Nonwoven business accelerates through partnership
Together with SharpCell, Valmet advances development of new technology for nonwoven quality control and automation. Establishing partnerships for co-creating is an important element of business development. SharpCell, an expert producer of air laid nonwovens, has joined the effort. Together we are testing how Valmet’s advanced automation solutions widely used in pulp and paper can be applied to nonwoven process and exploring further development for nonwovens.
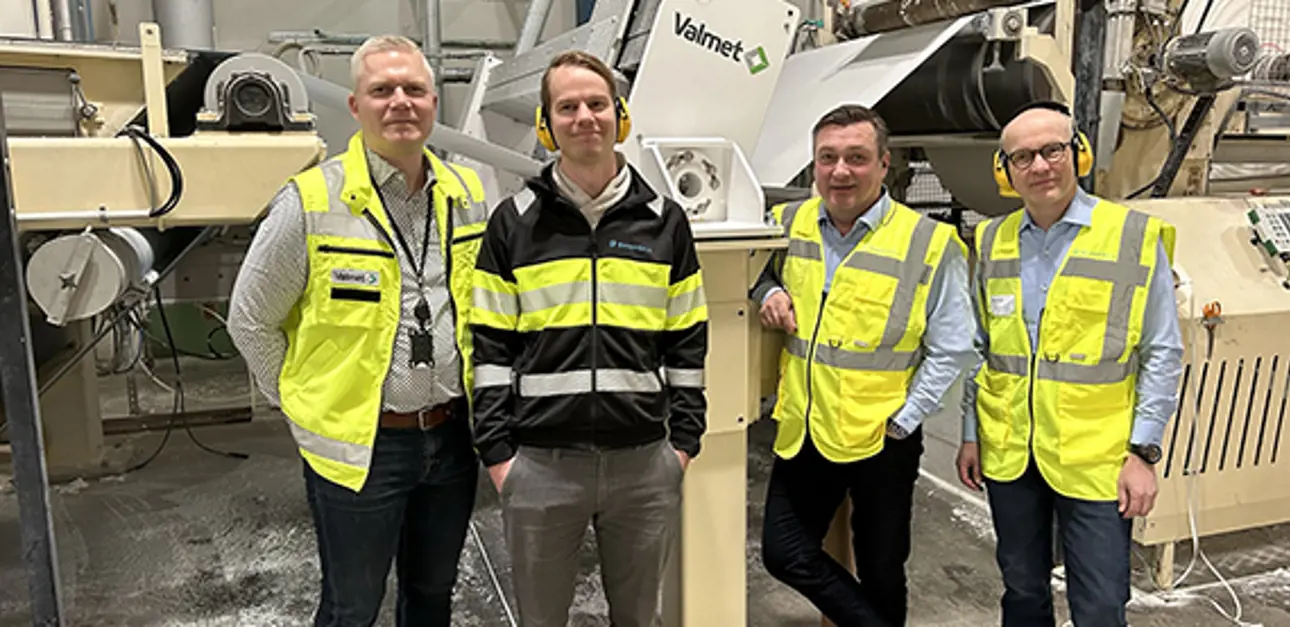
Co-development to meet new demands
“Valmet is a great partner because they can do everything, from machines to software algorithms,” says Jouni Lehtonen, Director of Marketing and Development at SharpCell.
“Nonwoven suppliers who can contribute to all aspects of the process are very rare,” he continues. “When we heard Valmet is interested in developing their offering for our industry, we wanted to get involved. Our goal is to establish long-term partnerships, and we are looking forward to what we can accomplish together with Valmet.”
“This is a true win-win,” agrees Mikko Talonen, Business Manager at Valmet Automation. “Valmet has the measurement and control technology know-how, while SharpCell has the process insights. Both of us can gain knowledge and new opportunities out of the partnership.”
Valmet IQ Scanner S gets a tough test
The partnership with SharpCell kicked off in earnest this year with the Valmet IQ Scanner S to measure basis weight and moisture using Valmet’s infrared sensor technology. This is the first industrial installation of the Scanner S, a new product in Valmet’s scanner portfolio engineered for nonwoven applications.
