LondonWaste Ltd. chooses Valmet for energy-from-waste control system migration project
As one of London’s original generators of electricity from waste, LondonWaste Ltd. consistently updates, evaluates and maintains its technological efficiency. With a mission to efficiently and safely produce electricity, while remaining compliant to air emission standards, the company diverts waste from landfill and is among the region’s most vital public-service providers. To maintain technological updates for the energy-from-waste facility and for its control system, LondonWaste Ltd. assigned Valmet to deliver the conversion project.
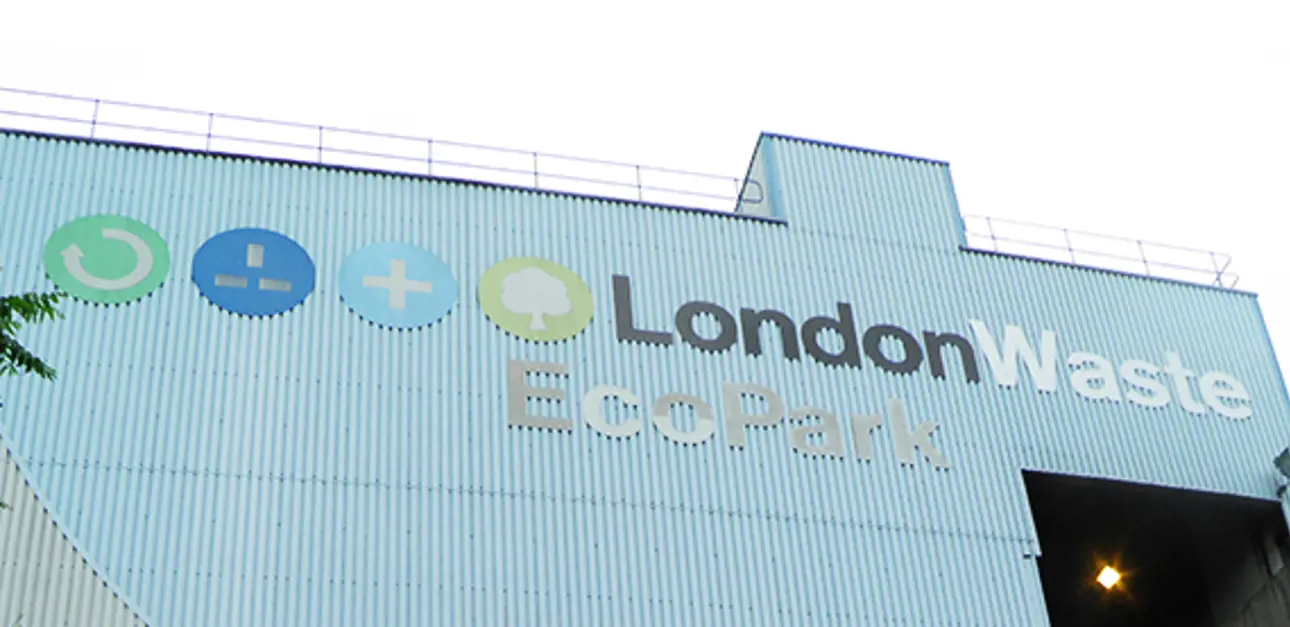
The energy-from-waste facility uses five boilers to burn household waste 24 hours a day, seven days a week. The steam produced is superheated to 415 °C before driving the turbine generators to produce electricity. The renewable energy generated powers all the other facilities on the company’s 17-hectare site and is enough to power 72,000 homes throughout the year.
As the plant burns household waste to produce power, its fuel source has many variables that have the potential to impact both the energy generation and emissions into the air. For this reason, air monitoring control systems are vital for the company to keep its operations compliant with the most recent emission regulations and to remain a leader in the field. A carefully managed migration to the latest control system allows LondonWaste Ltd. operators to control the plant’s performance in the most efficient way.
Valmet DNA – a better value solution
![]() |
|
Mr. Mark R. Beattie
|
Mark R. Beattie, Chief Information Officer from LondonWaste Ltd., is responsible for all the technology requirements in the business. He explains: “As a vital renewable energy generator, our technical upgrades should have minimal impact on the business. We wanted a guarantee of a long-term solution to our control system requirements. Valmet with its experience in migrating control systems in the energy-from-waste sector was reassuring.”
“Valmet offered us a total solution, both in terms of supporting the existing system and providing an integrated system migration. Valmet DNA was good for us. It solved all our problems in terms of the quality, service and reliability of the system,” Beattie states, explaining the company’s choice.
