Sappi Kirkniemi relies on Valmet
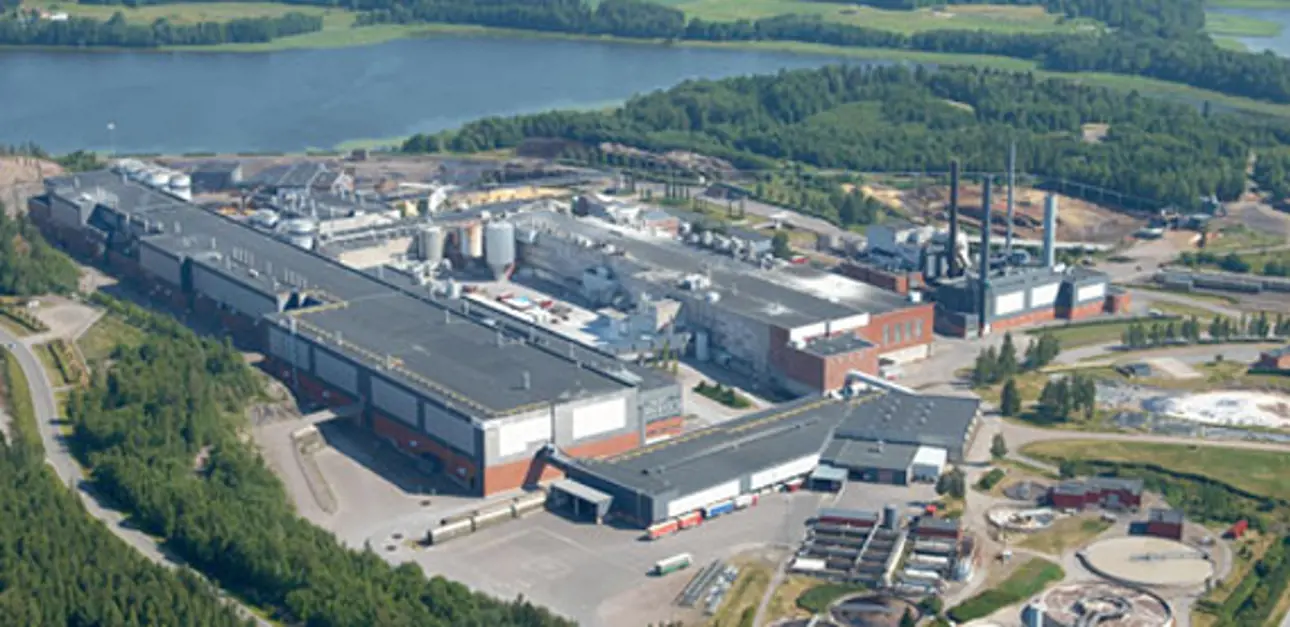
In common with many industries, the pulp and paper industry faces major challenges in improving the economics of their operations. As new technology, equipment and automation provide the tools to improve production, papermakers are seeking other ways to release money and resources to concentrate on their core business of making paper. Sappi’s Kirkniemi mill in Finland is no exception and has been quick to take advantage of Valmet’s (until Dec. 31, 2013 Metso Paper) skills and expertise to maintain critical machinery and secure production line availability.
The Kirkniemi mill, located in southern Finland, 70 km west of Helsinki, started in 1966 with one paper machine and today produces 730,000 tonnes per year of coated papers with three machines. The mill has a well-known track record in product innovations resulting from cooperation with customers as well as machinery and raw material suppliers. Valmet has been a valuable partner since the beginning, supplying paper and stock preparation machinery as well as automation. At the beginning of 2012, Valmet’s relationship with the mill entered a new phase with the start of a frame agreement covering various services and spare parts for the three papermaking lines. An existing program for suction roll seals utilizing the innovative Valmet Seal Strip Flex1, had already provided evidence of the opportunities for wear part inventory savings, and further opportunities were recognized. After two years, the mill has been very satisfied with the durability, availability and cost of Valmet Seal Strip Flex.