SharpCell was immediately impressed with the Valmet IQ Scanner S and its innovative design. The scanner is smaller and, thanks to its fully rotating design, supports more installation options than standard scanner.
As a first installation, SharpCell is an ideal setting. The very dusty air-laid nonwoven process environment is unquestionably demanding. Valmet will be able to prove the rubustness of the scanner from the very beginning.
Results deliver immediate savings
With their previous basis weight measurement, SharpCell struggled to get reliable, real-time measurements. The new Scanner S has changed the picture dramatically.
“It was eye opening for everyone to see how much variation there actually was in the process,” remarks Lehtonen.
Not only does SharpCell now get highly accurate and reliable basis weight, but with the same sensor, they also measure moisture. Adding moisture to their measured data set is very big step forward for SharpCell. The moisture level can be used to control temperatures in the drying phases.
Oven drying is the biggest energy consumer, so tuning the ovens to only dry as much as really needed leads to immediate costs savings. After just a few weeks, SharpCell was able to achieve 20% drying energy savings and more stable end product qualities.
Next insights eagerly awaited
The Valmet IQ Scanner S supports up to three sensors, and everyone is eager to add more measurements. Caliper and surface topography sensors are next in line to help optimize calendaring
Nonwoven customers pay particular attention to caliper. Serviette packages, for example, need to be just right – not too loose and not too tight. Caliper can also impact the quality of the printed surface.
Through better calendaring, SharpCell aims to achieve optimum thickness and a better understand surface properties. This will help them deliver improved and more stable quality to customers and end users.
Another essential are for better quality and savings is composition. Nonwovens are typically a complex multifiber product. Controlling the amount of each fiber type and the binder that goes into holding the web together is a certain optimization path.
Valmet will measure the entire makeup of SharpCell nonwovens using IR Spectroscopy, a significant departure from traditional IR measurements. This measurement data feeds advanced automation controls to fully optimize use of binder and raw fibers.
Advanced measurements tackle real-world challenge
A reliable online formation measurement and corresponding index is a high priority for nonwoven automation. Uniformity across the entire web is one of the key control parameters and plays a central role in the quality of end-product characteristics such as embossing.
Today quality is largely based on look and touch (hand-feel). End users have perceptions about softness, for example, that are not easily captured. Having data that explains why one formation produces a different quality perception than another would be a game changer.
“Valmet’s surface and formation measurements and tools are excellent for embossing development,” says Lehtonen. Topography details can help by giving nonwoven producers insights into which geometries deliver best, for instance, in terms of longevity, absorption and so for.
Positive nonwoven market outlook
In the air laid nonwoven market, the table-top sector is picking up after the Covid pandemic slowdown. “It’s quite surprising, actually,” says Risto Pollari, Vice President at SharpCell. “The table-top growth is expected to be very high, even though prices have also gone up.”
While the nonwoven capacity is growing, new demand is also coming novel applications. The agricultural sector, for example, is looking at reducing water and chemical consumption by using biodegradable nonwovens in layers to block weeds yet allow seeds to sprout.
“There are also extensive discussions around plastics in nonwovens,” adds Polalari, “examining where it is really needed versus where it can be removed or replaced with alternative sustainable raw materials.”
Use of PPE in nonwovens may be a bigger environmental issue than single-use plastics. Yet even if there are sustainable alternatives, it takes time to get them to market. They require changes to the entire end-to-end lifecycle.
Even more demanding is to get end users to switch to the non-plastic alternative. This is much harder than it sounds. “Even if our customers are excited about new sustainable options, market success can take time,” explains Lehtonen. “No matter how good the new product is, consumer purchasing behavior tends to change slowly.”
“If we want to take over new applications, we need to be more cost-effective and be able to deliver consistent quality,” he adds. “This goes for all players in the nonwovens business.”
For more information, please contact
Mikko Talonen, Business manager, Automation Systems Business Line
Mikko.Talonen@valmet.com