Success with the Valmet Acoustic Pyrometer at the Xinyuan Power Plant
The continuous measurement furnace temperature during the full load is a difficult problem. On the 700MW supercritical boiler furnace at the Xinyuan power plant in China this has been solved with the installation of a Valmet acoustic temperature measurement system.
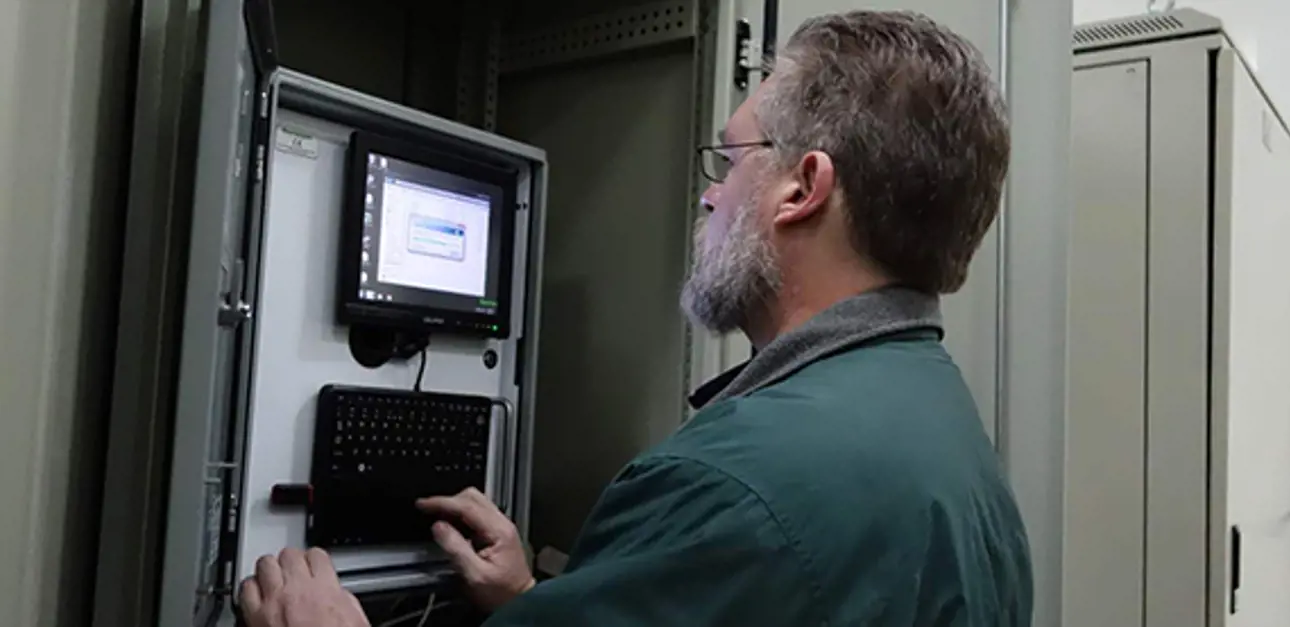
Boiler combustion optimization is the key to safety, energy conservation and emission reduction of thermal power plants. Traditional boiler-attached thermal flue-gas probes (one on each side) only work within 1 hour of powder dosing when flue gas temperature is less than 539℃, and the 8 to 9 meter long probes are very easily damaged while inserting and removing in the high-temperature furnace. With no reliable and accurate furnace outlet temperature monitoring system available during full load, damage to the boiler often occurs: for example, high temperature at the furnace outlet (>DT-50℃) leads to severe coking and slag fall; flame deflection causes abrasion and coking to one side of the boiler wall, large left/right deviations of superheated steam and overheated tube walls among other problems. In order to address these problems, the plant decided to trial the Valmet Acoustic Pyrometer on boiler #3 (700MW) after considering the many successful applications on other boilers in China as well as worldwide.
Reliable acoustic temperature measurement
It is well known that the speed of sound varies directly with the temperature of the medium through which it travels, and that changes in sound speed can therefore provide a direct measurement of the medium’s temperature. The Valmet Acoustic Pyrometer produces a high-energy sound wave (over 170 dB) using a unique patented pneumatic device and a receiver at a known distance to measure the time of flight and compute the temperature. The sound wave has a sharp leading edge that is propagated concentrically from the generator to enable accurately measure temperatures to within + 1% over a range of 0 to 1900 C, even in the presence of considerable noise. The measurement of gas temperatures is possible in furnaces over 30 meters wide and within sootblower lanes (up to 25 m), which was previously not possible. It also allows the use of long (up to 13 meter) pipes to deliver the sound to the desired measurement location, to permit mounting arrangements through windboxes and/or around obstructions without affecting the quality of the resultant measurement.
A typical furnace temperature measurement system. The acoustic waves sent by an acoustic generator can be monitored by multiple receivers which are easy to install requiring only a small hole of 12mm diameter in the wall.
The system utilizes 2 acoustic generators (ASG) and 8 acoustic receivers (ASR) to determine the temperature distribution in 16 zones of the furnace outlet. The 16 zone temperature information and a 2D temperature field distribution are presented on a control room screen for operating personnel to make the correct adjustments and optimize combustion conditions.
2D Temperature field distribution
High-sensitivity leak detection
The system can also distinguish the sound of furnace tube leakage from other sounds (such as soot blowing) by the comparison of the strength and time duration of the acoustic waves. to give leakage alarm in time, and thus the system also possesses the function of tube leakage detection.
Improved operations
After being put into operation, the system provided a large amount of data on furnace combustion conditions and flue-gas temperature distribution for the boiler operation and management personnel. The plant now has vital information at all load conditions to prevent excessively fast temperature rises during startup, too high temperatures at the reheater and avoids too high temperatures during normal operation to reduce superheater coke formation. The proper flame height can be determined and possible damage caused by flame deflection reduced.
Monitoring the temperature curve at boiler startup helps avoid undue thermal stress on boiler components.
Furnace temperature distribution data (normal operation). The temperature of the right rear zone is a little lower because when the five coal mills are running, the one placed at the right rear zone stops. As it is still within the allowable range no adjustment is required but still needs close monitoring under different load conditions.
Furnace temperature distribution data (abnormal operation). An abnormal temperature rise in the second zone on the left was observed. The temperature of the furnace upper left (at the outlet) is about 400℃ higher and noise also rises on the left indicating obvious deflagration due to incomplete combustion of coal powder. The flame at the outlet of the left burner was deflected leading to erosion and a coked left furnace wall.