Recausticizing filter fabrics on top of the game
Innovative recausticizing filter fabrics are the result of demand in the pulp industry.
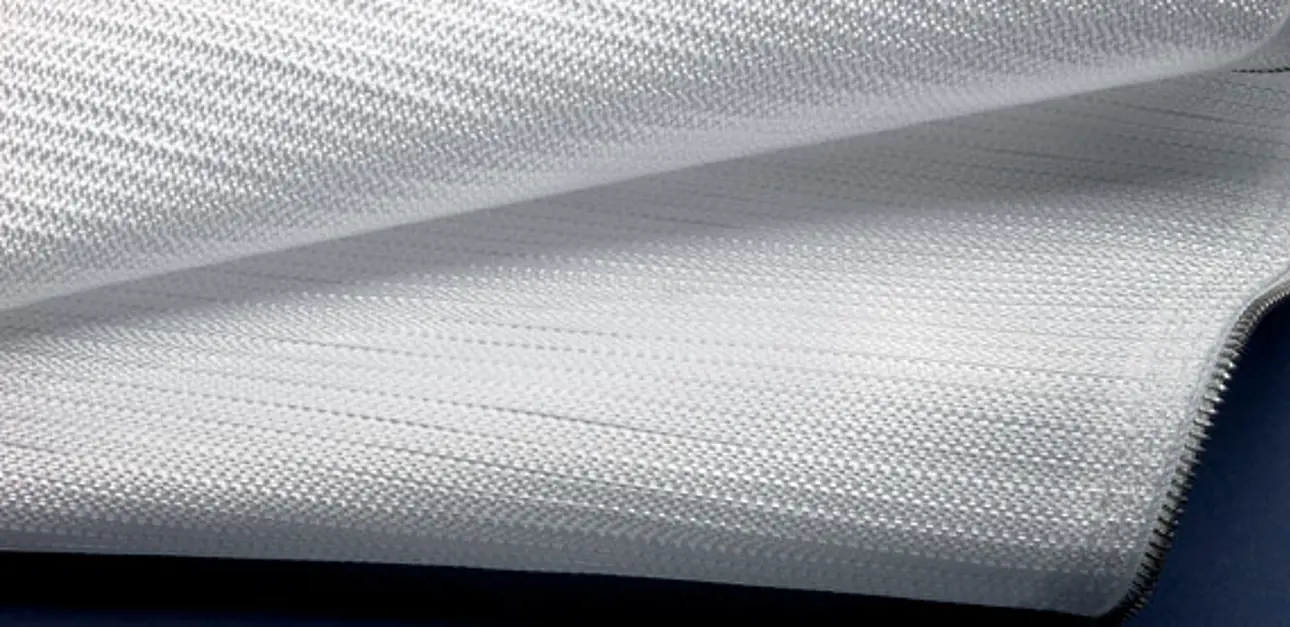
When a pulp mill customer invests in recausticizing equipment, Valmet’s filter fabrics are most probably doing the dirty work. With a unique chain of in-house R&D, laboratory testing and its own production, Valmet is the leading developer and manufacturer of recausticizing filter fabrics. “Our expertise starts from the premise that we have always collaborated with leading filter suppliers globally, spreading and cultivating know-how within the industry,” explains Antti Mäkinen, Senior Sales Manager of Valmet. “This cooperation will continue. Our history includes many challenges and successes, but Valmet’s role as a supplier of superior-quality filter fabrics has not changed,” he says.
Effective recausticizing with filter fabrics
A variety of products and filters are used in recausticizing processes within the chemical pulping industry. The quality of filtrated green liquor, white liquor and lime mud depends heavily on the filter fabrics’ ability to effectively filtrate and recover cooking chemicals for further processing. “High demands for increased capacity with the existing machinery present interesting challenges for recausticizing filter fabrics,” says Antti.
Today, the most commonly used recausticizing filters are disc filters, alongside conventional drum and tube filters. A disc filter consists of around 200–300 filter bags and sectors. Each filter bag needs to filtrate lime mud and white liquor with a good clarity, as well as having excellent mechanical durability features. The bags need to resist extreme conditions: high process temperatures, exposure to harsh chemicals and mechanical stress. Above all, the filter has to achieve high filtrate clarity for excellent quality liquor.
“The starting point is to use the most suitable fabric structure for each application so that the best possible filtration results are achieved. The objective, of course, is to find the most cost-effective solution for the customer,” Antti explains. In the lime mud filter, one key factor is that the dry content of the separated lime mud needs to be ideal when it goes to the reburning process. If the amount of water is even a few percentage points lower, burning the cake in the lime kiln requires less energy. “A difference of 3% is enough to create significant energy savings for the mill,” says Antti.
Valmet is the leading developer and manufacturer of filter fabrics for all stages of the recausticizing process.
Many ways to save money
Customers expect a long filter fabric lifetime without any clogging problems that might lead to unnecessary maintenance. Antti explains: “An acid wash is a typical way of removing dirt particles to prevent them clogging the fabric. This means that the machine has to be stopped, production time is reduced, maintenance costs rise, and corrosive chemicals may wear out the fabric – all of which costs money. This, of course, is something all our customers want to avoid,” Antti explains, emphasizing operational reliability in filter fabric development. Valmet’s filter fabrics are always tailor-made specifically for each filter in the recausticizing process.
“Our goal is to minimize unplanned downtime. The right direction is found by listening to the customer already at the mill. Valmet’s advantage is our comprehensive ability to provide service locally,” Antti continues. Valmet is also the only manufacturer able to weave fabrics up to 12 meters wide for lime mud drum filters. “This means we can supply fabrics for all machines without any seams. A seamless filter fabric is many times more durable and wear-resistant, since it is not exposed to extreme abrasion.”
Up to 10% increase in filtration capacity
Traditional concepts are making way for a new generation of filter fabrics. The reasons behind this much-needed innovation are increased capacity requirements, heavier mechanical loads and common goals in finding easier and faster installation procedures that save time for customers.
“We have been able to respond to the changing expectations by optimizing existing filter fabric sections,” says Antti. Valmet’s research resulted in an innovation in recausticizing filter fabrics: a two-in-one integrated fabric for white liquor disc filters.
“Our challenge was to develop an improved product without compromising quality or reliability. We decided to concentrate on threads, materials and overall product features, which led to combining the filter bag and the underwire into a functional, integrated structure,” Antti explains. In the patented two-in-one structure, thick support wires are woven to the bottom side of the fabric, giving the single-layer filter fabric the same properties as two separate components.
“The sparse support wire structure hinders the fabric from full contact to the sector, increasing filtration capacity by up to 10%,” Antti says. Compared to conventional disc filter fabrics, the two-in-one structure is affordable and easy to install. “Our product development objectives are really captured in this product. We continue to lead the way towards more durable, effective and reliable filter fabrics. Valmet is the only manufacturer providing all the filter fabrics required in the recausticizing processes. Our products can be fitted with all filters available on the market.”