Mitsubishi Hachinohe optimizes recovery boiler performance
Along with improving recovery boiler efficiency, Mitsubishi Hachinohe Mill combats climate change through accurate online analyses and optimization.
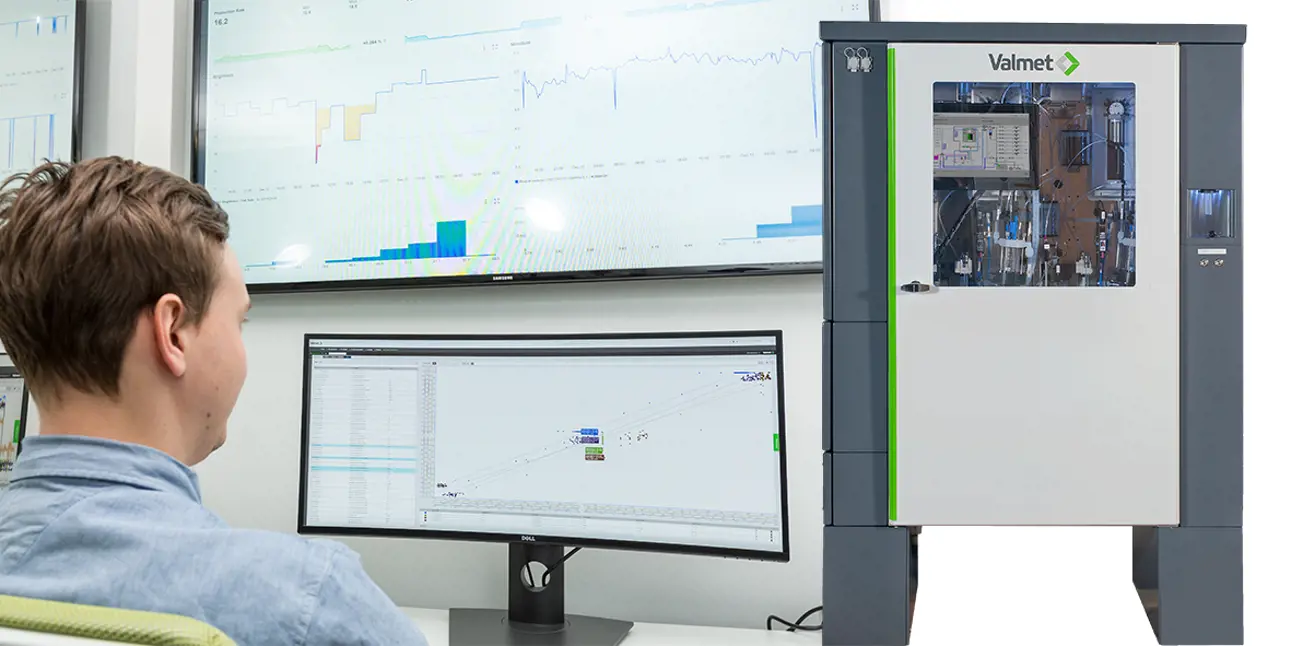
Mitsubishi Paper Hachinohe Mill, located in Hachinohe City, Aomori Prefecture, Japan, is Mitsubishi Paper Mills Ltd’s main mill. It produces 500,000 tons of fine paper and writing paper annually.
The mill wanted to improve the combustion and energy efficiency of its Recovery Boiler 4. “Although we had made some combustion improvement efforts in the past, overall air volume control had not yet been achieved, and the boiler was operating with excessive air volume, meaning the outlet oxygen concentration,” says Mitsuhiko Chiura, Raw Material Department Group Leader at Mitsubishi Hachinohe. “Better combustion would help us increase our steam production, reduce the amount of sootblowing steam consumption, and eventually decrease our use of fossil fuels.”
Better reduction performance and optimized processes
Of the many alternatives available on the market, the mill chose Valmet to provide the needed solutions to reach its targets on Recovery Boiler 4. “We selected Valmet because the company has a proven track record, and we could expect a high improvement effect through the additional analyses provided,” Mr. Chiura points out.
In June 2019, a Valmet Recovery Liquor Analyzer (Valmet Alkali R) with an advanced process control (APC) application, Valmet Recovery Boiler Optimizer, were started up in the mill’s chemical recovery process.
Valmet Alkali R provides tools to improve recovery boiler reduction performance with its unique online reduction degree measurement. It plays a major role in improving combustion, as optimizing the liquor chemistry reduces inorganic deadload throughout the liquor cycle. Reduced deadload means better black liquor heat value and reduced heat loss through smelt.
Valmet Recovery Boiler Optimizer controls the black liquor burning, air feeding, and furnace processes. Air feeding controls together with black liquor feeding controls form the basis for efficient furnace operation at the desired excess oxygen level.
“Valmet did exactly what we expected them to do, including startup and subsequent tuning. Valmet people responded promptly to our operational consultations and requests,” Mitsuhiko Chiura adds.
Reduction results beyond expectations
Mitsubishi Hachinohe invested in the Recovery Liquor Analyzer and the APC application with clear targets in mind. One of them was to reduce the variation of excess O2 concentration at the exhaust gas outlet by 35%. This target was indeed reached, as O2 variation was reduced by 78%.
Another target was to increase reduction efficiency to 95.0%. It is now 94.8%. Sootblowing steam consumption was lowered by 7.5%, even though the target was 5.0%.
“Optimization of the energy balance throughout the plant, lower costs through energy savings and efficient chemical recovery are the main factors for us papermakers to stay competitive. We need business partners that have the know-how and experience to achieve these goals. We appreciate that they can provide appropriate advice and support us,” says Mr. Chiura. “We are looking forward to Valmet providing us with products and services that can contribute to our process improvement, energy savings and decarbonization through the use of digital transformation.”
Related articles