Beating NOx emissions with optimized combustion
Pohjolan Voima’s values – skillfully, boldly and together – came to life when the company succeeded in reducing NOx emissions and improving energy efficiency through combustion optimization and data analyses at its two biopower plants.
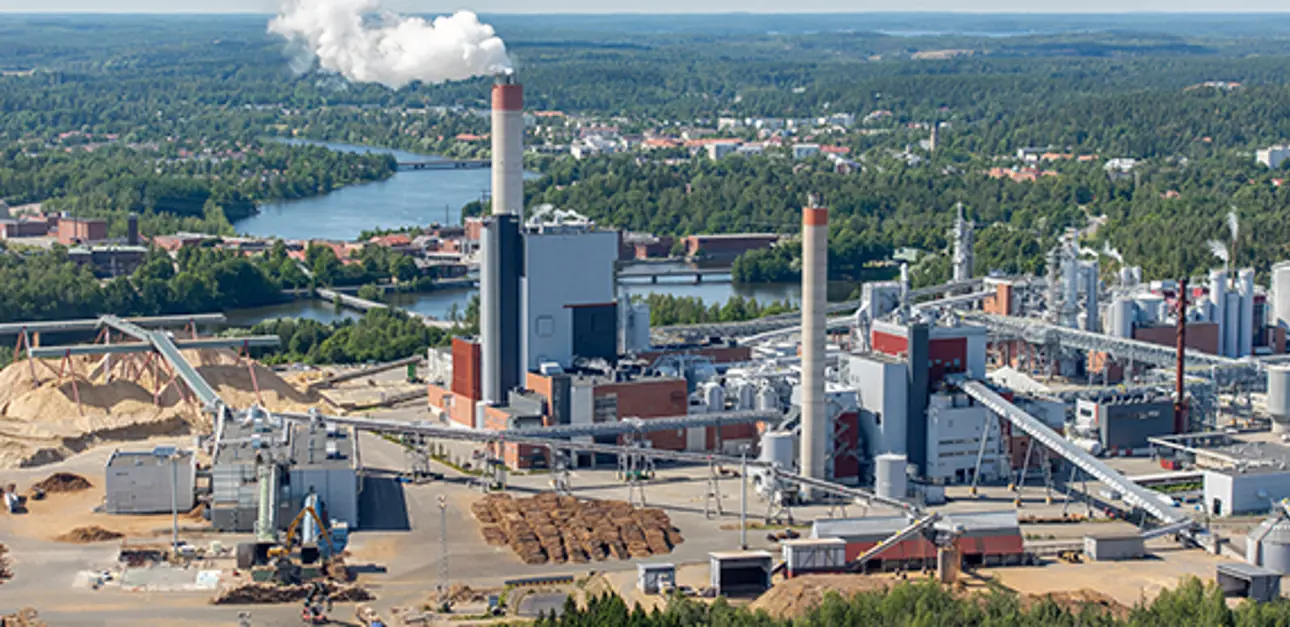
Pohjolan Voima, a major player in the Finnish energy sector, accounts for approximately 20 percent of the country’s total electricity production. At its 22 power plants, it produces electricity and heat for its shareholders – export industry companies, energy companies and cities – with hydro-, thermal and nuclear power.
With emissions limits tightening at the end of the Industrial Emissions Directive (IED) national transition period, the company had to find a way to reduce NOx emissions at two of its biopower plants, Kymin Voima in Kouvola and Kaukaan Voima in Lappeenranta, Finland. Additionally, at both plants the company wanted to improve boiler efficiency, and at Kaukaan Voima reduce ammonia consumption.
Focus on combustion management
Both plants produce process steam, district heat and electricity, and the main fuels are forest industry side streams and forest residues. Their fuel mixes vary according to the season. Kymin Voima’s boiler utilizes bubbling fluidized bed (BFB) technology. Kaukaan Voima’s boiler plant utilizes circulating fluidized bed (CFB) technology.
Kaukaan Voima power plant in Lappeenranta.
The customer understood that the technical challenge with emissions management actually lay in combustion management
The customer understood that the technical challenge with emissions management actually lay in combustion management. “The problem is often connected with fuel input. When the boiler furnace is wide, even as much as 10 or 20 meters, it’s challenging to feed the fuel evenly throughout the furnace. The bubbling sand in the furnace contributes to good combustion, but it isn’t enough. Changes in fuel quality and mixture add to the challenge,” says Managing Director Juha Kouki at Kaukaan Voima.
Advanced process controls optimize combustion
The solution for improving combustion management and consequently reducing the formation of NOx in the boilers was developed in close cooperation with Valmet. After a process improvement study in the fall of 2018, Valmet DNA Combustion Manager, an advanced process control application for optimized combustion, was installed in the plants’ existing Valmet DNA Automation.
Control room at Kymin Voima biopower plant in Kouvola. Advanced controls at both plants of Pohjolan Voima have made operators' work easier and freed up their time or other tasks from manual control.
Advanced control technology ensures even fuel input at all times.
The advanced control application manages the combustion process against variations in production, fuel amount, fuel quality and combustion circumstances, based on fuzzy logic, measurements and measurement data. Advanced control technology ensures even fuel input at all times.
“The most significant improvement is more even fuel combustion throughout the boiler. The oxygen level after the furnace can be more accurately controlled and thus reduced too. In turn, this reduces the amount of flue gases and enables better carbon monoxide control. Combustion staging also improves, contributing to lower NOx emissions,” Managing Director Antti Rainio at Kymin Voima points out.
The long list of other benefits includes a reduced requirement for combustion air, which reduces the need for auxiliary electricity, improving power plant performance. The lower amount of flue gases improves boiler efficiency. Power plant energy efficiency improves, because more heat and energy can be produced with the same amount of fuel. Heat losses also decrease, because less heat goes to the stack from a smaller amount of combustion air.
Lower chemical consumption
Thanks to combustion optimization, there is now no need for Kymin Voima to invest in an ammonia injection system at all. “We’ll be able to keep emissions below the upcoming tighter limits with our present technology and more accurate controls, as well as by reducing the use of NOx-containing fuels such as peat,” adds Antti Rainio.”
At the Kaukaan Voima plant, NOx emissions were previously controlled mainly with an ammonia injection system. Thanks to more accurate control technology, it has been possible to reduce its use and consequently save costs through lower chemical consumption.
An additional bonus is that advanced controls at both plants have made operators’ work easier and freed up their time for other tasks from manual control.
Photos: Hannu Vallas and Kai Tirkkonen
For more information, please contact:
Tiina Stenvik
Director, Performance Solutions, Valmet
Related articles