Successful QCS migration leads to second system ahead of schedule
Faced with replacing an aging quality control system on board machine 3, Ningbo Zhonghua Paper selected Valmet* because of its innovative sensor technology, especially the direct coat weight measurement. The results were so good that within a year they replaced a second quality control system on BM2 ahead of schedule and report being very satisfied with both deliveries.
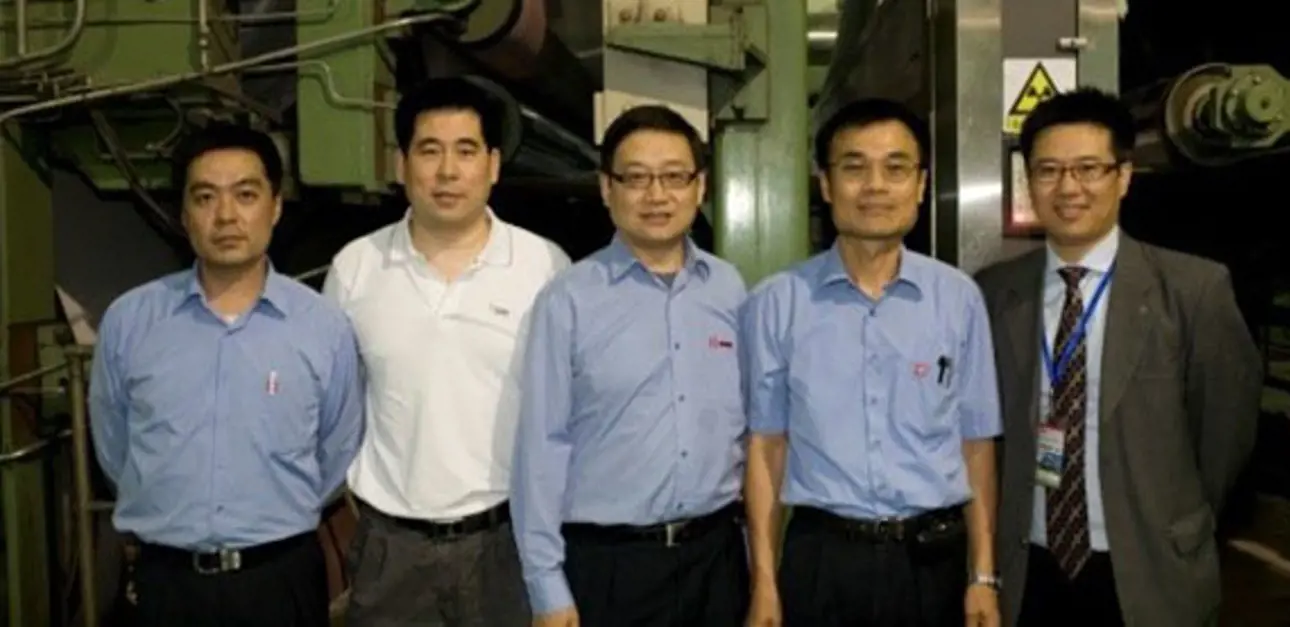
APP China's Ningbo Zhonghua Paper Co Ltd is one of the largest manufacturers of white paperboard in China. Established in July 1992, the mill is located in the Haishu Industrial Zone, Ningbo, Zhejiang Province, with three board machines producing a variety of high quality coated white board amounting to 500,000 tons annually. As well as virgin fiber, Ningbo Zhonghua Paper collects and uses recycled newspaper, office paper and magazines as its main source of raw materials. In 1999, the mill was the first paper making enterprise in China to achieve ISO 14001 Environment Management System Certification. The successful in implementation of an eco-friendly and sustainable economic model helps to keep the environment clean as well as promoting conservation and recycling of resources.
Aging QCS needed replacing
Board machine 3 with a trim width of 4.27 m running at 600 m/min was started in 1997. Recycled paper is the main source of furnish for the 4-layer sheet, the top layer being made of chemical pulp, and the other layers of deinked waste paper. The machine is equipped with four coating heads, allowing dual coating on both sides. After 14 years, the original quality control system needed replacing as spare parts were getting difficult to obtain. Additionally the mill needed a more accurate measurement of coat weight. With no space for scanner frames between the first and last two coaters, the traditional oven dry method, based on moisture and basis weight, could not determine the coat weight of each layer separately. Coat weight control was a matter of guesswork and for the top layer, especially difficult. Several QCS suppliers were invited to the mill to discuss replacing the QCS and especially alternative technology for the coat weight measurement problem.
