Valmet Press Roll Cover PP: Low rolling resistance saves drive energy
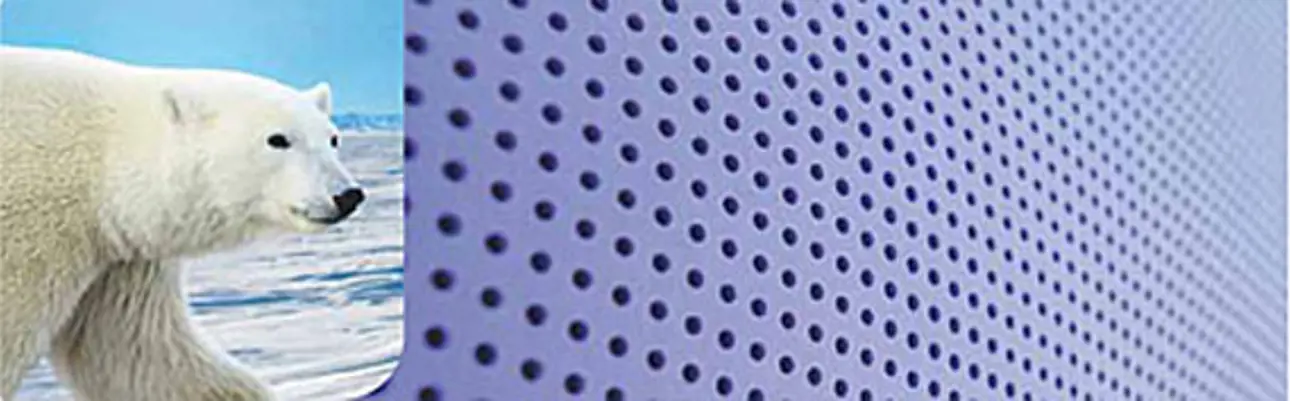
Part of the rolling resistance of press rolls is basically attributable to the energy lost in nip contact through the deformation and recovery of the roll cover. This roll cover deformation is, of course, very desirable in terms of proper nip length and nip pressure. Without roll cover deformation, we would destroy the paper web in many cases and have an inefficient dewatering process. When the hardness of the roll cover, i.e. its elastic modulus, needs to be fixed at a certain level, the rolling resistance of the roll cover is determined by other properties of the cover material.
Reduced energy consumption with Valmet Press Roll Cover PP
Saving energy has been one of the main themes for Valmet’s roll cover development program. Our intensive research and trial work has just recently produced some impressive publishable results. The new polyurethane roll cover, Valmet Press Roll Cover PP* offers new opportunities for energy savings. Thanks to a new type of polymer material, the rolling resistance of the roll cover is only a fraction of the resistance associated with traditional roll cover products. The cover is primarily targeted for highly loaded (linear load 300-350 kN/m) press rolls experiencing the greatest roll cover deformation under nip loads.
![]() |
40 kW difference -> energy 346 MWh/a -> potential savings up to EUR 30,000 year |
Simulated drive power comparison between traditional roll cover and Valmet Press Roll Cover PP, which offers remarkable drive energy savings, even at slower speeds.
A simulated drive power comparison between a traditional roll cover and Valmet Press Roll Cover PP is illustrated in the adjacent graph. The higher the speed (higher nip frequency) and the nip load (higher deformation), the greater the effect of the roll cover. Valmet Press Roll Cover PP offers remarkable drive energy savings, even at slower speeds. For example, a 40 kW cut in drive power conserves 340 MWh annually. Depending on local electricity rates, related savings may reach 30,000 euros per year. In addition to extensive theoretical work, the feasibility of corresponding drive power reductions has also been proven on real production machines.
Besides saving drive energy, Valmet Press Roll Cover PP works without internal water cooling. This means savings in related water pumping and cooling system maintenance. Water diffusion inside the cover material can also be avoided when internal water cooling is not used. Furthermore, it is one of the most abrasionresistant and durable polyurethane-based roll cover materials available in the papermaking industry today.
*earlier known as PressPolar
Article published in Results 2/2012.