Valmet's automation for all kinds of biofuel production
Availability and safety are unquestionably key issues in any process. In producing highly flammable fuels and biofuels, the importance of these issues grows even more. Today, several leading global producers rely on Valmet's process automation technology to control their biofuel plants, which produce second-generation biodiesel, bioethanol or bio-oil.
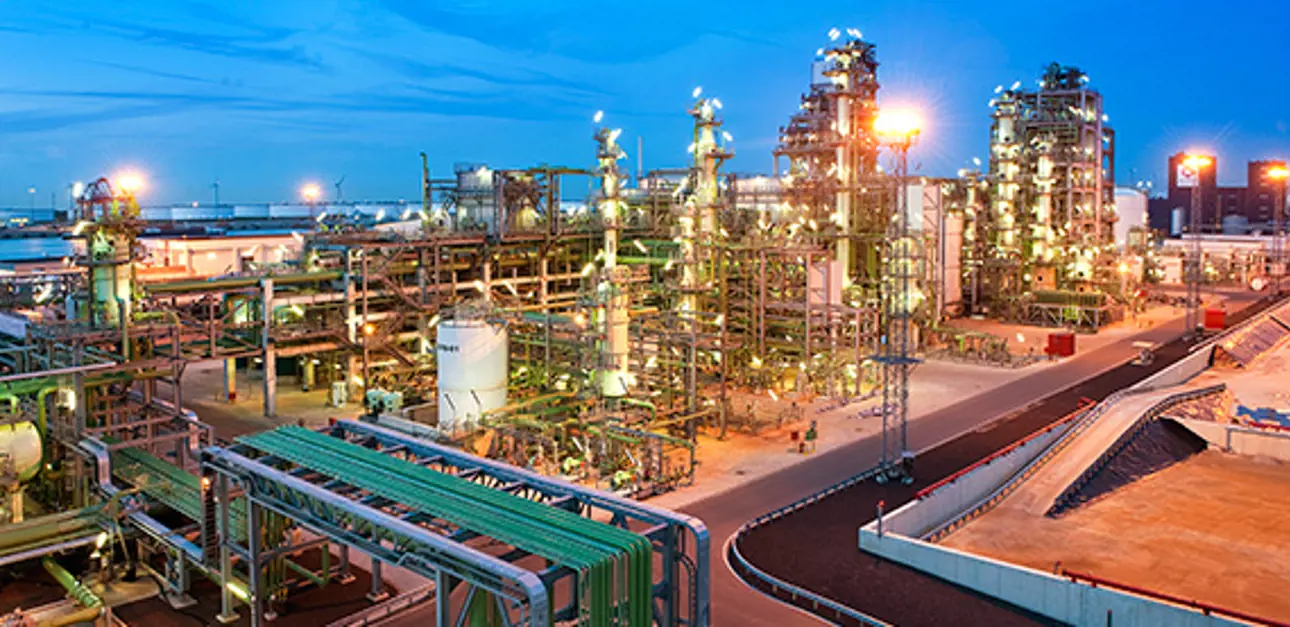
“The fact that makes process automation at biofuel plants even more demanding than at pulp & paper mills or power plants, for example, is that the processes include highly inflammable liquids and gases,” remarks Kari Karppinen, Sales Director, Automation, Valmet. “This means that process automation safety and reliability are very important. Dangerous process conditions are absolutely not allowed. If the process goes to a state outside specific values, it is immediately force controlled to a safe state by the safety system. Safety always comes first, investment costs only come after that.”
According to Karppinen, Valmet has intensely worked on safety issues in developing Valmet DNA features according to customer requirements. Safe operation and high process availability are, of course, secured by the fact all the critical system parts such as process controllers, data buses, links and power supplies are redundant.
Making the most advanced renewable diesel in the world
One of Valmet's long-standing customers is Neste Corporation in Finland, the leading renewable diesel producer in the world. The company has developed NExBTL renewable diesel production technology, which allows flexible use of any vegetable or waste oil in the production of premium-quality renewable diesel. Recently, the company announced having added technical corn oil, a residue generated during ethanol production, to the range of sources it uses to produce NExBTL renewable diesel.