Migration proceeds step by step
For LondonWaste Ltd., the demanding conversion project will take three years to fully complete. Each boiler has specific scheduled maintenance periods so that only one boiler would be unavailable at any given time. The update-related work is being carried out during these scheduled boiler shutdowns.
Mark Beattie explains: “Despite the demanding migration project’s procedure and schedule, there have been no plant performance disruptions. During the project, all daily operations have continued as usual without any problems for the power plant or overall operational efficiency.”
Optimization system for emissions – a symbol of DCS potential
The company continues to manage and minimize its environmental impact. Using Valmet’s knowledge to further optimize emission control systems, both organizations will pool their experience to achieve compliance with air emission standards. Until recently, there was only one person in the plant in charge of providing this service.
“In discussions with Valmet during the bidding phase, it became clear that Valmet had more than just the control system to offer. The process optimization system, as well as additional advanced control applications, were also available. During the project, Valmet’s HCL/SO2 optimization solution was purchased and installed, demonstrating the system’s capability and Valmet’s commitment to the energy sector,” Beattie explains.
With optimization, the Valmet system actively looks for changes in the emissions rates and takes corrective actions to adjust the SO2 and HCL dosing accordingly. The availability of this optimization for the control system allows the operators to easily identify process trends and implement corrective actions to keep the plant within operational limits in the most cost-effective way.
Beattie says: “In addition to the possible plant operations optimization, the way the system stores historical data also allows operators to switch the display into a replay mode. This has been a real advantage because it shows the operators how to resolve problem situations in the most effective way, enhancing the efficiency level of the plant operations.”
Control room
In the spirit of mutual respect
During the project, genuine mutual respect prevailed. Mark Beattie emphasizes that collaboration between the plant personnel and Valmet was very open and constructive. Both sides brought in their professionals to discuss the various topics.
Valmet has responded well, according to Beattie. “Valmet’s engineers never said that something could not be accomplished. They always found a solution, even in complicated situations. The planned switchover was smooth. Communication with the engineers was proactive and everyone was informed in advance. Valmet’s team felt more like part of our staff rather than our contractor. When you see the engineers every day, you can ask questions and have them available to help you if something is needed. And what is also important in our environment, as a partner, Valmet understands the pressures and time constraints,” Beattie explains.
Operators involved
It is never too easy if you have a long-established process in place, and you want to implement new working methods. To make the move easier to the new system, Valmet’s engineers on site helped build trust. Beattie emphasizes that relationships were built continuously between the individuals – and that this was really important for them.
The operators gained confidence in the project by being actively involved. They helped design how the graphic displays looked and could be operated with the new system. This enabled their years of experience in operating the plant to be transferred into the end result, which then further enhanced the success of the project.
Neil Buckland, Valmet’s Sales Director, highlights that Valmet became an integrated part of the IT support desk HelpStar system to further assist and streamline support for the existing system and during the commissioning of the new one. By having a partner in the company’s support infrastructure, LondonWaste Ltd. strengthened its confidence in having any unexpected disturbance be solved quickly and effectively. Beattie states the idea to integrate Valmet into their own system has helped in quickly resolving common problems and repetitive cases, as well as reduced the number of such occurrences.
Today, LondonWaste Ltd. is owned by North London Waste Authority, which handles 525,000–550,000 tons of waste annually. It is important for the plant to produce a steady, uninterrupted supply of electricity.
“Everything in the process is transparent. We cannot control it blindly. I report monthly to the management about the proceedings and can assure them that the availability of Valmet’s automation system is maximal. Last year, it was an outstanding 99.9%. So, I do not have to worry about keeping up with the required electricity demand,” Beattie says.
According to Beattie, the boilers’ efficiency is better than ever. The waste throughput depends, for example, on the right temperature. The fuel is not necessarily constant but is monitored all the time by the operators. They watch the flames through cameras. In case they notice any deviations from the norms, they can take actions to improve the situation. There are many control options to carry out corrective measures. “Over the long run, we now have the capability to make our processes even more efficient,” states Beattie.
Reliability improved
![]() |
One of the major targets of the retrofit project was to improve the power plant’s reliability. LondonWaste Ltd. also recognized the benefit of having one company responsible for all parts of the system. With Valmet, LondonWaste Ltd. has gained a partner who helps customers get what they want.
“We targeted a long-term relationship and have indeed achieved this. The cooperation now continues in the form of service agreements with Valmet’s experts. We also appreciate the post-installation support we get,” assures Mark Beattie.
For more information:
Neil Buckland, neil.buckland (at) valmet.com