GE Frame 6 automation retrofit at Lahti Energy: Better availability and at least 100 times more information
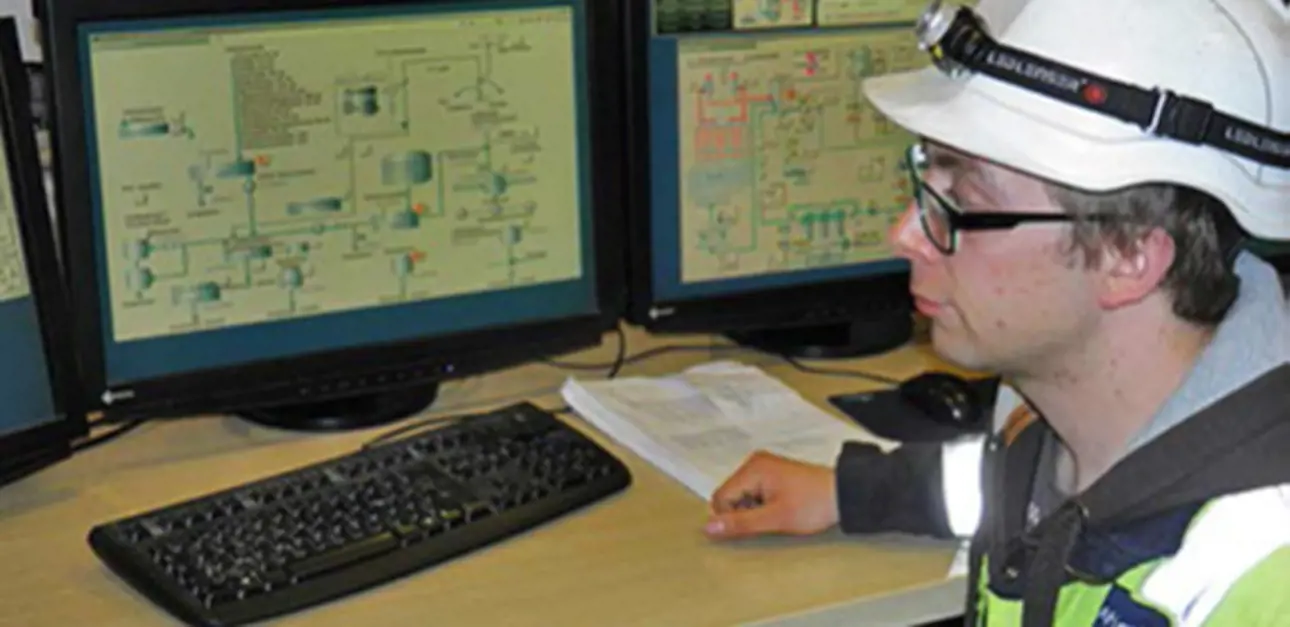
Higher reliability and a deeper view into the process – that’s definitely what Lahti Energy got when Valmet delivered a demanding automation retrofit to the company’s GE Frame 6 gas turbine. Unlike before, a massive amount of information is now available to all involved in the process, enabling continuous follow-up and proactive measures.
In this article you will learn:
- How the new gas turbine controller and its redundancy concept achieve the highest possible system reliability and availability to ensure reliable and safe operation.
- How troubleshooting is easier; the operators can follow the process more accurately and see the trends.
- How being able to carry out all functions and diagnostics at various plants through one system improves plant availability.
![]() |
![]() |
Will it or won’t it start up this time? The operators at Lahti Energy in Lahti, Finland, used to keep their fingers crossed that it would when they pushed the button to start up the GE Frame 6 turbine. | Jarmo Naukkarinen and Mikko Anttila in front of the GE Frame 6 gas turbine |
“The turbine acts as a backup plant for the main plants, Kymijärvi I and II, at the same site. If one of the two goes down, and the gas turbine is needed but will not start up, we will lose capacity,” says Mikko Anttila, Process Engineer at Lahti Energy. “This is critical if the price of electricity is high at that time and we miss, let’s say, two days of production. And it might be that – finally – when we are able to start up the gas turbine, the price of electricity has sunk.”
Availability is a key issue also for the company’s district heat customers. If the above problem occurred during the coldest winter spells, local inhabitants would soon start to shiver. “Nearly all of Lahti would feel the chill since most of the housing is connected to the district heat network. The backup plant must start up when needed,” adds Jarmo Naukkarinen, Project Engineer at Lahti Energy.
