Customized winder service ensures efficient operations at Stora Enso Huatai PM 6
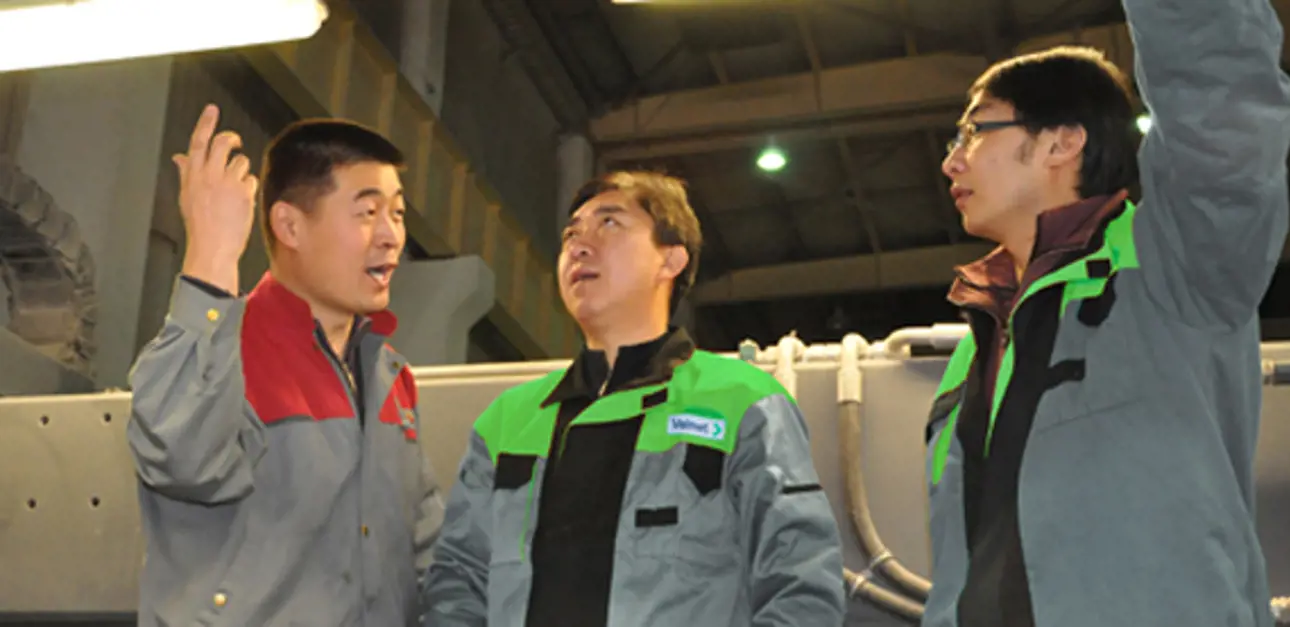
The quality of customer rolls is greatly influenced by the winder. Unstable performance can result in major losses and headaches, whereas reliable performance can reduce costs and offers peace of mind. One mill that has benefited considerably from Valmet’s (until Dec. 31, 2013 Metso Paper) regular on-time preventive maintenance solutions and professional mill site services is Stora Enso Huatai.
Established in April 2006 and located in Dongying, Shandong Province, China, Stora Enso Huatai (Shandong) Paper Co. Ltd. is a joint venture of Stora Enso Group and Shandong Huatai Paper Co., Ltd. Previously located in Germany and then migrated to China, PM 6 produces recycled fiber-based super calendered paper (SC). The grade is widely used, for example, in advertising materials, mass circulation magazines, catalogs, newspaper inserts, mail orders, and supplements.
The production line features a new belt-supported WinBelt winder supplied by Valmet. The winder became operational at the end of 2007. The winder is able to turn nip load sensitive paper into large, high-quality shipping rolls by controlling the nip load and making tight paper rolls through the application of high winding force from the driven belts.
Regular vis
Since the start-up of the winder, local Valmet service people have been providing the mill with customized winder process know-how, improvements, and maintenance services.
“My cooperation with Valmet goes back ten years to the time when I worked at PM 9 and PM 11 in Shandong Huatai Paper,” says Bin Li, Winder Supervisor at Stora Enso Huatai. “The technology that Valmet’s mill site service uses is advanced and their service quality is very good. These are the reasons why we trust Valmet and why we have chosen the company as our preferred supplier for the winder. In fact, we have improved our winder performance a lot by working with Valmet.”
Valmet’s mill site service team in China was established in 2005 to provide fast and effective service for pulp and paper mills. The work of the team is summed up nicely by the Chinese saying: “When the medicine comes, the symptoms are alleviated”.
Increased speed and capacity
In April 2011, when Stora Enso Huatai was adding a new paper grade to its production range, it was necessary to upgrade and optimize the winder. Not only was its speed too low, but there was also major vibration in the winding area.
The mill contacted Valmet’s mill site service and an expert was immediately assigned to the job. To begin with, the winder’s mechanical components were checked for wearing. Then, to keep the vibration at a good level and all rolls in tolerance, mechanical alignments were checked and corrected. Also, new winding parameters were created to produce high-quality shipping rolls out of the new paper grade.
Valmet also arranged on-site training for the mill operators. The training better acquainted them with the winder so they could locate possible problems, analyze the paper by using the proper tools, and use the Valmet winder automation system more efficiently.
As the result of all these winder performance improvements, the winder speed was increased from 1,600 m/min to 2,000 m/min, which meant an increase in winder capacity.
Dishing problem eliminated
In September 2012, a dishing problem with the winder caused uneven roll edges, resulting in poor roll quality. Despite their best efforts, the Stora Enso Huatai staff could not find the reason for the problem. Valmet was contacted to provide deeper insight into the winding process.
Customer roll end after service.
After a careful winder inspection and the elimination of some possible causes of the problem, the real reason was discovered. The winder rear drum surface roughness had reduced, making the winding force uneven. Valmet fixed the problem by re-coating and re-aligning the rear drum. In addition, the winding recipe was optimized, and the tension transmitter was replaced.
With these measures, it was possible to improve roll quality and eliminate the mystery dishing problem.