Optimized water management saves natural resources and money
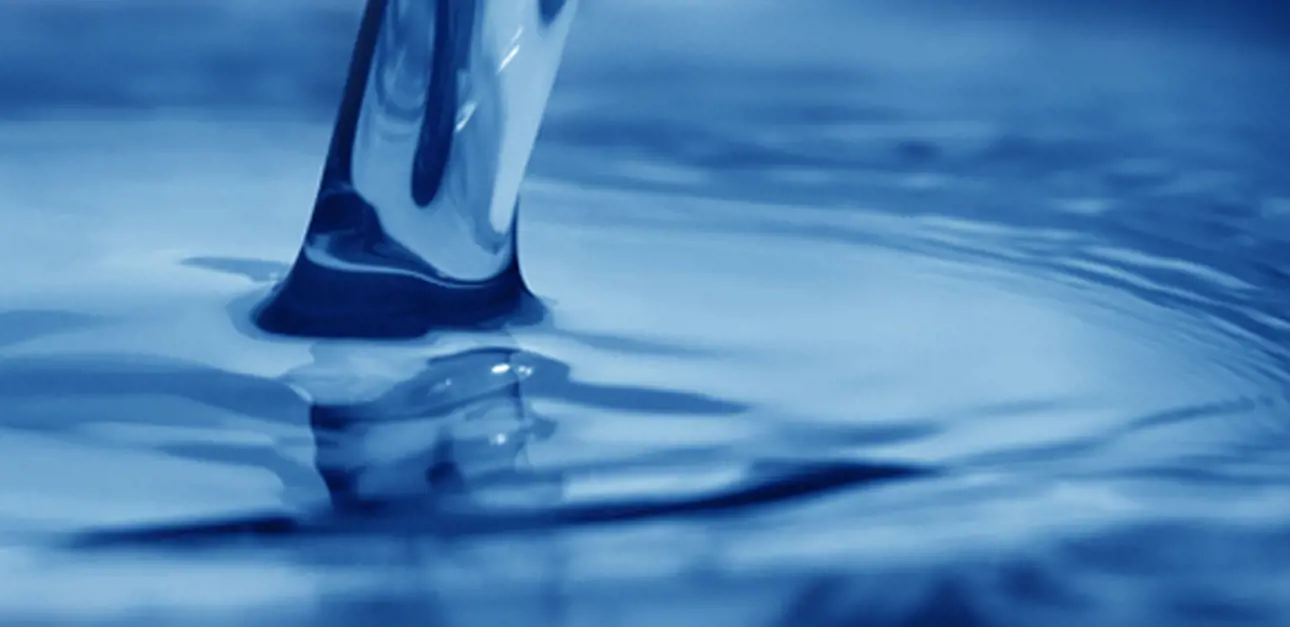
Paper mills have significantly reduced their use of fresh water over the past few decades. This is due to many reasons, including the limited availability of fresh water, increased cost of effluent and fresh water treatment, tighter environmental legislation, or even the desire to improve a mill’s public image in some cases.
This lower fresh water consumption has been facilitated by the reuse of process water, but also by a better understanding of process chemistry. Nearly every mill recognizes water emissions as a problem area. However, these environmental loads can be reduced by modifying and developing traditional papermaking processes.
Good water management improves mill efficiency
Today’s demand for better product quality and the increased use of recycled fiber both require higher-quality process water for good machine runnability. Our focus has to shift from individual process components to the overall quality of process water.
The goal is to master the whole papermaking line (machinery, equipment and processes) in detail. You have to understand the big picture all the way from fresh water treatment and internal water circulations up to the purification of effluent. Water management means planning, developing, disseminating and managing the optimal use of water, under applicable water policies and regulations, throughout an integrated paper and pulp mill complex.
The primary challenges in water management include environmental legislation, cost-effectiveness, and runnability. Optimized water management helps to support an efficient papermaking process.
Whether and how to close your water systems depends on the types of technology you are prepared to use. Along with the economics of the investment, you also need to consider potential disadvantages low fresh water consumption might entail.
Every papermaking line has its own minimum level of fresh water consumption that can be achieved with conventional process solutions. This level is reached when process engineering is based on the best available technology.
The closing of water systems has to be carried out without any negative effects on paper machine runnability, final product quality, or the environment. This means that the water used needs to be as close to fresh water in quality as possible.
Reducing fresh water consumption by 1,500 m3 per day?
The less water you use, the more you help to conserve the environment and save in water treatment costs. By using Valmet’s (Metso (Paper) until Dec. 31, 2013) ultrafiltration technology, you can purify your paper machine’s clear filtrate and use it instead of fresh water. Fresh water consumption will be reduced, as well as the amount of waste water. If fresh water needs to be heated, savings will also be achieved through lower heating costs and related airborne emissions.
Water management concepts for a variety of needs
The key to water and effluent cost savings is an efficient water management concept. Valmet has developed a full range of water management concepts for different paper grades and fresh water consumption levels. They are all based on extensive know-how accumulated through our reference projects, process evaluations and simulation studies at many paper and board mills around the world.
Process evaluation studies and the benchmarking of similar machine lines have enabled Valmet to evaluate a multitude of targets, technologies, successful solutions, and possible improvements. This prior experience is invaluable when carrying out a feasibility study or the preengineering stage for a project.