Built in 1987, the GE Frame 6 gas turbine has an electrical capacity of 49.5 MW and a thermal capacity of 60 MW. It is fueled with natural gas and runs depending on the price of gas and electricity.
An automation retrofit was necessary since the original gas turbine controller had reached the end of its life cycle. It featured outdated electricity, and components were no longer available for it. “And what’s more, our maintenance staff familiar with the system was retiring. This presented another risk,” Naukkarinen explains.
Highest possible system reliability
From several alternatives, Lahti Energy chose Valmet* to supply the gas turbine automation retrofit, mainly based on earlier good experience with the supplier and its solutions. Its Kymijärvi I and II plants are controlled with Valmet DNA technology into which the new turbine controller was integrated and started up in the fall of 2012. “The project went according to plan, although the schedule was tight,” says Naukkarinen.
In addition to the Valmet DNA Gas Turbine Controller, the delivery included Valmet DNA Machine Monitoring, Valmet DNA Information Management as well as overspeed and machine protection featuring the HIMA F60 SIL3 system. A number of Endress+Hauser temperature transmitters were delivered, too.
The new gas turbine controller and its redundancy concept are designed to achieve the highest possible system reliability and availability to ensure reliable and safe operation. The control applications are implemented as part of Valmet DNA DCS standard redundant ACN high-speed Process Controllers. The turbine controller utilizes the standard Valmet DNA DCS M120 I/Os, specifically designed for power industry applications to meet their requirements.
Prior to delivery, the gas turbine controller control design was tested at Valmet’s certified FAT facility with a simulator for all standard operation and emergency operating conditions to ensure correct governor and ESD system functionality. “We tested the process and protection with the simulator to see what triggers what. It was beneficial to see possible problems before the equipment was actually running,” Anttila comments.
Able to act before it’s too late
Integration of the turbine controller into the plant-wide automation system and thus having only one system has provided many benefits at Lahti Energy, which also operates a network of smaller plants in and around Lahti. “An operator who knows how to operate one plant, and knows the process, is now able to run any of our plants. There are fewer risks involved,” Naukkarinen points out.
“We can follow the process much more accurately and see the trends. The process is much more open for us. The old controller provided only a tiny fraction of the information that we now have access to. The amount of information is now a hundredfold,” Anttila stresses. “We no longer have to keep our fingers crossed for everything to go well since we know all the time what is happening in the process. We can react sooner – and before anything goes wrong that could break the turbine.”Whereas it was earlier challenging and time- consuming to find out why the turbine stopped and to re-start it, troubleshooting is
now easy – even when it comes to possible upcoming disturbances. All information from the turbine can be viewed on graphic displays in the Kymijärvi main control room with efficient user tools.The operators are able to carry out all functions and diagnostics through one system, which significantly improves plant availability. “Now that we have only one automation system, also maintenance is simpler and training is not needed for many systems. Our own staff, for example, is able to carry out minor software changes,” he goes on.
Much use of the process history databank
The operators appreciate the clear and plain language displays. User-friendliness is built in to all parts of the system and its user tools. Anttila is especially fond of the history databank, Valmet DNA Historian.
“I actually find it to be one of the best tools in the system. For example, the turbine startups are usually very early in the morning when I have not yet come to work. From the process history databank, I can later check how the startup went,” he says. “If something did not go well, we can analyze the event second by second and possibly also discuss it with Valmet people through their remote connection. In all, the turbine controller works well!”
Continuous flexible cooperation
Closer cooperation between Lahti Energy and Valmet started in 2008 – and proved fruitful again in this project. Naukkarinen appreciates Valmet’s flexibility, for example, in rescheduling the test trial period. “It was supposed to be in summer 2012, but the gas turbine was not running due to electricity market conditions,” he notes. “Another thing is that working with professionals is always nice. Our special thanks go to Pekka T. Niemi, Senior Specialist at Valmet who handles any demanding task.”
Lahti Energy has a 24/7 service agreement with Valmet for all the automation systems it has delivered. Valmet’s professionals have access to the systems via remote connection. Cooperation currently goes on also in automating smaller heat plants and equipping them with remote control from the Kymijärvi main control room.
For more information, please contact:
Johan Musch
johan musch(at)valmet.com
*) Company and product name Metso until March 31, 2015.