Customer needs drive innovation
Customer needs and global megatrends have been the driving force of Valmet’s product development throughout the company’s 220 years of industrial history. Resource efficiency and open innovation connect Valmet’s product development and customers. New leaps in development are aimed at the Industrial Internet and digitalization.
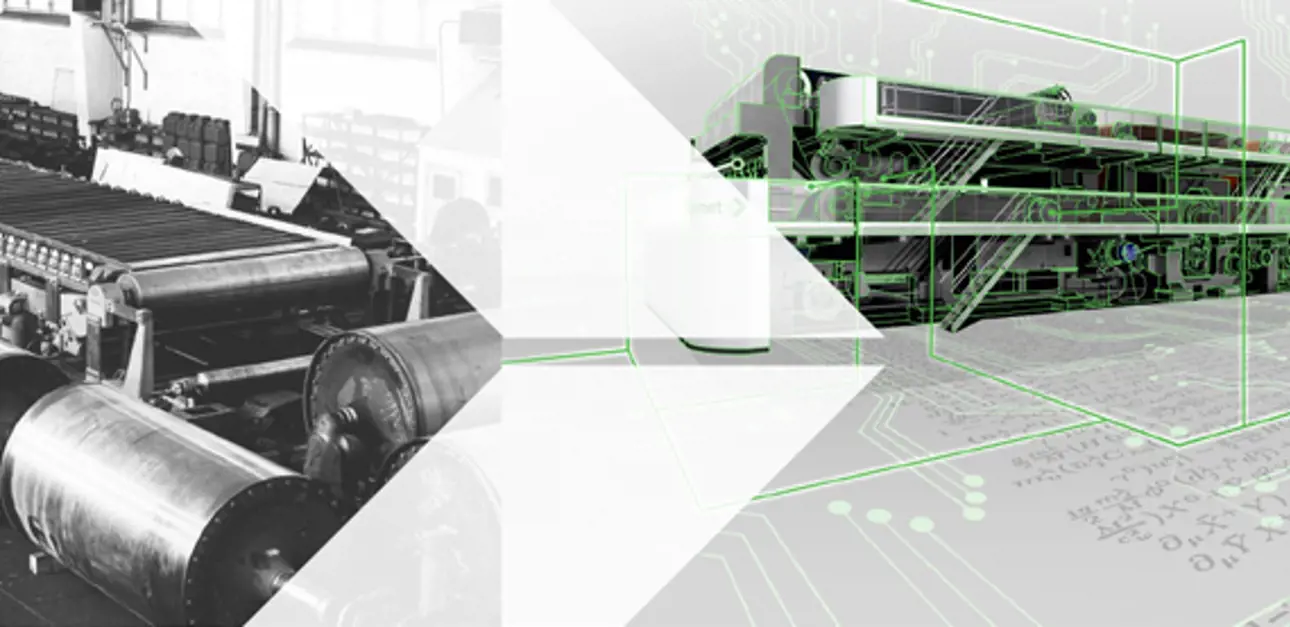
Valmet’s story began in 1797, when Tampereen Verkatehdas, a cloth factory that later became known as Tamfelt, was established. Tamfelt became a part of Valmet in 2009 through a corporate acquisition. So, Valmet’s 220 years of industrial history began with the manufacturing of textiles, and this tradition still continues in Tampere, where Valmet Fabrics develops and manufactures machine clothing.
The Valmet of today was created through numerous corporate acquisitions, mergers and demergers. In its history, Valmet has, in fact, developed and manufactured nearly everything from aircraft to rolling stock and from chainsaws to cannons. Today, Valmet develops and manufactures technologies, automation systems and services for the pulp, paper, board and tissue and energy industries.
Entering the market with a differential drive paper machine
The first steps to manufacturing paper machines at Valmet were taken in 1946, when several metal workshops owned by the Finnish state were merged to form Valtion Metallitehtaat (“State Metalworks”).
Already in the 1950s, Valmet entered the paper machine market with its own differential drive machine, in which each motor group worked steplessly, according to its own adjustments. This way, they could be adjusted accurately to the right speed. In the 1960s, Valmet expanded its own machine base, developed its research activities and networks, and increased its delivery capacity.
Valmet’s pilot plants have offered a unique opportunity for product development. Since 1972, Valmet has had its own pilot paper machine. “With the help of the pilot paper machine, new ideas, even radical ones, could be tested at a smaller but truthful scale,” says Jouko Yli-Kauppila, Valmet’s emeritus Technology Director.
