Warping and runnability problems cured in Cartojanes Santorromán
Cartonajes Santorromán is a family run company in Spain with over 100 years experience, spanning four generations, in producing paperboard boxes and packaging. They work closely with the food and beverages as well as wine and spirits sectors where corrugated cartonboard plays an important role in the protection and handling of the products. Packaging for footwear, technical, automotive, construction and furniture industries also feature in Santorromán’s product portfolio as well as being certified for the manufacture of hazardous goods packaging.
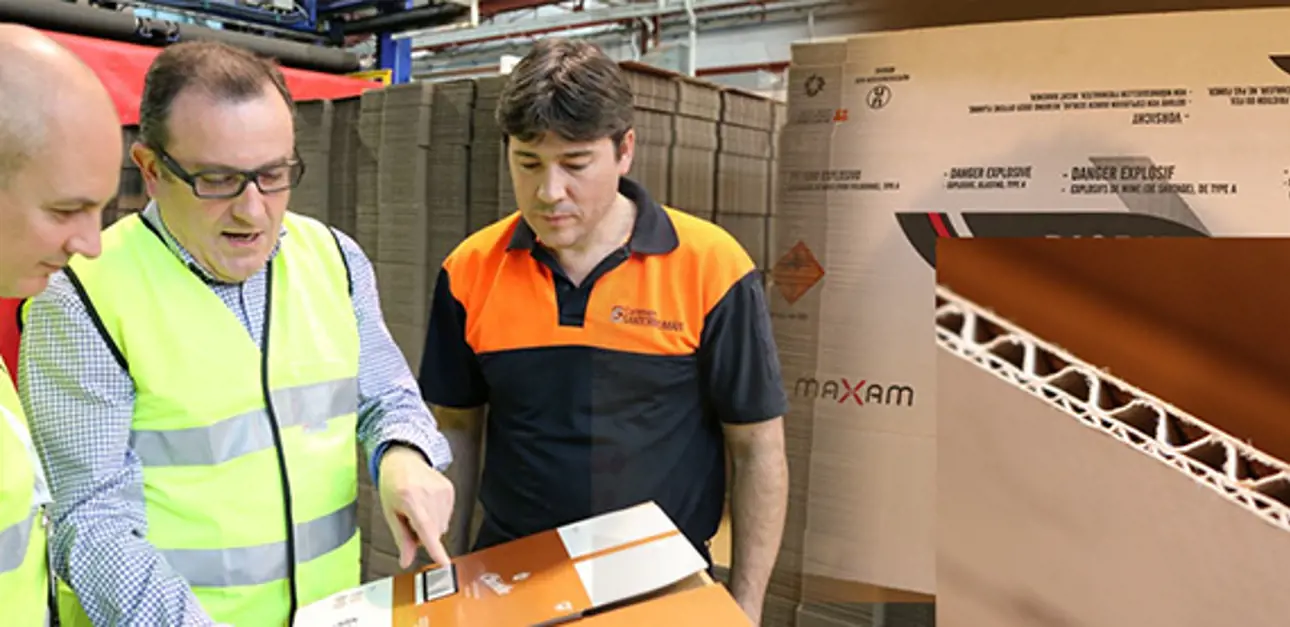
Santorromán has a philosophy of constantly investing in infrastructure and technology for the manufacture of corrugated cartonboard and any product that can be made with it. This has led to many innovative products and a well deserved reputation for quality. Innovative products bring new challenges and when faced with a warping problem, Santorromán turned to Valmet for a solution.
Warping in the final combined sheet is one of the most serious defects that can occur on the corrugator.
An explosive problem!
The corrugator is the backbone of corrugated cartonboard production at Santorromán and combines two stages. At the wet end, the paper is heated, moistened and formed into a fluted pattern after which it is glued with a starch based adhesive to a facing of smooth paper. Next, at the double-backer, a second flat linerboard is glued to the other side to form a single wall corrugated board. At the dry end, Slitter-Cutter-Creaser cuts and scores the cartonboard sheets to the patterns defined by the requirements of each order. The product is then stacked by the stackers and placed in provisional storage until further processing. Differences in moisture content of the top and bottom facings can cause warping or bending of the sheet which interferes with the following converting processes. “The warping problem manifested itself when making a double wall (five plies) board on the corrugator which involves the gluing of a second microchannel flute and facer to the C-channel fluted board,” says Jesús Pérez Osma, Technical Manager. This type of product, a Santorromán specialty, is used for instance to make boxes to transport explosives, an application for which the factory has special certification. Microchannel fluted products are also used extensively for fruit and vegetable packaging.
Santorromán’s combination microchannel and C-channel fluted board is internationally approved for the transportation of explosives.
Warping in the final combined sheet is one of the most serious defects that can occur on the corrugator. Cross direction warp is caused by differences in moisture between the top and bottom liner with higher moisture causing more shrinkage of pulp fibers to warp or bend towards the side with higher moisture.
Jesús Pérez Osma, Technical Manager (center) explains the finer points of a 6 wine bottle box to Javier Navas of Valmet (left) with Corrugator Machine Manager, Victor Ruiz, (right).
Valmet IQ Moisturizer
One of the two Valmet IQ Moisturizers
Santorromán installed 2 Valmet IQ Moisturizers for liner moisture control in March 2015. The Valmet IQ Moisturizer, used extensively in paper production to control curl, wrinkles and heavy edges, has found a ready market to correct warp in corrugated board. The IQ Moisturizer corrects the warp of combined board by spraying a fine mist to the liner in a controlled way providing a very high degree of control and very fast response to quality destroying conditions.
Easy to operate
The operators now know how much moisture to add and need to just enter the number of grams per square meter according to grade. For Victor Ruiz, corrugator machine manager, the moisturizer is easy to use, “I see the first sheets from the machine and with experience I can quickly make adjustments if needed. For lighter boards we can also adjust the cross direction profile to correct the edges,” he says. The control system delivered with the moisturizer takes care of production rate changes automatically, so even during reel changes when the machine speed is changing the moisturizer adapts immediately. Moisture applied varies according to grade with the fine mist nozzles coping with as little as 0.3 gm/m2 for grades up to 3.5 gm/m2 for the double faced board. A new reel can have a different moisture content but the control makes it very easy for the operator to quickly change the moisture applied to the liner.
A bale of corrugated board with perfect flatness.
No reclamations
Jesús Pérez Osma has been impressed with the results, “The corrugators can now run at its maximum speed and the quality is better. Earlier we had few reclamations because if we were not satisfied we did not ship the product. But in the last year we had none and the best recommendation is in house from the converting machines where you can even hear that the printing machine is running better.”
“You can even hear that the printing machine is running better.”
Victor Ruiz, corrugator machine manager, says the moisturizer is easy to operate for the best effect.