In 2012, Neste produced enough NExBTL renewable diesel to power 2.1 million cars for a year. According to the company, its use has been proven to reduce greenhouse gas emissions by over 40–90% throughout the product's entire life cycle when compared with fossil diesel.
In its demanding biofuel production processes, Neste relies on Valmet's control technology. “We have had good cooperation with Neste for a long time,” Karppinen points out. “Today, the company has the largest renewable diesel refineries operating with Valmet DNA. Our automation is controlling Neste's renewable diesel plants in Finland, Singapore and the Netherlands, with altogether a total production capacity of two million tons annually. Automation and safety solutions guarantee efficient operations at all these renewable diesel plants.”
The Rotterdam refinery, the newest plant commissioned in 2011, is a significant milestone in Neste's cleaner traffic strategy and consolidates the company's position as the world's leading producer of renewable diesel. “Valmet is proud to have been chosen as a partner for this project, where high automation reliability and safety as well as demanding operational features cannot be excessively emphasized,” says Karppinen.
Valmet's deliveries to Neste's renewable diesel plants have included Valmet DNA automation systems, DCS integrated safety systems, field equipment maintenance tools and process history data storage, trending and reporting applications with remote access possibilities.
Controlling bioethanol production, too
In addition to biodiesel, Valmet's automation is also controlling new-generation bioethanol production at various plants in Spain, France and the Netherlands.
“We have supplied Valmet DNA process automation system hardware and software to several bioethanol plants through Schneider Electric (formerly Telvent), who provides the engineering for both ethanol and biomass boiler sections at these plants,” notes Esko Koivisto, Manager, Strategic Accounts, Automation, Valmet. “For the end customer, the cooperation between us two brings unique, well-functioning automation solutions that meet their requirements for efficiency and reliability.”
Currently, Schneider Electric and Valmet are working on a delivery to an international company in the US that applies innovative technology solutions for the development of sustainability in the energy and environmental sectors. The newest plant to produce next-generation bioethanol will be started up in 2014. Controlled by a Valmet DNA automation system, it will produce approximately 100 million liters of ethanol annually from biomass.
In this project, Valmet DNA process interface is widely based on fieldbus technology in addition to a conventional field interface. “We are also providing process engineering to develop an integrated process simulator for both the bioethanol and biomass boiler operations,” Koivisto adds.
Bio-oil through fast pyrolysis
A third interesting branch of biofuels in which Valmet is involved is the production of bio-oil. Fortum is currently building a new bio-oil plant in connection with its Joensuu CHP plant in Finland. Based on fast pyrolysis technology, the plant is the first of its kind in the world on an industrial scale. Upon completion, it will produce 50,000 tons of bio-oil annually, enough to meet the heating needs of more than 10,000 single-family homes.
Valmet will deliver the plant to Fortum as a turnkey delivery. The scope includes foundations and building work, necessary production equipment, a Valmet DNA automation system, and electrification. The demonstration venture will test and further develop integrated pyrolysis technology and the control solutions of the Valmet DNA system, which will be utilized in larger-scale pyrolysis processes in the future.
According to Fortum, energy produced with bio-oil reduces carbon dioxide emissions by over 70% compared with fossil fuels. The initial intention is to replace the fuel oil used at the company's own heat plants with the bio-oil made from forest residues and other wood-based biomass. In the future, bio-oil could also be used as traffic fuel or as raw material for various biochemicals.
The use of bio-oil has a significant positive environmental impact because energy produced with bio-oil reduces greenhouse emissions compared with fossil fuels. It has been calculated that the utilization of bio-oil produced at the Joensuu plant helps reduce carbon dioxide emissions by 59,000 tons and sulfur dioxide emissions by 320 tons per year.
The new bio-oil production plant is scheduled for startup in the autumn of 2013.
For more information:
Kari Karppinen, kari.karppinen at valmet.com