Economies of scale as a driving force of 80’s and 90’s
In the 1980s and 1990s, economies of scale were dominant in the forest industry: Ever wider and more efficient machines were constructed, and run with an increasing speed and efficiency. “New top-selling products were created when the hydraulic headbox and gap former, among others, were developed in the 1980s. As a result, we were able to raise the machine speed, leading to increased production and better paper quality,” Yli-Kauppila says.
New solutions were also developed for example for paper machine rolls, especially to replace the stone roll in the press and to improve the durability of suction rolls.
The OptiConcept technology, launched in 1997, proved to be a super product. The paper machine was 25% faster than older machines. Thanks to industrial design the machine was also easier to use and maintain.
Involving customers
After the turn of the millennium, challenges to product development came from China, where narrower and slower machines were needed. At the same time, online trade started a downward trend in the consumption of writing and printing paper in the West. As a response to these changes, Valmet developed a modular machine concept, OptiConcept M, which is suitable for board, as well as writing and printing paper, with only small modifications.
A clear change has also taken place in customer wishes in this millennium: while in the 1980s, customers were interested in technology in itself, today they ask what can be accomplished with it.
“When developing technologies, we are working in closer cooperation with key customers and suppliers, as well as universities and start-up companies,” says Ari Saario, VP for research and development at Valmet.
Valmet has a total of 16 technology centers focusing on different subject areas in Finland, Sweden and Portugal. Every year, more than 400 man-years and €65 million are used for research and development.
The rise of resource efficiency
The interest in sustainability, resource efficiency, the circular economy and responsibility started to rise in the beginning of 21st century. The competition started on who uses the least amount of raw materials and energy.
“This also changed the focus of product development. And the change resulted in another leap, as we had to develop new types of tissue and board machines,” explains Ari Saario.
Another strong development trend is lightweighting. Instead of the number of tons, customers now look to performance. “You get larger amounts of products from the same amount of raw materials.”
New raw materials
Another current megatrend is pulp mills becoming bioproduct mills, in which valuable by-products are obtained from raw material streams in accordance with the principles of the circular economy and sustainability.
One important raw material separated in the process is lignin, which makes up 20–30 percent of wood. Lignin can be used to produce replacements for fossil plastic and carbon fibers, as well as to replace for example fossil substances in glues. In the LignoBoost process special equipment is used to separate lignin during pulp-making.
Pulp is not just pulp anymore, either: it can be micro- or nanocrystalline, or micro- or nanofibrillated cellulose. They provide new materials, for instance, for the textile industry.
A new trend can also be seen in manufacturing through 3D printing. It is being developed at a Valmet research center’s pilot plant in Sundsvall, Sweden. 3D printing is associated with many new generation devices. Metals can be used to print spare parts for machines, among other things.
“The new manufacturing technology means that a device part can be designed more efficiently than before, saving material,” Saario says.
Fuel flexibility at the forefront
Renewable forms of energy and energy saving are reflected in product development. The flexible use of fuels is at the top of power plant procurement criteria, together with cost efficiency.
Since the 1980s, product development has been driven by a significant cluster of the industry operating throughout the Nordic Countries, as well as a large number of experts working for technology companies, customers, universities and research institutes. There have also been several large-scale research programs in Finland related to power and recovery boiler processes.
“At that time, there was no shortage of creativity and boldness. Start-up initiatives were innate in companies, and controlled risks were taken. Products were also developed in connection with delivery projects,” says Matti Rautanen, who manages the networking of Valmet’s energy sector research work with stakeholders.
Valmet’s current expertise in the energy industry, the focus areas of research and success culminate in multi-fuel boilers. ”The wider the fuel base, the better customers can optimize from technical and economical perspectives what kind of raw material, and at what price, should be burned and which sidestreams should be utilized,” Rautanen says.
In the energy field, the company’s areas of special expertise include bubbling fluidized bed, circulated fluidized bed and gasification technologies. As new items, various biomass refining technologies are being studied.
“The bubbling fluidized bed technology is suitable for fuels with a low thermal value, and the circulated fluidized bed technology enables a wider selection of fuels. The expertise has made it possible to raise steam parameters to a higher level,” Rautanen says.
Both in the energy field and in the pulp and paper industry, measuring technology and automation have been an essential part of the process. In maintenance operations, preventive maintenance and lengthening the operating cycles between maintenance breaks have been a focus of development.
A leap forward with Industrial Internet
New leaps in Valmet’s product development are aimed at the Industrial Internet and digitalization. “This year, Industrial Internet and digitalization are a special focus area in our R&D,” Ari Saario says.
Automation and measuring devices guide the pulp, paper and board industries into utilizing resources more and more efficiently. One part of Industrial Internet is virtual reality. With the help of diagnostics, services and maintenance have also taken a leap forward.