Valmet’s 1,000th Black Belt shoe press belt: A real success on Palm PM 6
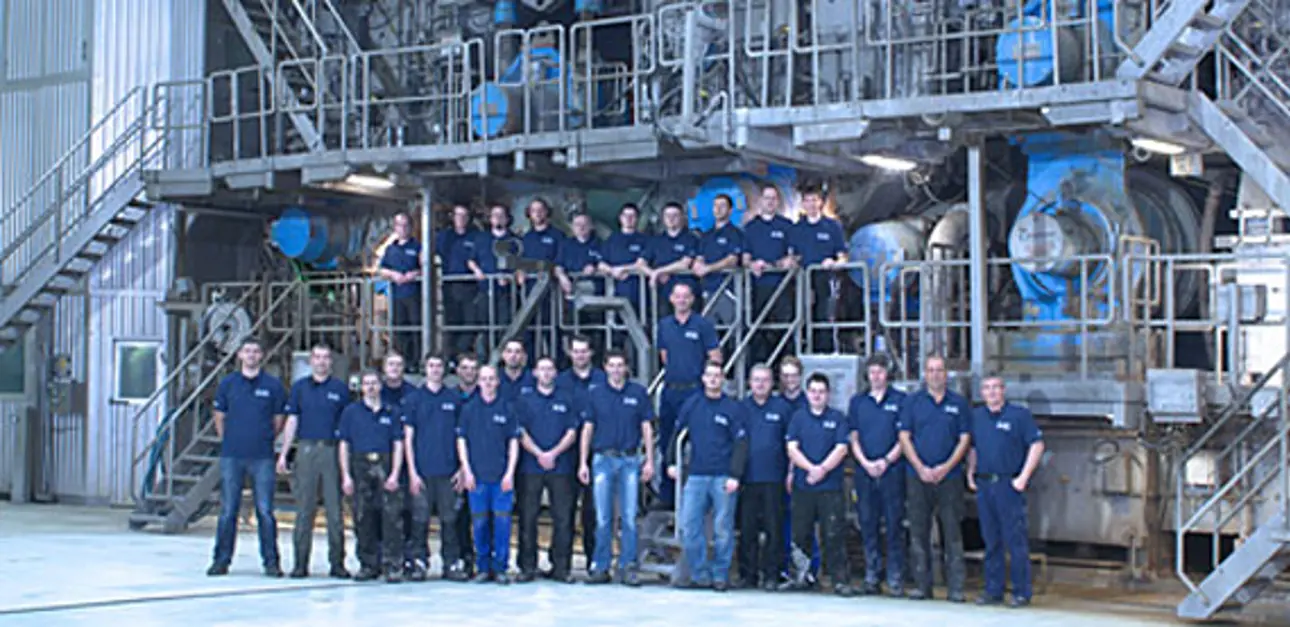
PM 6 of Papierfabrik Palm, Wörth, Germany, together with its machine crew.
“Absolutely, yes!” The answer given by Jürgen Kosse, Mill Manager, Papierfabrik Palm GmbH & Co. KG, in Wörth, Germany, to the question of whether Valmet's Black Belt shoe press belt achieved the targets it was set leaves no room for interpretation. “First, the product offers excellent performance. Its various properties contribute to a consistent, smooth run of the paper machine. Belt performance is absolutely constant from beginning to end, and the belt improves press performance.”
![]() |
Valmet Black Belt’s excellent material mix, long lifetime and good dewatering capability are the product highlights according to Jürgen Kosse, Mill Manager at Palm Wörth. |
In July 2013, the mill installed two Valmet Black Belt shoe press belts on PM 6: one in the first press and another in the second press. The first was the 1,000th Black Belt delivered by Valmet, and it ran from July 2013 to January 2014 – almost 200 days. The second belt ran from July 2013 to October 2013. “The paper machine’s performance was very good, and we got a perfect dewatering profile before and after the nip. The dry content after the press increased, and the moisture profile after the press was excellent,” Kosse says.
Kosse names Valmet Black Belt’s excellent material mix, long lifetime and good dewatering capability as the product highlights. “The dewatering process in the nip area looks perfect. The most important properties in a good shoe press belt are stiffness and hardness.”
High belt performance needs teamwork
As a paper producer, Palm wants to utilize the latest technological innovations in order to give its customers excellent-quality products and reliable service. The principles for the cooperation and success of this independent family business are its openness and honesty. As a customer, the company sticks to the same principles with its own suppliers.
“We expect good communication with our clothing/shoe press belt supplier, steady advances in all products as well as research and development for the customer’s benefit,” Kosse states. The mill also appreciates cooperation in troubleshooting and finding successful solutions to all kinds of problems. Responding rapidly to emergency cases and taking care of the relationship are also highly prized.
The 1000th Valmet Black Belt shoe press belt on its way into the machine.
“We think Valmet is a perfect partner in research and development. We have received complete support in every situation, and our wishes and requirements have been taken into account at all times. Our successful relationship is in line with our principle of working together.”
According to Kosse, the relationship between machine crew and supplier is very important. “The parties have to share their experiences with the product. The machine crew has to tell the supplier how the product works in their daily process, and the supplier must provide development ideas and benchmark belt performance with other machines. Finding solutions takes teamwork.”
Clear plans to optimize the whole process
Since the PM 6 start-up, cooperation between Palm and Valmet has been close, and the mill is looking to the future with optimism. The mill manager continues: “We are going to optimize our process from the wet end to the winder and increase the output of PM 6.” There are clear plans for the PM 6 press section and the shoe press position in 2014. They include using different felts, improving the work with the steambox, getting better profiles after the press for perfect paper quality and good performance, increasing the dry content after the press and improving the dewatering relation between the first and the second press.
While happy with the performance of the Valmet Black Belt shoe press belt, Palm has high expectations for the future development of belts in general. “We expect a long running time. On the other side, we need consistent, smooth belt performance. We have to optimize the dewatering process in the nip, and maybe we will do some research into new materials,” Kosse remarks. “Another point is energy consumption. If it is possible to increase the dry content after the press, steam consumption will drop. Working together with Valmet, we’ll find solutions, and both sides will improve their engagement in the coming years.”
Valmet Black Belt shoe press belt
|
Papierfabrik Palm is one of Europe’s leading paper industry companies. Founded in 1872, it specializes in producing newsprint paper and paper for corrugated board. Palm Wörth is home to PM 6, which Valmet supplied in 2002. It has a capacity of 650,000 tonnes of paper for corrugated board made from recovered paper (OCC). PM 6 is one of the most efficient paper machines in the world, breaking three world speed records so far. |
Originally published in Forward customer magazine 1/2014