Down with NOx emissions
Helen Ltd has reduced the already low NOx emissions from its Salmisaari B power plant in Helsinki, Finland, with Valmet’s efficient Selective Catalytic Reduction (SCR) system that employs urea instead of ammonia.
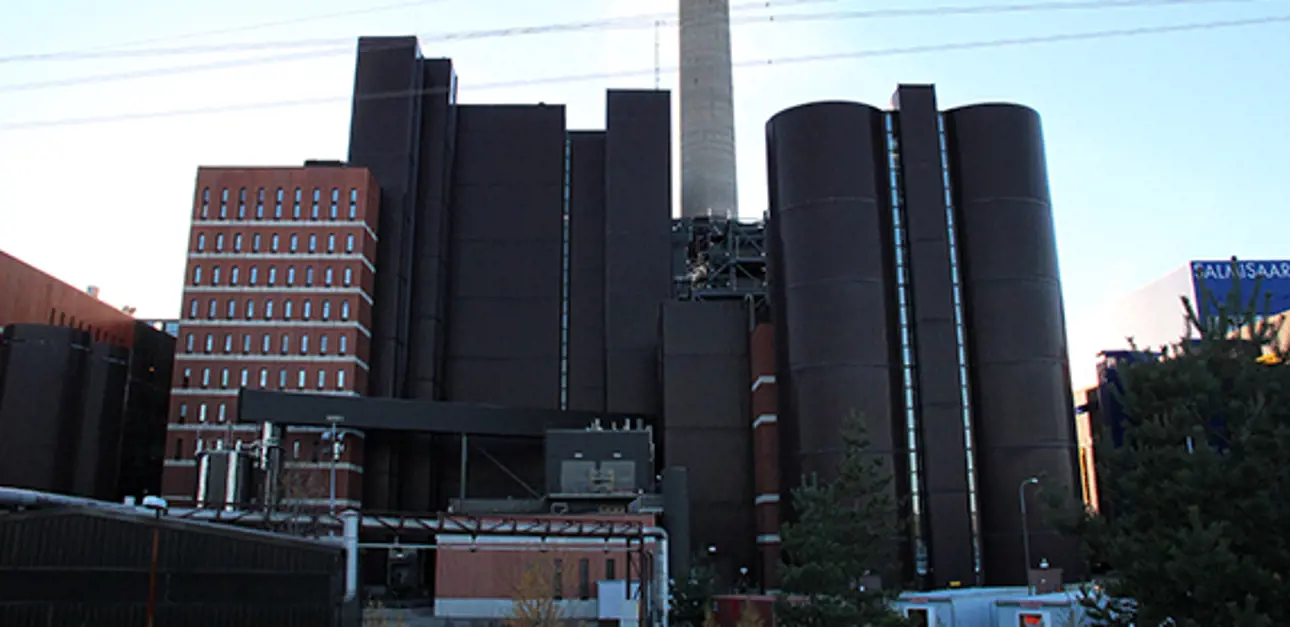
The new tighter nitrogen oxide (NOx) emission limits set by the Industrial Emissions Directive presented a challenge for Helen, a company fully owned by the City of Helsinki. To reduce NOx emissions even further, the company chose Valmet’s SCR system for its Salmisaari power plant.
“Through a public tender, we asked for earlier references from the possible suppliers and their response to various criteria for the equipment. Based on fulfilling our technical and other key criteria as well as the operating costs and price, Valmet ranked highest among the bidders,” says Reima Rynö, Project Manager at Helen.
Rynö appreciates the good cooperation with Valmet that actually started already during Helen’s pre-study phase and well before the call for tenders. “We asked several equipment suppliers about the NOx reduction methods they may be able to provide. Valmet was very active in answering our questions, which gave us a very positive image of the company.”
Ammonia produced by hydrolysis onsite
Valmet’s SCR solution is an effective NOx reduction method in which nitrogen oxides are reduced to harmless components, water and molecular nitrogen. This takes place in a SCR reactor by using a reduction agent and catalyst. The purpose of the catalyst is to speed up the reaction. The benefits of this method include maximized reduction efficiency – over 90% reduction of NOx – with minimum operating costs.
Typically, catalytic methods for removing nitrogen oxides employ ammonia as a reduction agent, but at Salmisaari B, the ammonia has been replaced by urea for safety reasons. “Our power plant is located in downtown Helsinki. According to the authorities’ restrictions, we were not allowed to store large amounts of ammonia water onsite or have ammonia transported within the city area,” Rynö explains.
With Valmet’s solution, urea water is converted into ammonia gas using hydrolysis equipment.
Photo: Reima Rynö, Project Manager at Helen, appreciates the good cooperation with Valmet that started already during Helen’s pre-study phase. Both photos on this page by Helen Ltd.
A successful retrofit
At Salmisaari B, the SCR system was installed in a pulverized coal fired boiler. In addition to the equipment, Valmet’s turnkey delivery included engineering, project management, procurement, steel structures, installation and startup. Helen took care of the foundations and buildings required for the equipment. The new system was integrated into the plant-wide Valmet DNA automation system that Valmet recently upgraded.
Retrofitting a fully built environment with urea storage, hydrolysis equipment and a catalytic reactor was challenging.
“It is essential for the process to find good places for the equipment so that the units are not too far from each other. For example, the reactor was installed on top of our electrostatic precipitator in a very tight location,” Rynö explains. “Valmet’s installation work, technical expertise and project management were top class. It was a pleasure to work with the project team.”
Well below emission limits
The SCR system was started up in November 2015. “Since very early on, its performance has been excellent and exceeded our requirements. Some minor fine tuning was necessary, like with every new system,” remarks Rauno Kontro, Operations Manager at Helen, Salmisaari Power Plants. “This has certainly been one of the most painless projects we have ever carried out.”
Before the new system installation, Salmisaari B’s annual NOx emission average was slightly under 500 mg/Nm3 with 6% oxygen. Now the emissions have been about 50 mg/Nm3.
Four SCR systems on their way to Poland
During the past 20 years, Valmet has supplied SCR systems to numerous new and retrofit boilers. One of the latest orders includes SCR technology for four OP-110 coal-fired boilers at CIECH Soda Polska S.A’s CHP plant in Inowroclaw, Poland. The first of the installations will be operational in June 2016. The delivery also includes a wet limestone flue gas desulphurization solution.
Text: Marjaana Lehtinen