The giants of the sea
The largest ever container vessels will soon sail with help of Valmet’s expertise. Daewoo Shipbuilding & Marine Engineering has chosen the unique combination of tailormade scrubbers and automation to drive sustainability at sea.
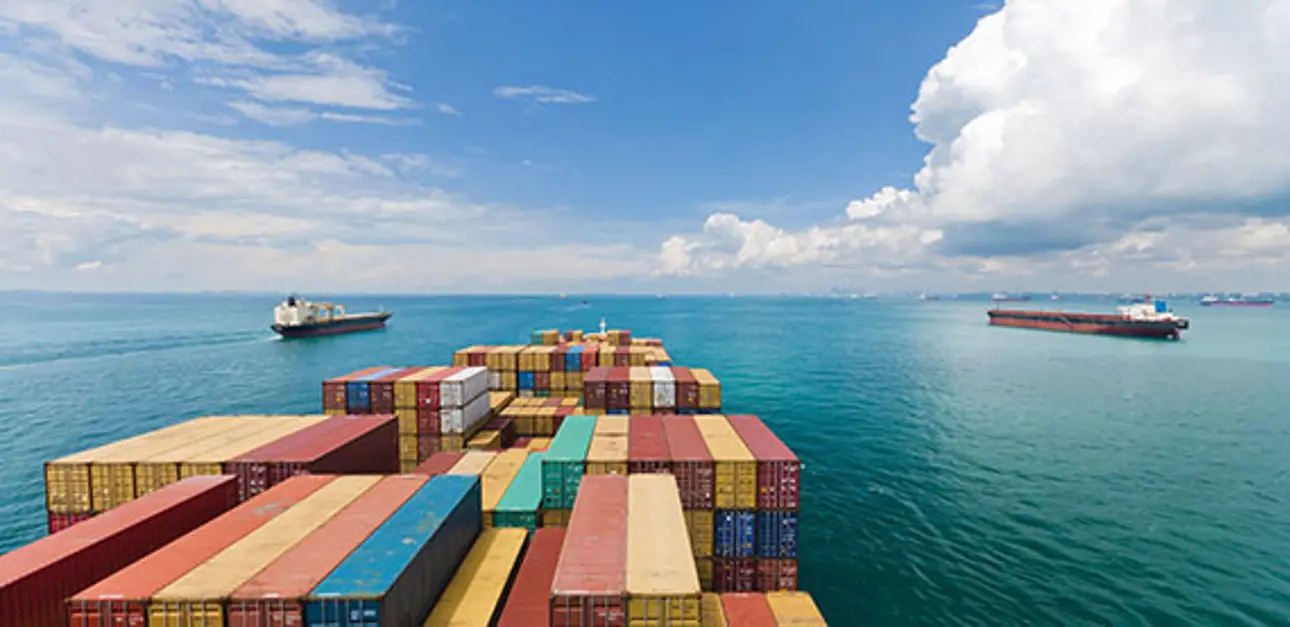
The Korean shipbuilding history is embedded in Geoje, in the South Gyeongsang province. One of the most significant shipyards there is Daewoo Shipbuilding & Marine Engineering (DSME). It is the largest shipyard in the world, driving innovation to meet customers’ needs in the demanding marine business.
Largest container vessels ever
Thousands of vessels are built at DSME’s shipyard. The world’s largest container vessels are currently in production. Each of these seven vessels can carry 23,964 TEU (twenty-foot equivalent unit) containers.
Seong-Hyun Park, DSME’s Assistant Manager, Ship Machinery, Procurement Department, is clearly proud of their container vessel expertise. Such large container vessels have never been built before. They therefore need to be tailormade, with containers fitting perfectly in the correct place on the vessels. Valmet’s strength lies in the flexibility of its scrubber design. The shipyard has selected the U-type scrubbers, which means that they have their own bypass line.
Valmet’s scrubber system delivery includes hybrid scrubber systems for the main engine and generator engines, including auxiliary systems and automation. In the open-loop mode, the exhaust gas is washed with seawater. In the closed-loop mode, it is washed with recirculated water and alkali. All emissions are continuously monitored, and the complete exhaust gas scrubber system is controlled by Valmet’s proven marine automation.
A unique combination: scrubbers and automation
The integration of Valmet’s automation with the scrubber makes the delivery unique. It is a cost-competitive solution to get both from the same supplier. For instance, fewer engineering hours are needed, and information sharing between the scrubber and automation experts is easy.
During the construction process, risks in time schedules can be reduced when products come from the same supplier. Later, the vessel owner will need only one source for spare parts and maintenance. The single point of services will enhance customer service.
Local experts enhance the project
“In Korea, Valmet’s dedicated project engineers undertake the work,” says Keon-Yeong Yoon, Valmet’s Vice President for Automation in the Asia Pacific.
Seong-Hyun Park is very satisfied with the services offered by the local Valmet personnel. “They are helpful and are very familiar with the project. Their Project Engineer, Dong-Seon Kim, is the perfect contact to support us on a daily basis. He’s committed to improving the project’s performance,” he emphasizes.
Anssi Mäkelä, Valmet's Senior Manager, Sales & Technology, Marine Emission Control, adds: “The basis of our fruitful cooperation lies in the trust that has been created by working closely together. Our aim is to offer our expertise to customers. The key is knowledgeable resources, local people who speak the local language – and people who know the culture and are eager to learn new things.”
Tight time schedule for start-ups
As part of large projects, pre-inspection and factory acceptance tests (FAT) are also extremely important. They ensure that everything fits when installation is underway in the vessels.
The commissioning for the first vessel started in early 2020. The final delivery will soon follow. For seven vessels, the time schedule is well planned, and everyone needs to work together.
The complete exhaust gas scrubber system is controlled by Valmet’s marine automation.
Text Soili Städter
Photos Shutterstock and Soili Städter
Related articles