Tammervoima produces responsible energy from garbage bags
‘What a waste of waste’ is no longer valid in Tampere, Finland. In January 2016, Tammervoima Oy’s new power plant went into commercial operation and now turns garbage bags into energy. Valmet’s flue gas cleaning, condensing and automation technologies contribute to its efficient operation.
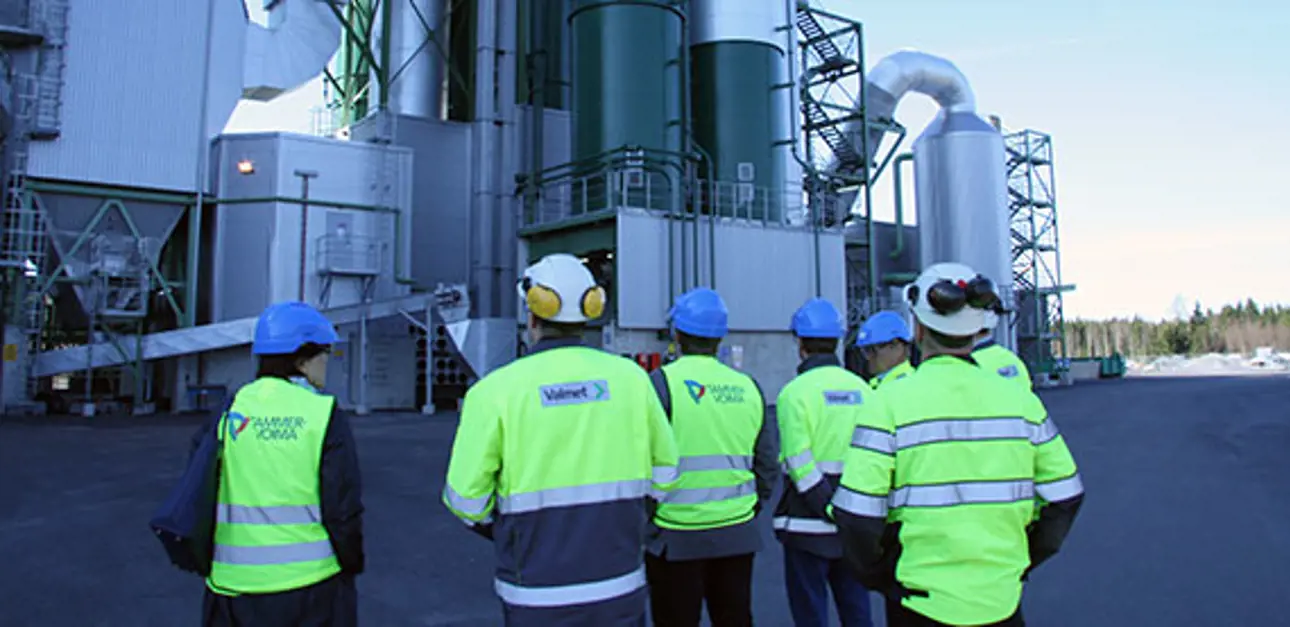
![]() |
||
The sound of a truck backing up and dumping its contents into a waste bunker can be heard approximately 80 times per day at Tammervoima’s new plant. About 160,000 tons of municipal waste annually is combusted in a 60 MW grate incinerator and turned into 310 GWh of heat and 90 GWh of electricity. The company is jointly owned by Pirkanmaan Jätehuolto Oy, a local waste management company, and Tampereen Sähkölaitos, a local energy company.
“We managed to build the plant in just two years and stay within the 111 million euro budget. Thanks to a speedy timetable, the plant was finished by the beginning of 2016 when the landfilling of organic waste was banned in Finland,” says Mika Pekkinen, Development Director, Tammervoima Oy and Tampereen Sähkölaitos Oy.
Waste incineration decreases the need for fossil fuels and lowers the climate load of energy production.
