Irving boosts jumbo set throughput with Valmet iRoll
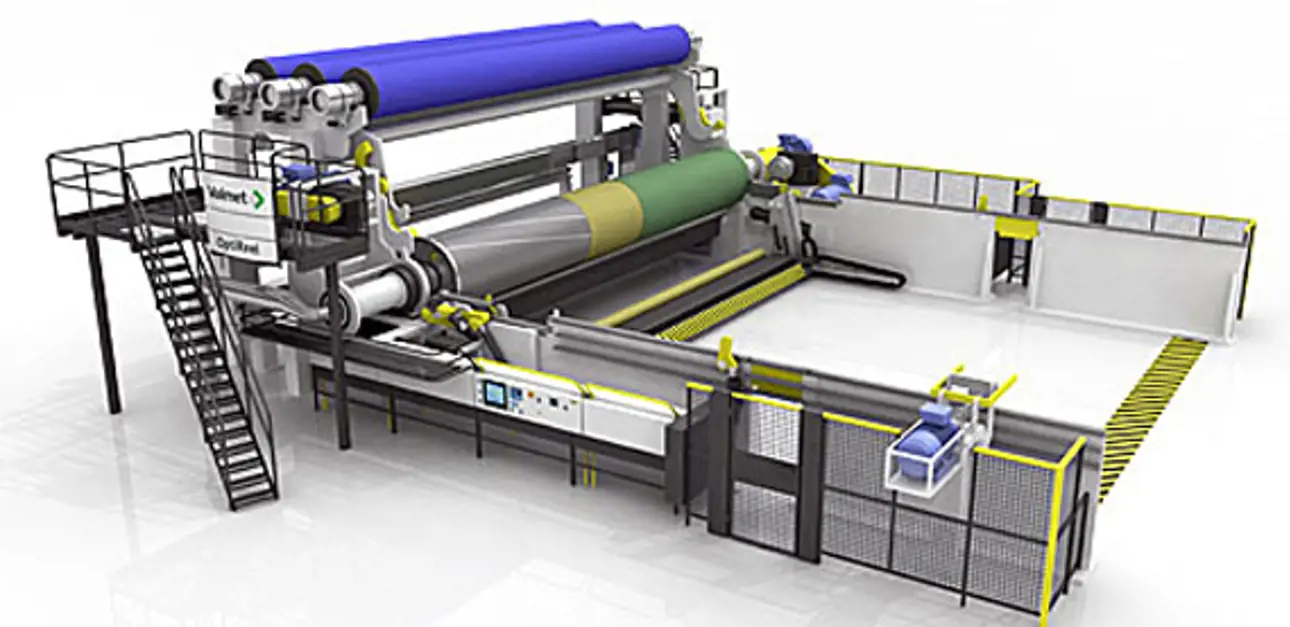
Irving Paper’s mill in Saint John, New Brunswick, Canada has managed to conclusively improve its customer roll throughput and the hardness uniformity on the winder of its PM 1 SCA+ production line with the help of a new polyurethane-covered Valmet reel drum with integrated iRoll nip load and reel hardness profile measurement and control. The mill now produces considerably larger jumbo reels with good profiles, even sheet tension and improved winder productivity.
Mark Chatterton, the Operations Manager at the mill, summarizes the successful project: “We are making more good-quality wound rolls; the efficiency of the winder has been increased. The iRoll has been a success story, a real plus for us.” PM 1 produces mainly SCA+ grades with basis weights from 42 to 67 g/m2.
Satisfied mill staff at Irving Paper: Justin Charron PM 1 (Technical Assistant, from left), Bill Davis (Operator), Greg Ryan (PM 1 Superintendent) and Mark Chatterton (Operations Manager).
Good roll structure is challenging
Many SCA producers would agree that it’s challenging to make a well-structured jumbo SCA reel with good hardness profiles once a certain reel size threshold is reached; the effects of air entrapment become significant after so many wraps in a parent reel. Dense SCA+ sheets, with their very low porosity, do not effectively allow the air trapped between the winding layers to escape evenly, which has a cumulative effect on sheet tension, causing wrinkling and winder breaks. Dr. Heikki Kettunen of Valmet explains the practical papermaking reasoning: “Profile errors affect the accumulation of air under the topmost layer of paper. In many cases, you can run with a stable air bubble before the nip. However, if the top layers of paper are not stabilized, an air bubble impacting the tight part of the roll easily creates foldovers and wrinkles.”