![]() |
Leo Järvenpää, Mill Maintenance Engineer: "This kind of service from Valmet is so effective it makes no sense for us to try to do it ourselves." |
A question of skills
“We need Valmet’s expertise, especially in the maintenance of tail threading equipment. We have our own maintenance department but the skills needed are not available in-house and are only utilized during major maintenance shutdowns on a yearly basis,” says Leo Järvenpää, Mill Maintenance Engineer. PM 2, producing coated (LWC) magazine paper under the brand name Galerie Brite, is a typical case. In June 2007, Valmet had installed its 1000th state-of-the-art Valmet Tail Threading Belt2 unit on Kirkniemi’s PM 2; the mill was already familiar with the technology having similar systems on the other two machines. This challenging project was to replace the former guide plate-based tail threading and to pick the sheet tail up at the last dryer cylinder to carry it all the way to the calender and reel. The primary goal of the project, to improve the operational reliability and safety of the tail threading process was met. June 2008 saw the twin-fabric area of the machine’s dryer section upgraded from rope-assisted to the latest Valmet Tail Threading Double Fabric3 system. At the time, break times were reported to have been cut by 35% and with one year of operation, tail threading double fabric had not needed any servicing. Very reliable equipment is a two-edged sword for a mill maintenance department, as having equipment you can forget about means that members of the maintenance department are not familiar with the equipment, if and when this is necessary.
![]() |
Valmet Tail Threading Double Fabric units thread the sheet tail through the machine with the help of compressed air. |
A solution that is easy to work with
The tail threading maintenance agreement with Metso combats the problem of unfamiliarity with reliable equipment. “In future, Valmet will perform an audit of the automated tail threading on all three machines and present us with a maintenance plan for the next shutdown and suggestions for other improvements. They use our tag numbers so they are very easy to understand,” says Järvenpää. A fixed price for the service crew from Valmet and availability of spares from Valmet’s nearby Kerava warehouse provide an easy solution to the yearly maintenance shutdown and guarantee the availability of the automated tail threading equipment. Emergency service with short response times is also covered in the agreement, making the right skill set and equipment expertise available when needed. “This kind of service from Valmet is so effective it makes no sense for us to try to do it ourselves, and we are also confident that we are applying the latest technology as Valmet keeps the systems up to date,” says Järvenpää.
Valmet’s Kirkniemi frame agreement covers• Valmet Seal Strip Flex |
Inventory savings
An important area of savings is in reducing the mill-owned stock of spare and replacement parts, as they are “eaten” from the mills own inventory. Valmet guarantees availability from the Kerava service stock. The agreement also covers refiner and deflaker shaft units and loading devices, a perfect example of the possible inventory savings. These replacement units would previously be held in the mill’s own spare part stock for literally years before being needed at very short notice. As well as the non-earning expense to the mill, the condition of long-held units was always questionable. Now, the mill can rely on fast delivery on demand of replacement units, as well as spare parts, from Valmet. Previously-stocked units are used as needed with Valmet purchasing exchanged units for later use. Valmet's task is to keep the required number of parts in stock at all times. With 19 refiners and 5 deflakers to look after, mill inventory costs will be drastically reduced and the condition of replacement shaft units and loading devices is assured.
Better planning
“Overall, the service agreement with Valmet allows us to plan better, sometimes years into the future and reduce maintenance shutdown surprises,” says Järvenpää. “Service is done properly and as agreed with fixed pricing, and any other major actions identified along the way can be planned now we know what to expect.” Service planning can now be done for all three machines, taking advantage of common actions when Valmet service personnel are on site. “Valmet knows our machines and the way we work, which makes things easy. Operators log any problems into our SAP-based maintenance system and Valmet personnel familiar with the mill know exactly where to go.” With the first major shutdown in the agreement, Valmet will first perform the audit and provide the mill with a comprehensive report of planned actions and cost. Then, well prepared and with the necessary parts, a Valmet service team will be ready to ensure the tail threading equipment continues to deliver fast and trouble-free recovery from infrequent breaks for another year.
1 earlier known as FlexSeal
2 earlier known as FoilForce1
3 earlier known as TailDoc
4 earlier known as WinBelt belts