Selective coat weight measurement
Lin Zheng, Deputy Manager of the Electrical and Instrument Department says, “It was a big surprise when Valmet showed us a direct coat weight measurement. This sensor provided all the reasons to invest in the Valmet IQ quality control system.” Using Valmet’s patented technology, IQ Coat Weight enables the selective measurement of coat weight more accurately than previously possible.
Fast startup
Two mill engineers had attended the factory acceptance tests in Finland prior to the delivery and two Valmet specialists from Tampere were at the mill for installation and startup. SJ Lin, Engineering and Maintenance Director says, “Valmet were very helpful before the shutdown, they made two visits to help plan the careful removal of the old frames, which we intended to keep as spares for BM2. The shutdown itself lasted just 40 hours to install the four new Valmet frames with 21 sensors.” Ning Zhu, Valmet’s Automation Business Manager commented, “With the mill’s strong mechanical and automation capabilities, we worked as one team with one target.” After the restart, the fourth jumbo reel was already to specification and saleable. The results were immediately impressive and after only six months the mill decided on a repeat order for BM2. According to SJ Lin, “Our production people are really satisfied, the CD and MD controls are working really well and it is now very quick to set individual coat weights. The operator’s job is now much easier.” As well as quality, the Valmet IQ system contributes to better machine control, “ Valmet’s feedforward basis weight control also works extremely well as the operator can see the basis weight prediction during tail threading which makes it much faster to reach good production.” For Lin Zheng the bottom side color sensor performance has been particularly helpful in achieving higher production. “We also now have the slice control in automatic whereas before it was normally manual.”
![]() |
![]() |
CD profile paper samples taken before and after the QCS rebuild illustrate the improved CD profile (base board plus coat weight profiles) shown here in green, the ash profiles are a good indication of the coat weight profile improvement.
Second system ordered ahead of schedule
In 2007, BM 2 had been rebuilt to extend the product range to produce art board as well as ivory board. A fourth coater was added but reliance on the oven dry calculation of coat weight made life difficult for the operators, not being able to separate the measurements for layers 2, 3 and 4. Lin Zheng says that, “We had expected to wait at least another year but with correlations of coat weight on BM3 to plus or minus 1 gsm, Valmet was definitely the choice for BM2.” With the four coaters, there was no space in the coating section for a full scanner frame. But by moving a sheet break slitter, the mill and Valmet worked together to find space for a single sided frame to measure the back of the sheet between coaters 2 and 3. A second half frame provides the coat weight measurement on the top of the sheet between coaters 1 and 2 and enables the separation of each of the four coat layers on both sides for control. The installation and startup in early 2011 of 3 full scanners and 2 single sided scanners plus sensors was handled by Valmet’s local Shanghai engineering staff.
![]() |
Space for a single sided scanner frame was tight on BM2 |
Essential production tool
SJ Lin reports that they have been very happy with Valmet’s local service capability. For the first installation on BM3, 2 Valmet engineers stayed onsite for a month. Well into the learning curve with the second system, this onsite assistance was needed for only two weeks. Both Valmet’s service staff and spare parts are in nearby Shanghai, giving a short response time. According to Lin Zheng, “The QCS is now so important that it cannot be stopped, we even remotely monitor the cooling water to the frames from our offices.” Maintenance is simple, regular cleaning of the caliper sensors and scanner photocells being the only short term scheduled actions.
The operator’s views of caliper profile control on BM2 with the same grade before and after BM2 QCS rebuild. These two displays just three weeks apart show a 2-Sigma improvement from 2.7 to 1.61.
With one year of running on BM3 and a few months on BM2, Ningbo Zhonghua is very satisfied with the Valmet IQ quality control system and especially the direct coat weight measurement. It has become an indispensable tool for the production of excellent products from what is definitely a world class board producer.
*Metso until April 1, 2015