Propapier - 2,300 tonnes per day through one single OptiWin Pro winder
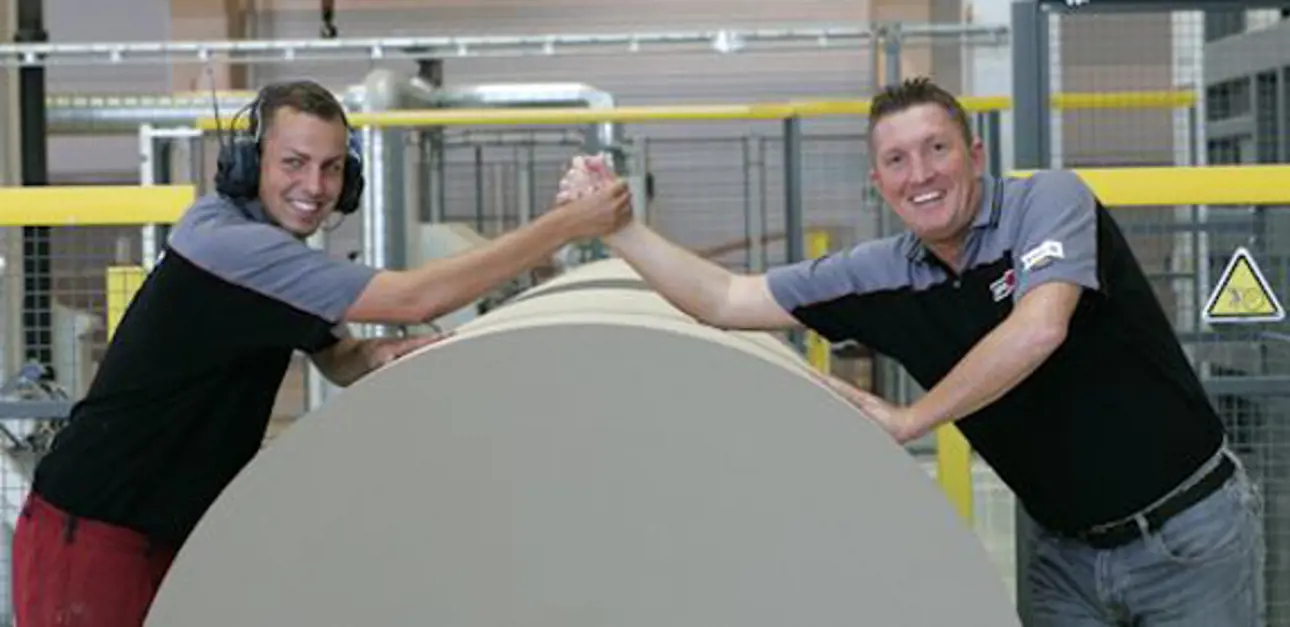
“We are very satisfied with the OptiWin Pro winder,” says Peter Resvanis (on the right) from Propapier. Diego Schwagerick shares his enthusiasm.
So for us, with the high-quality paper we can make on PM 2, it was an easy decision to use only one winder. It was also an easy decision to choose Valmet* ( *Metso (Paper) until Dec. 31, 2013) as there was no real alternative that we were comfortable with,” Propapier's Peter Resvanis states.
"Of course, not everything was simple,” admits Resvanis. “We were a bit nervous when PM 2 started up so incredibly well, as has been documented in other reports, and we had all these parent rolls coming at the winder so quickly. Normally you have time to learn about the winder because the PM start-up curves are usually flatter. But PM 2 was making paper within hours and A-quality 90 g/m2 testliner and fluting at high speed after only two weeks." “So we had to run the winder at top speed from day one and we learned as we went. Our excellent cooperation agreement with Valmet meant that all we had to do was snap our fingers and their very competent winder experts would arrive to work out the initial challenges together with us.”
Since start-up, PM 2 has continued to run extremely well, setting several world speed records, with the first being in November 2010 at 1,620 m/min for 90 g/m2 corrugating medium, with an efficiency of 94%. In April 2011, the next world record was set at 1,650 m/min for 80 g/m2. Resvanis says speeds are increasing all the time with 1,700 m/min in sight and 1,800 m/min being the ultimate target. And the OptiWin Pro (former WinDrum Pro) winder has kept up every step of the way.
The winder 'that does it all.'
Numerous features add up to high throughput
The numerous advanced technical features of the OptiWin Pro are helping it to keep up. Resvanis certainly appears well informed as he runs through the details of the OptiWin Pro technology. “There is the 15 second set change, the 45-50 second parent roll change, optimized acceleration/deceleration, the gap opening between the drums, two unwind stands, and a perfect core handling solution that includes core grooving. It also has very advanced vibration controls. So, it is not one single feature which makes the difference but all of these details which work together to give the high throughput. This allows us to run 2,800, 2,900, even 3,000 m/min on the winder, with no trouble. We require perfection and the OptiWin Pro provides it.”
Resvanis also says that they have very low downtime with a planned shutdown of about four to six hours per week for clean-up, and typically two or maybe three web breaks on the winder per day. Likewise, there are no problems with tension variation, knives or edge cutting. “Nothing,” he says simply.
Perfect paper coming off the line
Key factors in the ability to run so fast, explains Resvanis, are the paper properties and extremely flat profiles that PM 2 produces. Of particular importance are roughness, permeability and slipping angle. “PM 2 has given us an almost perfect sheet as far as profiles and properties. We have used these to run the winder very fast.”
Another factor that he points to is the housekeeping and cleanliness of the board machine and, in fact, the entire mill. “We have taken a fine paper approach to making board. Board mills have typically been pretty dirty. We don’t want this. We want an extremely clean environment, much like a well-run fine paper mill. This certainly pays off for us in terms of production efficiency and high quality." Indeed, “perfect” is the word Resvanis uses to describe the quality of the containerboard coming off PM 2 and the winder.
He also wants to give his colleagues credit for the success. “All my team mates at Propapier have worked hard with a very positive attitude and this has made the project so successful. We are also very fortunate to have experts in corrugated board geometry at our sister company, Proteam. The team spirit within the company, as well as the cooperation with Valmet, has been excellent.”