Asia’s largest biomass power plant operates with Valmet DNA
The Dangjin plant near Seoul in South Korea is the largest biomass power plant in Asia. It uses a mix of agricultural and associated by-products. The plant generates 105 MW electricity and the demanding process is run with Valmet’s latest technology, Valmet DNA.
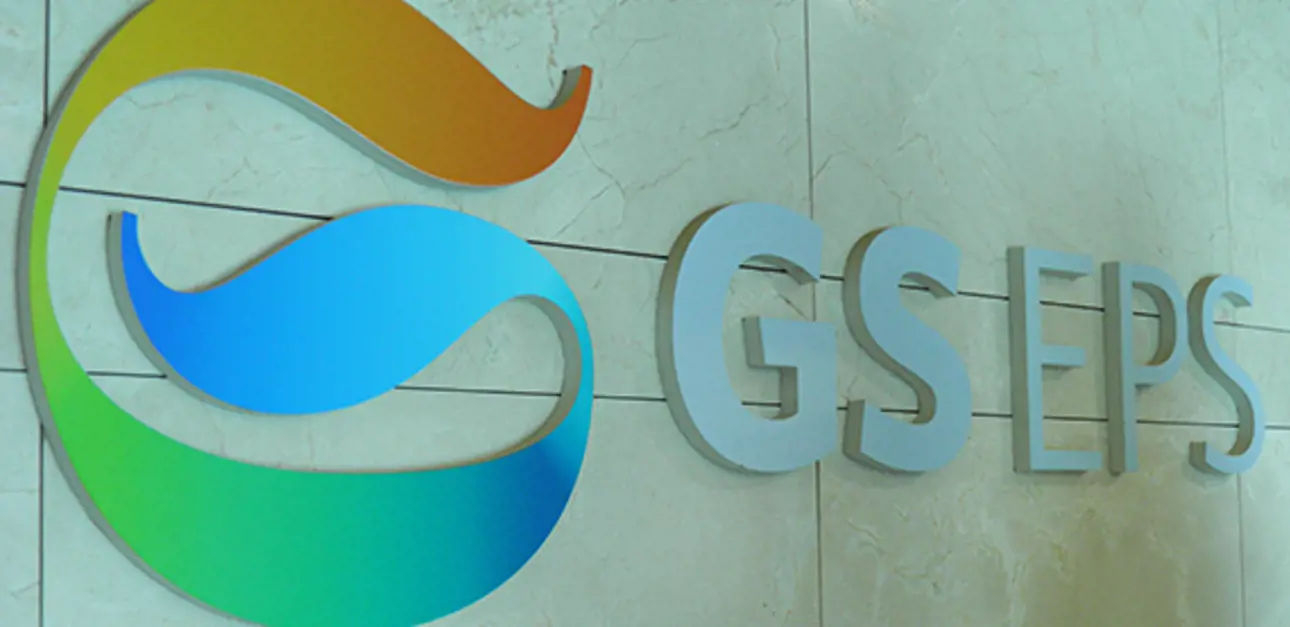
GS Engineering & Construction Co., Ltd. (GS E&C) in Korea has chosen Valmet to supply automation for the Dangjin Biomass Power Plant. The plant started up in August 2015. The advanced automation solution makes the process easy to control.
Valmet’s references were decisive
The power plant site is operated by GS EPS. The site consists of three other power plants that are LNG-fired combined-cycle power plants, 1–3. With this newly started biomass power plant, owner GS EPS aims to enhance its competitiveness in the power market, increase its electricity capacity and produce more renewable energy. “We have chosen Valmet because the company has many references from demanding biomass-fired power plants. It also fulfilled our technical support requirements,” says Gye Man Jeong, General Manager, GS E&C.
The plant is fueled with a mix consisting of 80% palm kernel shells and 20% coal. With Valmet’s advanced automation applications, it is possible to control even these difficult fuel mixes with varying fuel ratios.
Automation system covers the whole plant
|
JeongHo Ahn, Maintenance Manager |
Valmet DNA automation system is in use for the whole bio power plant, including the CFB boiler, Balance of Plant, fuel handling system and electrical network. At the plant, there is a main control room and another one for the fuel field.
JeongHo Ahn, Maintenance Manager of GS EPS, explains that the use of biomass is very important for the company and its sustainability progress. GS E&C has launched a wide energy management program where the greenhouse gas emission level assessment and measures to reduce emissions, for instance, play a key role.
To be aware of the environmental values status, JeongHo Ahn is able to follow the values through the automation system. He is very familiar with the plant’s automation solution.
The main control room is run by five operators who are working daily with Valmet DNA. In the beginning, the technical descriptions in the user interface have been used regularly. Now, when the operators have learned the features of the automation technology, these are not used any more so frequently. But they are certainly useful when educating new operators to do the work.
Flexible operation means a smooth process
![]() |
DNA Operate is the operator interface of the automation system and is executed in the operator stations. DNA Operate is used for all operation and monitoring, including graphic process control displays, event and alarm displays, loop windows and interlocking windows among others. For the users, it is important to know what has happened in the process and what are the reasons behind the events.
The history can be easily seen and analyzed, which JeongHo Ahn emphasizes. “The history replay feature makes the follow-up easy. We can also learn the roots of the disturbances and alarms, which is essential when running the process. With the drag and drop trend analysis, the timeline can be visually presented. The visual elements are quick and more informative to look at,” he explains.
DCS – a tool for the operators
“The more user friendly the automation system, the better the operators can utilize it. For me, it is most important that the heavy users, the operators, can make good use of the automation system. The initial training was given by Valmet experts, and it was a good start to learn the process. Then you can learn more by doing,” states JeongHo Ahn.
First thing every morning, JeongHo Ahn checks what has happened during the night shift. Luckily, he has an impressive tool, Valmet DNA, which offers much more than just following the process. For him, it is significant to analyze the alarms to further develop the process.
Information is power
|
The information coming from Valmet’s monitoring and reporting applications is regularly used by the management. There are many parameters which can be followed, for instance, the fuel data and performance of the power plant and steam turbine. Real-time reporting is based on concrete measurements.
Valmet’s heat exchanger performance monitoring provides the bio plant maintenance personnel with a powerful tool to detect problems and deviations in the heat balance. Furthermore, with the thermal stress monitoring, the personnel can follow the heat situation that contributes to the economical operation of the boiler. In power generation, like in many other industries, correct information at the right time clearly contributes to the success of the business.
Bio plant with attitude
Now, the project is completed successfully and JeongHo Ahn remembers the project phases with pleasure. The planning phase was completed professionally; the installation and start-up were executed ahead of schedule. During the entire project, information was shared openly between the customer and Valmet. This helped demonstrate the expertise of Valmet’s engineers.
Now, when Asia’s largest bio plant is producing electricity on a regular basis, the plant management can be proud of its achievement, which was accomplished successfully together with Valmet.
More information: Matti Miinalainen
matti.miinalainen at valmet.com
![]() |
![]() |