Effect of composite roll cover hardness on calendering
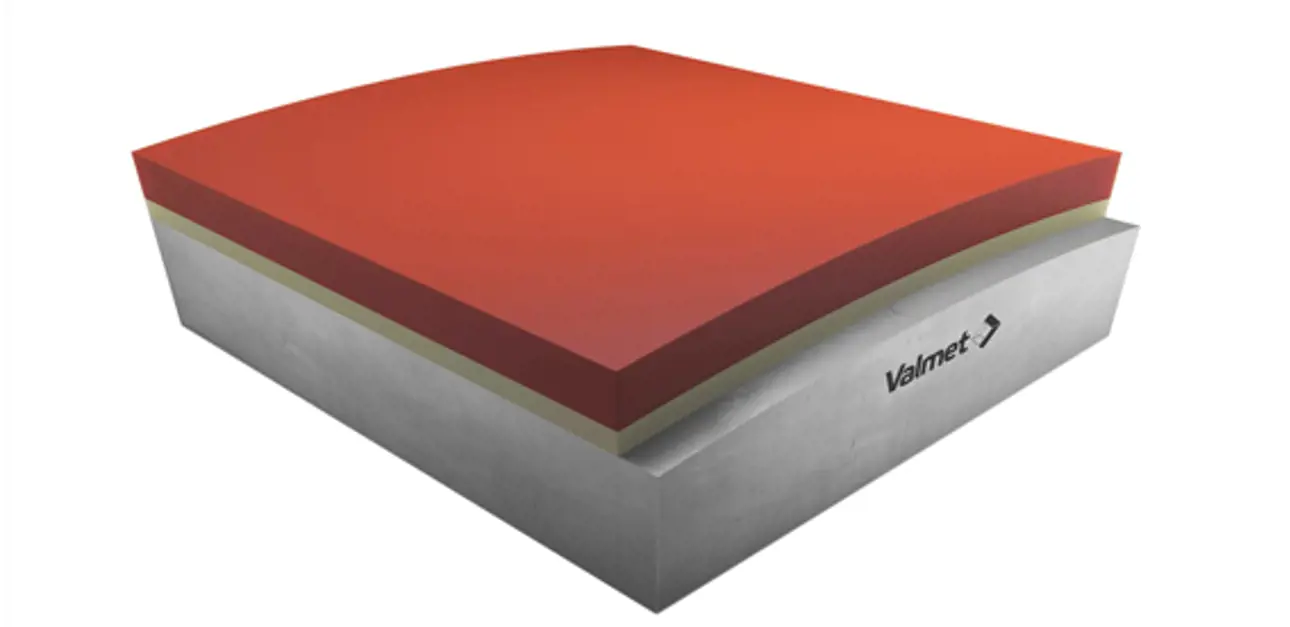
Every now and then the question arises of whether paper producers can improve end product quality by using softer composite covers in the calender section when dealing with bulky grade calendering, such as wood-free or liquid packaging board grades.
Basically all soft calender and multinipcalender covers are made of an epoxy
composite. The hardness of these composite covers ranges from 88 ShD
to 93 ShD, mainly depending on the hard filler particle content of the cover.
In calendering, bulkiness is preserved and the paper or board becomes less dense when the maximum pressure is as low as possible. In order to make the same calendering work for the web, like smoothing and creating gloss, the
high pressure needs to be compensated for by a longer dwell time (meaning a wider nip as the speed is constant) and higher temperatures.
Consequences of composite hardness
Using a softer roll cover allows the maximum pressure to be reduced and the dwell time prolonged as the nip width increases. How much can we actually infuence these factors when using composite covers that are as soft as possible? The figure 1 shows the potential difference in nip pressure and nip width while using an 89 ShD composite cover compared to a 93 ShD hard cover. These calculations were prepared using a 7 m wide soft calender with woodfree paper in the nip.
Figure 1. Composite hardness effect on nip pressure and nip width.
With a low calendering load of 40 kN/m, not much difference can be seen.
With a load of 100 kN/m, the difference in maximum pressure is 9%, but the nip width difference is only 2.5%. In practice, this difference is lost in paper production variance.
The importance of nip load
To actually gain a significant difference in calendering, much more softness is
needed than any epoxy composite cover can offer. In some earlier, very limited applications, a special rubber or polyurethane material was used for soft calendering. As seen in Figure 2, decreasing the nip load while using a composite cover will reduce nip pressure in a linear fashion, while also reducing the nip width. At the same time, the amount of calendering performed will decrease.
Moreover, reducing the nip load involves technical difficulties: Nip vibrations have a tendency to significantly increase when nip loading falls below a critical level. This happens due to bearing backlash and bearing loading that might become too light at low loading levels. In many calenders, this limits the minimum useable loading level.
Better calendering with Valmet Calender Roll Cover CPU
Figure 2 clearly shows that the same nip pressure level can be achieved at double nip loading with our polyurethane Valmet Calender Roll Cover CPU as with a composite cover. While the nip width is increased, more calendering work is done. This means that the same calendering effect can be achieved for the web, but with less web intensification. This in its turn increases bulk, which paper and boardmakers can turn into savings on fiber costs.
Valmet's new polyurethane materials offer a softer composite cover for demanding calendering conditions. Valmet Calender Roll Cover CPU is a soft calender roll cover that provides a long nip, good impact resistance and maximized bulk. It can lead to great improvements in line profitability.