Steinbeis PM 4 increases its production capacity
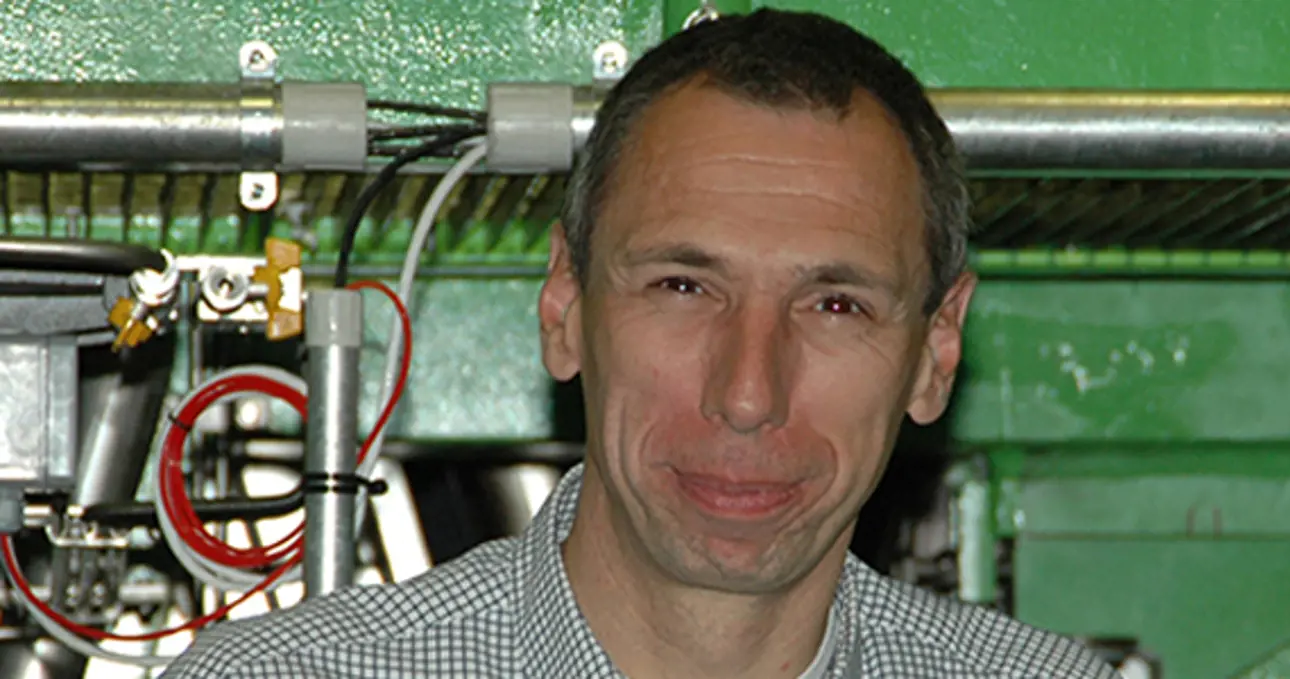
Doctor Michael Hunold (right), Production Manager at Steinbeis Papier says, “We are very pleased with the fact that the OptiDry Vertical dryer achieved the guaranteed drying capacity so fast and that the start-up was so easy.”
The German Steinbeis Papier paper mill needed more production capacity to better meet the needs of its customers and its PM 4 had a limited drying section. In spring 2008 the company studied the possibilities of increasing its drying capacity and instead of extending the machine length they decided to invest in Valmet’s solution – the OptiDry Vertical impingement drying technology. With this dryer there was no need for major changes in the dryer section. The OptiDry Vertical can be installed in an existing dryer section without increasing the machine length, and with a minimal rebuild of the current dryer. In many cases this is the most economical way for dryer enhancement – and often the only way.
Why choose Valmet and the OptiDry Vertical impingement dryer?
Doctor Michael Hunold, Production Manager of the Steinbeis mill replies: “Valmet’s OptiDry Vertical solution is a very intellectual combination of well proven components, e.g. air dryers, blow boxes and rolls in a new mode. The solution was very attractive due to the drying capacity increase without having to increase the machine length. We also wanted the shutdown to be as short as possible to be able to fulfill our customers' needs. Now I can say the investment decision was the right one.”
The rebuild was scheduled for May 2009 with only 14 days shutdown time. The installation schedule was tight but the start-up already took place on the 12th day and the machine started producing saleable paper right from the first day. The impingement dryer was able to be in continuous use shortly after the start-up. The implementation of OptiDry was smooth and successful. The guaranteed drying capacity was quickly gained and the new dryer now provides enough drying capacity for a 15 % production increase and about 175 m/min machine speed increase. The paper quality is as good as before the rebuild and the investment has already proven worthwhile.
How were the project, installation and start-up handled by Valmet?
Production Manager Dr Hunold comments: “Installation was well organized. We are very pleased with the fact that the OptiDry Vertical dryer achieved the guaranteed drying capacity so fast and that the start-up was so easy. We made saleable paper right after the start-up. We are very satisfied with Valmet’s performance in this project. OptiDry Vertical gives us possibilities to look further to the future. This really was the right solution for us.”
High drying capacity with high energy efficiency
The OptiDry Vertical impingement dryer is a rebuild concept which adds drying capacity in the drying section, thus enabling a production and speed increase without additional dryer cylinders. It consists of two dryers that blow hot air directly onto the paper. The drying process is optimized by controlling two parameters – impingement air velocity and temperature. Drying by very high air temperatures gives 2 to 3 times more drying capacity per dryer square meter than traditional cylinder drying.
OptiDry Vertical impingement dryer is a rebuild concept that increases drying capacity in the drying section without additional dryer cylinders.
The OptiDry Vertical impingement dryer is a solution in which the environmental aspects were taken into consideration during product development. Gas burners were chosen as they have the lowest environmental impact when burning gas. Efficient dryers equipped with a heat recovery system means that the environmental load caused by heat generation is reduced to the minimum. This effectively supports Steinbeis Papier’s sustainable way of operation.
How is the equipment working?
Production Manager Dr Hunold states: “Our main concerns before the start-up were ropeless tail threading and runnability. And now I must say that the tail threading has been the best thing. There were absolutely no problems and it has worked well right from the first try, and the same goes for runnability. The OptiDry Vertical dryer has successfully fulfilled our needs for capacity increase.”