![]() |
According to Mika Pekkinen, Development Director, Tammervoima Oy and Tampereen Sähkölaitos Oy (second to the right), waste incineration decreases the need for fossil fuels and lowers the climate load of energy production. Pictured also Ari Pinjamaa, Vice President, EMEA North and East Europe, Automation, and Arto Mäkinen, Project Manager, Automation, both from Valmet. |
Efficient flue gas cleaning and heat recovery
Due to uneven fuel quality, emission limit values in waste-to-energy plants are tighter than in ones that run on other solid fuels. Efficient air emissions control is a must. “Our flue gas cleaning equipment has been designed for waste incineration. It is based on a semi-dry method and complemented by a condenser that recovers the remaining heat from flue gases,” Pekkinen explains.
NOx is reduced with the selective non-catalytic reduction (SNCR) method. Valmet delivered Tammervoima its GASCON™ flue gas cleaning technology, including a Valmet electrostatic precipitator for effective particulate capture. The plant’s semi-dry flue gas cleaning system is followed by a Valmet condensing wet flue gas scrubber that removes any remaining impurities and recovers energy in the flue gases that otherwise would escape into the atmosphere. This ‘free’ heat adds to district heat capacity. As the condensate from the scrubber is used as process water, there is zero wastewater.
The nominal capacity of the condensing scrubber is 8 MW. According to Pekkinen, it is run based on the plant’s need for process water, usually at 4–5 MW.
“The flue gas cleaning equipment functions very well: almost all our emissions, excluding NOx, are less than 10% of our emission limit values. In choosing the equipment, we had the tightening emission requirements in mind. The next time when we update our environmental permit, we don’t have to do anything with the flue gas cleaning process,” Pekkinen says.
Same automation platform as in other plants
The plant is operated with a Valmet DNA automation system. Valmet’s delivery included a boiler safety system as well as reporting, monitoring and emission control applications.
“From an economical point of view, Valmet had the most advantageous alternative in the public tendering process. Additionally, the Valmet DNA system is already widely used in other Tampereen Sähkölaitos plants, and the new system at Tammervoima supports our energy management system,” Pekkinen notes.
Delivered by Valmet in 2014 and integrated with the Valmet DNA automation and information system, the energy management system optimizes the utilization of the plants by taking into account the district heat need, electricity purchases and sales, fuel prices and availability of the plants. With the data collection, analyses, consumption forecasts and reports provided by the system, Tampereen Sähkölaitos is able to improve the efficiency of its production planning and make operations more economical in its power plants.
Tools liked by the operators
![]() |
![]() |
|
Janne Ahonen, one of the process operators, appreciates the analyses provided by the Valmet DNA automation system. | Jan Aarnimetsä finds Valmet DNA easy to use. “If something is wrong, you don’t have to look for it in many places. This makes troubleshooting easier.” |
Commissioning the automation system was smooth since all the operators worked earlier at the Tampereen Sähkölaitos Naistenlahti power plant and were familiar with Valmet DNA. Their tools to operate the plant include Valmet DNA applications for monitoring the performance of the boiler, steam turbine, heat exchangers, pumps and fans as well as for monitoring production, consumption, boiler fouling and operation point deviations in the boiler and steam turbine.
“We can do anything with this system. It’s the best!” says Janne Ahonen, one of the process operators. “I especially like the analyses; you can see what is changing and what is the average. And you can compare various process stages with each other.”
His colleague Jan Aarnimetsä likes Valmet DNA, too. “It is simple to use and you can easily find the information you need. If something is wrong, you don’t have to look for it in many places. This makes troubleshooting easier.”
According to Pekkinen, automation is an integral part of the plant. It is the tool to comprehensively manage, operate and optimize a complicated process. He continues: “In a waste incineration plant, the environmental permit requires that flue gases are measured and controlled online. In this plant, the measurements go directly into our automation system.”
The advanced Valmet DNA WI Emission Monitoring application enables effective authority reporting, but also serves the plant as an in-house operative tool.
Congratulations to Tammervoima on the smooth startup – and all the best for the future!
![]() |
About 160,000 tons of municipal waste annually is turned into 310 GWh of heat and 90 GWh of electricity. |