With those wrinkling effects, winder production often falls behind and the familiar sight of full reel spools in the aisles signals low productivity. The solution is often unwanted but necessary: limit the number of sets in the jumbo – which then increases the losses from bottom and surface broke.
That was the situation at the Irving mill. Chatterton reports that they were limited to making two sets of 50-inch diameter rolls, particularly on the heavier basis weights. Anything bigger and the rolls being wound would suffer from hard and soft spots and wrinkles that would lead to winder breaks. Winder production would fall behind. Also, with frequent reel turnups, the slab losses were higher than they should be.
Integrated two-component solution
The mill looked for a solution from Valmet, who had rebuilt PM 1 in 2006, to produce SCA+ with North America’s first OptiLoad TwinLine multi-nip online calenders. After visiting an SCA reference site in Europe, Irving concluded that an integrated, two-component solution was the right one for them. First, they decided on a compliant nip polymer-covered reel drum with chevron grooving. The extended nip would provide more nip dwell time and therefore better air removal, which would be assisted by the grooving. The extended nip would also provide a tighter wind. Material for the cover was polyurethane Valmet Reel Drum Cover RS, as it has excellent wear resistance and strength that ensure a long life time for the cover.
The second part of the solution was the iRoll pressure-sensitive sensor strip, embedded below the roll cover in a spiral pattern. Unlike traditional paper quality scanners, following its initial setup, iRoll has not needed frequent maintenance. The nip load and related reel hardness profiles are measured continuously and transmitted wirelessly to a central processing unit, which updates the profiles every half a second. These profiles are used to control the profiling of both OptiLoad calendar stacks to meet the targeted hardness profile. The calender profiling is done by using Sym-CD zone-controlled rolls in the top and bottom position of each calendar stack.
Immediate results: One extra set right after start-up
The new reel drum was installed over three days in early June, 2013. The results after start-up were immediate, according to Chatterton: “We were running three sets instead of two immediately after start-up.” He also mentions the good support Valmet provided after start-up as the company’s engineers continued to help the mill optimize the new reeling recipes. He reports that the operators are comfortable with the operation of the measurements and controls, saying it is “easy to catch on.” As is typical of this paper grade, the operator-entered target hardness profiles are not completely flat; they have a gently sloping bowed shape which is lower at the edges. The softer edges allow air to escape from the parent roll and avoid winder tears associated with edges that are too hard. The calender nip loading profile may affect gloss profiles, but they are reported to be well within quality tolerances. The iRoll also has a valuable diagnostic purpose for both reel and calender. The calender nip loading profiles required for even reel hardness may indicate roll wear problems in the calenders or in upstream rolls. Chatterton says, “Measuring calender zone profile trends offers us early indications of uneven roll wear problems.”
The new responsive measurement system has allowed the mill to develop a new, effective control strategy to resume production with good parent roll hardness profiles immediately following a long break. The control “flatlines” with all zones at an equal nip pressure until the iRoll profile is seen soon after the sheet is on the reel. The profile measurement is valid just a few minutes after the sheet resumes. Whether the location of hard and soft spots has changed is immediately visible, and the control works on them right away.
From two to four sets
The mill was able to produce three good sets – up from two – right after start-up, but the results have improved since then. Chatterton sums it up: “We eliminated wrinkles from air entrapment, giving us reduced breaks and winder cull. We now have a more even tension profile and finished roll profiles. We have run up to five sets, but we cannot easily handle the larger reels. We now run four sets of 50-inch rolls on every grade.”
Time-averaged figures comparing the year before start-up to the year to date since start-up quantify the results so far:
- The number of turnups are down 23%
- Slab losses, including the winder, are down 20%
- The number of sets per reel are up 16%
- Reel diameter is up 16%
Missed turnups are also down 70%, although iRoll is not the only reason. The iRoll feedback has aided in tuning and optimizing the OptiReel Plus operation. Thanks to the larger jumbo roll sets and decreased web breaks on the winder, the mill can also now perform maintenance tasks on the winder without needing to wait for a shutdown. All told, this adds up to a handsome ROI for Irving Paper.