Valmet and Sunpaper relocated PM3 in 5 months record time
In 2022, Sunpaper signed a contract with Valmet to relocate its paper machine PM3 from Yanzhou, Shandong Province to Beihai, Guangxi Province, about 2000 kilometers. The relocation aims to increase Sunpaper’s competitiveness and align with the company’s green production strategy.
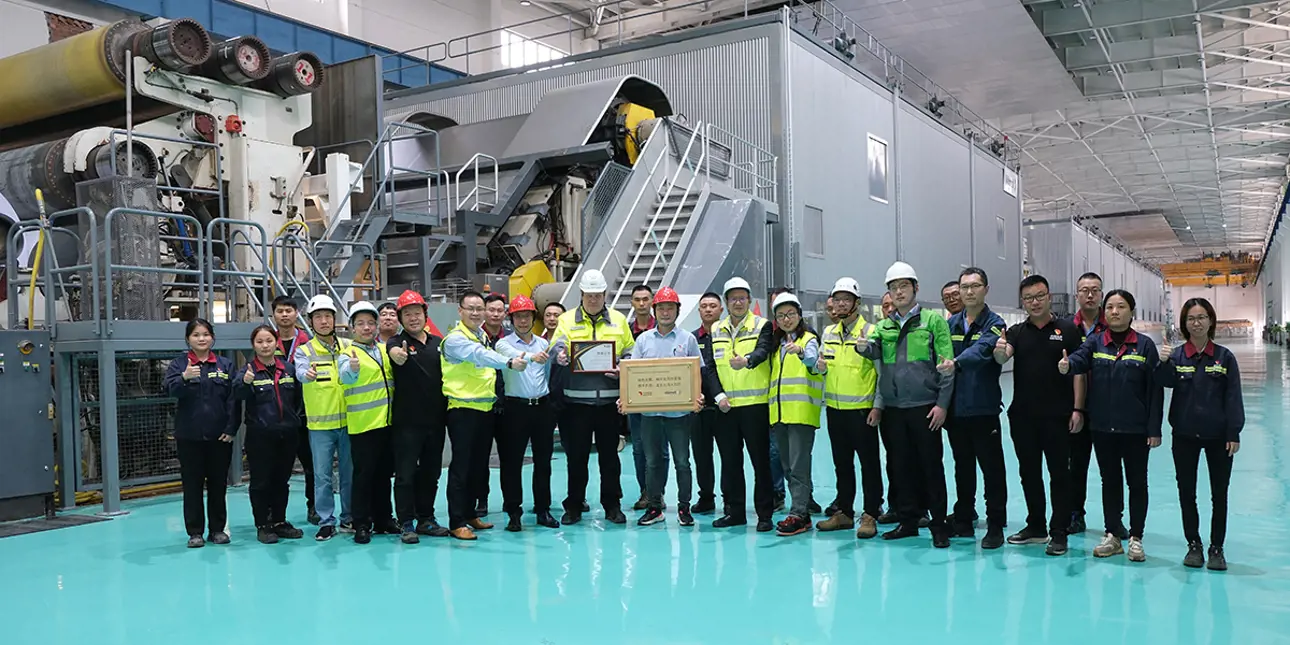
Moving towards a green factory
Sunpaper is a leading papermaker in China, with annual capacity of 5.8 million metric tons. A strategic decision was made to build an integrated ecosystem of forest, pulp and paper in Beihai. Currently its pulp capacity is 11,000 ton daily and 4 million ton annually. When they build the Beihai site, they always bear in mind the social responsibility to build a green and environmental-friendly factory.
“90% of the energy consumption comes from biomass, instead of traditional fossil fuels, which makes a big difference on environment. Every day, 180 ton of steam is recycled to supply the mill usage and we generate power from the gas we collected to minimize fossil fuels. Our mill is really a green mill, even a garden mill. “ Said Mr. Ying Guangdong, Deputy General Manager of Sunpaper.
Five months witnessed a new record.
2022 was not an easy year. With covid control everywhere, it was almost impossible to meet the 5-month project schedule.
“I remember at the end of project, 17 out of 32 Valmet engineers were staying at hotels as they were tested positive. Even with this extreme situation, we managed to keep our schedule. It is a record for both Valmet and Sunpaper, despite all the challenges. Valmet team showed us great commitment and teamwork. It wouldn’t be possible if both parties did not work as one team. “ Said Mr. Li Bing, Production Director, Sunpaper.
Upgrade to improve product competitiveness
PM3 was commissioned in 2008. After running more than a decade, a lot of assessment of PM3 was made within Sunpaper Group. The relocation is designed to upgrade some outdated technologies to improve product quality and be closer to pulp line to reduce cost.
The automation upgrades that were made include Valmet DNA distributed control system (DCS), Valmet IQ Quality Control System (QCS), Valmet Dilution Profiler, Valmet IQ Steam Profiler, Valmet DNA Machine Monitoring (DMM), Valmet PQV camera systems and Valmet Retention Measurement.
“We had lots of communication with Valmet experts. After understanding our needs, they gave a very suitable solution to solve our problem. The latest Valmet DNA has stronger processing capabilities. We can feel the system is more stable and the interface is also very user-friendly.
The upgraded quality control system (QCS) brings significant improvement on MD and CD controls. One thing I want to highlight is that we replaced one ash sensor for the QCS system. The new non-nuclear sensor does not have radiation source anymore. In that sense, Sunpaper and Valmet share the same social responsibility to a greener future. “ Explained Mr. Liu Bo, Automation Supervisor, PM 3, Sunpaper Guangxi.
“Our cooperation with Valmet has continued for more than 20 years. We fully trust Valmet expertise and professionalism. We are confident there will be more projects for us to work as a team going forward.” Said Mr. Li Bing, Production Director, Sunpaper.