Colored tissue says goodbye to nuclear basis weight, Metsä Tissue Žilina
With good results following a recent quality control system (QCS) upgrade on tissue machine 1 (TM1) at Metsä Tissue’s Žilina mill in Slovakia, a second IQ Fiber measurement has now been installed on TM2 producing colored tissue. Simultaneously measuring fiber weight and moisture, Valmet IQ Fiber has replaced the traditional nuclear basis weight sensors. Successfully installed on over 140 tissue machines using virgin pulp to 100% recycled furnish, the need for nuclear safety training and licenses as well as the specialized service and safety requirements have been eliminated.
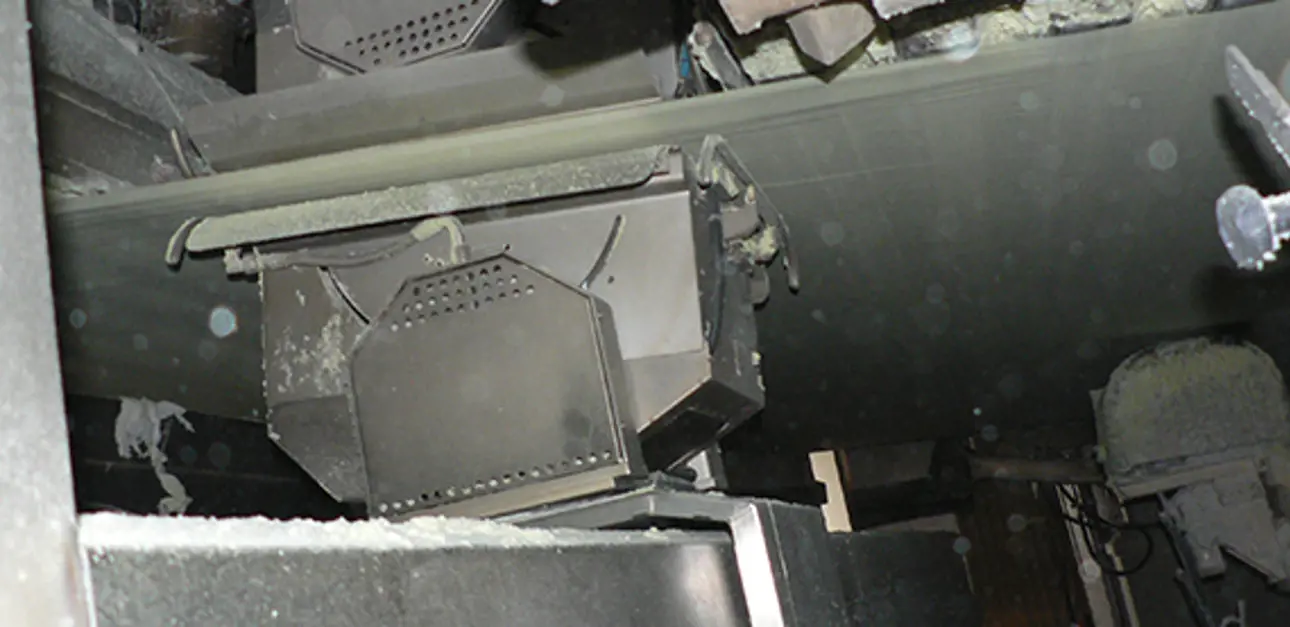
Nuclear basis weight sensors have for many years
been the standard for scanning the tissue web. They are capable of very precise
repeatable readings but over time, noise in the measurement signal requires
additional filtering as the nuclear source decays (Figure 1).
Figure 1. An example of single scan unfiltered basis weight profiles, IQ Fiber in green compared to the noisier nuclear sensor in blue.
To provide an oven dry basis weight reading for control purposes, infrared moisture sensors are normally positioned alongside. Infrared technology developed by Valmet has been refined to the point where it can measure oven dry basis weight (fiber weight) with the same precision and simultaneously measure moisture. By combining both measurements in the IQ Fiber sensor, Valmet has considerably reduced lifecycle costs of servicing and spare parts and eliminated the need for nuclear safety training and handling procedures. The accurate scan averages and high-resolution CD profiles measured by IQ Fiber provide a solid foundation for machine- and cross-direction oven-dry weight controls.
Valmet upgrade
Faced with obsolescence of the old basis weight and moisture sensors and gradually worsening results as the basis weight nuclear source reached end of life, the QCS on Žilina's TM1 was upgraded in 2013. As well as replacing part of the control hardware, the TM1 scanner was upgraded to enable the installation of the IQ Fiber measurement.
Stefan Matak, automation system engineer |
As with any new technology like IQ Fiber, comparison to earlier methods is of great interest and according to Stefan Matak, Automation System Engineer in the Žilina mill, the new measurement is more stable than the old nuclear sensor and moisture measurement. "Repeatability is better than before and the sensitivity to head geometry and dirt is less critical," he says. "As in all tissue mills we have a lot of fiber particles in the air but cleaning once per day is the only maintenance required in over a year of operation."
With good results from TM1 producing white tissue grades, the mill's attention turned to TM2 and colored tissue. Samples were sent to Valmet's Tampere R&D facility to evaluate the effect of color and ash content on the measurement (Figure 2). The Žilina mill produces tissue from either 100% virgin fiber with about 0.5% ash or totally recycled furnish, having an ash content up to 3%, depending on tissue grade. As expected by Valmet's Marko Toskala, Valmet product manager, the results confirmed that IQ Fiber would work well with the different colored tissue grades and varying ash on TM2. "Different colors are handled well by the measurement principle, only very black should be tested with paper samples beforehand," he concludes.
![]() |
Figure 2. Trial results from mill samples showed the accuracy of IQ Fiber was not affected by the different colored tissue produced at Žilina. |
Good results on colored grades
Dusan Planeta, production manager |
The upgrade to TM2 took place in June 2014 and according to Stefan Matak the results have been good with no problems, "The new sensor is a very good replacement against the old nuclear sensor. It gives the same or even better measurement quality for both basis weight and moisture." Determining the parameter change tables for the all the tissue grades being produced is still ongoing, but basic tuning for MD-control has been done and total average values are now better when in automatic control. For Dusan Planeta, production manager, the change to IQ Fiber has been painless with the results on colored tissue as good as white, "We have had very good results with new measurements and a very big advantage is that there is no need of a radioactive source anymore. The new sensors are easier to maintain and all the yearly nuclear procedures and costs can be saved now."
Metsä Tissue's mill in Žilina is one of the company's European tissue sites. With its high-quality tissue and cooking papers, Metsä Tissue is a leading tissue paper products supplier to households and industrial consumers in Europe. Metsä Tissue is also the world's leading supplier of baking and cooking papers. Their main brands are Lambi, Serla, Mola, Tento, Katrin and SAGA. With production units in six countries, Metsä Tissue employs a total of about 2,800 people. Metsä Tissue is part of Metsä Group.