Heat recovery stops energy from escaping into air
Instead of releasing heat into the air with flue gases, it is possible to harness it with Valmet’s flue gas condensing technology and use it in a number of processes.
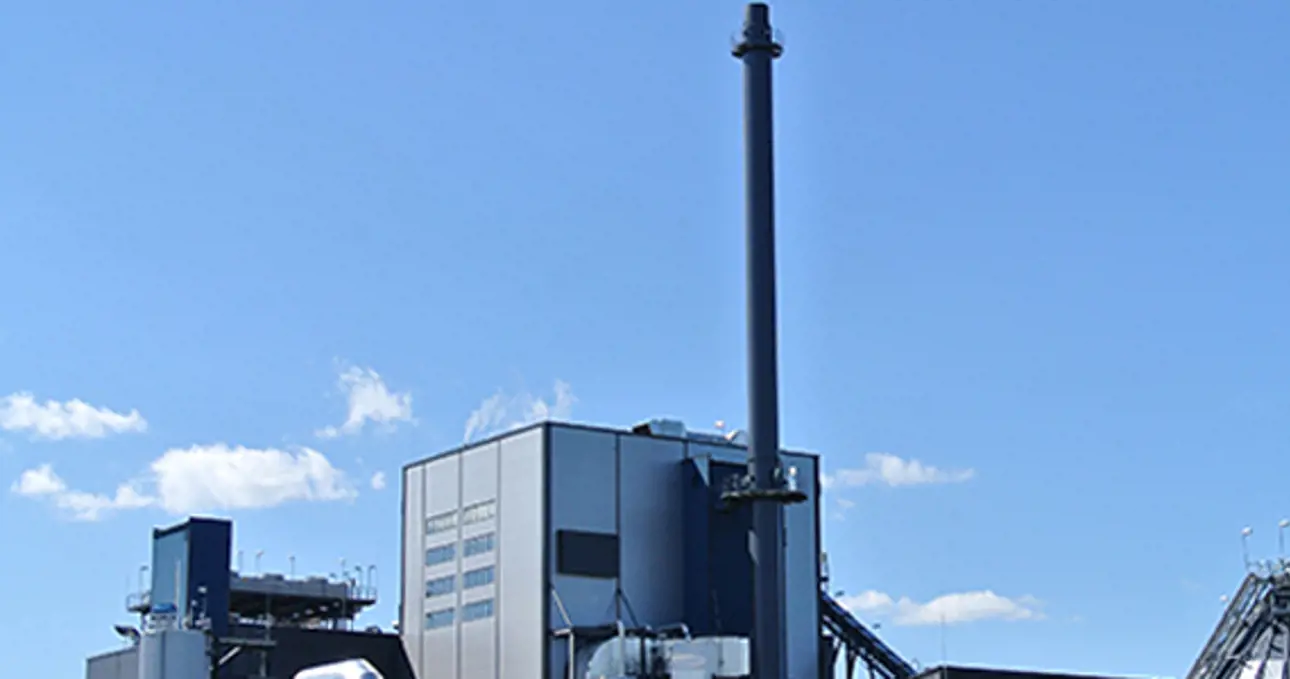
The possible applications for flue gas condensing are numerous: district heat production, paper mills, deinking plants, sawmills, plywood production, and any application where warm water is needed. The results observed at power plants and paper mills have been excellent.
“In this era of cost efficiency, no plant or mill can afford to waste energy. Further pressure comes from tightening emissions regulations,” points out Risto Hämäläinen, Director of Environmental Systems at Valmet. “One solution to boost both energy efficiency and sustainability is to combine wet flue gas cleaning and flue gas condensing into a single process.”
Flue gas condensing technology can significantly increase a power plant’s overall performance. For example, it has been proved that combined heat and power plants can achieve increases of up to 25% in their heat production when they take advantage of flue gas heat recovery. The Nordic countries – especially Sweden and Finland – have been pioneers in adapting this technology to boost district heat production. Today, almost all new plants in these countries are equipped with flue gas condensing systems.
Paper mills benefit, too
Technically, heat recovery is applicable for any flue gas that contains enough water vapor. Condensing is typically feasible when the moisture content of the flue gas is above 15%.
In addition to district heating applications, recovered heat is useful for paper, saw and plywood mills, among others. “All these share a need for warm water in their processes. Heat generated without paying for extra fuel is welcome in these times of growing cost efficiency pressure,” Hämäläinen continues.
More energy from fuel
Practically any combustion process that runs on moist fuel or produces flue gas that contains enough water vapor is suitable for flue gas condensing.
According to Teemu Toivo, Sales and Technology Manager for Environmental Systems at Valmet, this technology is often found at plants or mills that generate energy by combusting wet fuels, such as peat and biomass, but it is also suitable for drier fuels, such as municipal solid waste or even natural gas.
The key to higher energy efficiency lies in utilizing the moist fuel as efficiently as possible. There is a lot of energy in flue gas from moist fuel due to the water content (30–60%) of the fuel and the steam in the boiler. This energy escapes into the environment when the water is not condensed back into a liquid.
“With advanced flue gas condensing technology, energy can be recovered and used, for example, to increase district heat capacity, save fuel or increase the overall balance while heating up the turbine condensate,” adds Toivo.
Towards zero emissions
Efficient flue gas condensing has environmental benefits, too. Integrated with wet flue gas cleaning, it not only improves energy efficiency, but also minimizes emissions caused by the combustion process. The emissions regulations are continuously tightening.
“With modern, high-tech air pollution control solutions, energy producers and paper mills can aim for zero emissions,” Hämäläinen stresses. “The results gained with new flue gas condensing technology show that even the tiniest remaining particles and acid gases produced in the combustion processes can be removed. A flue gas condensing plant typically reduces, for example, acid gases, ammonia and dust by up to 95%.”
Tube condenser or condensing scrubber?
Valmet is one of the pioneers of efficient flue gas heat recovery, with experience extending back to the 1970s. “Today, we employ over 100 professionals focusing purely on environmental systems and solutions to promote sustainability in energy generation,” Toivo remarks. “Our strengths lie also in our broad know-how and ability to provide turnkey deliveries.”
The company offers two technologies for flue gas heat recovery – a tube condenser and a condensing scrubber. Deciding which of these alternatives best meets the needs of the customer always depends on the primary goal. If it is to clean flue gases, the solution is probably a condensing scrubber. If the main aim is to gain more heat through heat recovery, a tube condenser typically gives better results.
Toivo continues: “To boost heat recovery further, it is possible to add either a combustion air humidifier or a heat pump to either of the solutions. Valmet also offers condensate treatment solutions which make it possible to use the condensate for boiler feedwater or district heat make-up, or simply treat the condensate to meet the environmental permit limits”.
The tailor-made solutions are suitable for boilers in a wide range of sizes, with various types of boiler technology and running on all kinds of fuels.