Increasing quality and efficiency with Valmet’s automation and quality control at Mondi Ružomberok PM19
The Mondi Ružomberok mill, situated in the picturesque Liptov region of Slovakia, is a flagship facility in the Mondi network. The mill’s new production line, PM19, produces kraft top white, in a range spanning from 100 gsm to 200 gsm and an annual capacity of 300,000 tons – unmatched in Europe. One of the grades produced on this line is ProVantage Smartwhite, a completely new product on the market. This innovation along with increased production quality and efficiency was brought about through full automation integration, that only Valmet could provide.
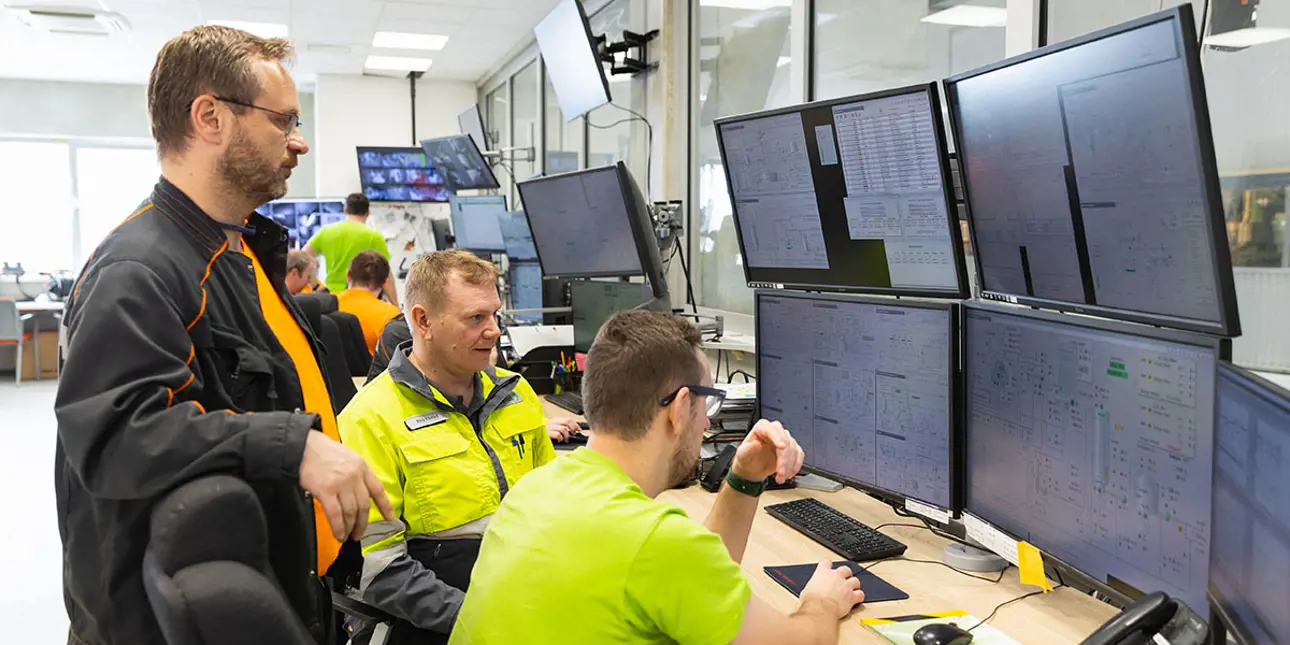
Looking for a fully integrated solution
Mondi Ružomberok, a long-time customer of Valmet, embarked on the PM19 project in 2020. Their primary requirement was a uniform control system for both the paper machine and the mill automation.
Marek Slamka, Automation Manager at PM19, recalls, “We approached several paper machine suppliers with this request. Valmet was the only one capable of delivering both the machine and the comprehensive automation solution. Their solution included a quality control system (QCS), condition monitoring, web monitoring, medium-voltage switchgear monitoring, energy monitoring and fully integrated drive controls. The additional integration of analyzers and Advanced Process Controls (APC) into one common system made Valmet’s offering unique.”
The integration meant that all control systems, from machine controls (MCS) to QCS and drives, were housed within a single platform – Valmet DNA. Such comprehensive integration ensured the mill’s reliability and simplified operations. But the ultimate goal was to achieve stable and reliable production with top quality and efficiency.
