in every project, and this time it ran like clockwork.”
According to Eemeli Ruhanen, the goal from the beginning was easy-to-use automation, because the number of staff will not be increased. “We achieved ease of use. The difference to the operating of the concentrating plant is evident in sequences, in particular, which we have not really used before. Even though our goal is to have an unmanned paste plant, we are taking things step by step. We are not taking any unnecessary risks,” Eemeli stresses.
Maintenance contract to facilitate downtime scheduling
According to Mikko Savolainen, they use an automation system with long-standing traditions at Yara in Siilinjärvi. Reading applications is user-friendly and history data is easily available via trends and reports.
Cooperation is continued with the local Valmet offices in Kuopio. In conclusion, Mikko says: “Maintenance is carried out both on site and remotely. We are drafting a roadmap in cooperation with local maintenance staff to help us in planning investments. The concentrating plant and the paste plant have annual maintenance shutdowns, which means that work must be carefully planned in advance.”
The first maintenance shutdown at the paste plant is over. All of the work was carried out on schedule, which means that the paste plant works according to plan.
For more information:
Reijo Simonen, reijo.simonen at valmet.com