Swift startup for immediate sellable production
Throughout the project, efficiency and problem-solving agility marked the cooperation between Mondi and Valmet. “Valmet Technology and Valmet Automation engineers worked closely together for a fast and smooth startup,” Slamka says.
Despite the challenges posed by the COVID-19 pandemic which still affected travel at the time, Valmet adhered to the planned project schedule.
Mondi was able to produce market-ready products almost immediately after the startup, with top products following after a brief optimization.
“We reached sellable production within hours after the first start-up of PM19,” says Slamka. “And the automation system’s performance requirements were achieved very quickly.”
One system to control all
The project delivered exceptional operational efficiency. For the operators, comprehensive integration within Valmet DNA ensures that operation across all controls is smooth and effortless.
“Full integration of MCS, DCS, QCS, drives and APC into one control system offers the same user interface and interaction habits to all operators. This unique feature eliminates the need for interfaces from third-party systems, shortening training times. Now, different control tasks can be performed with the same skill level.”
“In fact, it takes only a couple of hours to get familiar with system operation. This allows the team to focus more on technology-oriented tasks,” Slamka continues.
Nearly 100% system availability
For Mondi, reliability was imperative. “An automation system should provide stable and reliable production. Valmet DNA fulfilled this requirement completely. It manages quality well. And with APC, it does even more,” says Slamka.
The system’s stability has been a standout feature, with no major downtime reported. Any control loop stability issues have been resolved swiftly, often within hours. “Valmet DNA had already been widely used in our mill, so our knowledge of the system was at a good level,” he explains. “Still, we have been able to reach a system availability rate of over 99%, with less than five hours of downtime per year – a remarkable achievement.”
Accurate quality management and efficient grade change
“Valmet’s quality management system has also proven its reliability. The accuracy of the system was verified by our laboratory, and it performs stably, fulfilling agreed-upon guarantees,” says Slamka.
Additionally, the grade change feature reduces the amount of rejected paper to just a few tons. This makes it easier to switch between different types of products without producing much waste, further contributing to greater efficiency.
Embracing advanced technologies and digitalization
Valmet’s new technologies and digital solutions, such as the Valmet Industrial Internet (VII), have further boosted effectiveness and quality at the mill.
“Implementing APC was a long journey but definitely worth it – and we are achieving promising results. APC offers fully automated control of selected quality parameters and allows us to considerably optimize production efficiency and quality,” Slamka observes.
The mill’s operators also praise Valmet’s single-point moisture measurement technology. “A tail threading in the sizing section of the paper machine requires a certain moisture level. Experienced operators are able to determine whether the moisture of the paper is correct or not. But with single-point moisture measurement, we can define the exact tail moisture without any guesswork,” he explains.
The VII tool offers extensive analysis capabilities. “It processes historical data from all integrated control and monitoring systems – along with laboratory results. This helps us find possible root causes of quality fluctuations,” Slamka says.
The role of automation in the mill’s strategic vision
Looking ahead, Mondi Ružomberok aims to establish itself as the market leader in its product segment. According to Slamka, ensuring stable production of high-quality products while minimizing costs is key to their future success. And automation plays a crucial role in achieving this balance.
“The main factor for staying competitive is to produce more efficiently while maintaining proper quality levels. Automation helps achieve quality targets while reducing energy demand and raw material usage. The more tasks you can automate, the more stable quality you can reach,” he says.
Another key factor is how automation enables people to perform at their best. At Mondi Ružomberok, the operators have been able to easily see the big picture and manage abnormal situations. They received thorough training from Valmet on how to operate the mill more efficiently and to optimize production.
“The one-user environment is intuitive and easy to use,” Slamka says. “It allows our operators to focus on the safest and most meaningful operations. “In addition, the advanced diagnostics and analytics allow them to manage asset performance better.”
Set for continued success
Collaboration between Mondi Ružomberok and Valmet has been marked by seamless integration, reliable performance and enhanced production efficiency.
“The project has been a success in terms of reaching our production stability and reliability targets,” Slamka concludes. Mondi is now well-positioned to continue leading in the efficient production of high-quality kraft top white.