A perforated Valmet Uhle Box Cover proves a success at Propapier PM 2
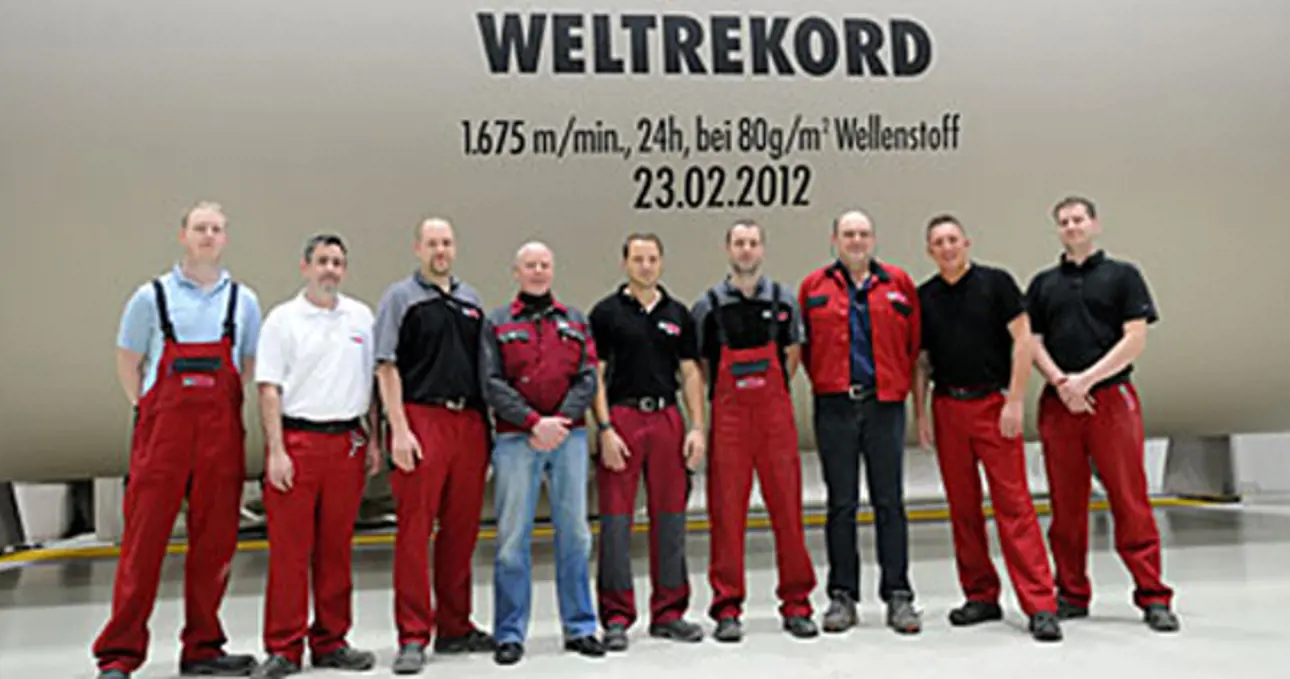
Propapier PM 2, in Eisenhüttenstadt, Germany, has been turning recycled paper into 60 to 115 g/m2 lightweight and ultra-lightweight corrugated board base paper since March 2010. This 10.85 m wide OptiConcept machine has already demonstrated its capabilities by setting new world record speed three times.
Despite the machine’s excellent performance, sheet dewatering still needed a boost, especially at the bottom felt of the first press. There were two Valmet Uhle Boxes in each felt loop, which meant high airflow demand and consequent high vacuum system energy consumption.
Dewatering improves immediately
Valmet (until Dec. 31, 2013 Metso Paper) supplied a perforated Uhle box cover for PM 2 in December 2011. Dewatering increased substantially at the bottom felt of the first press right after installation. In addition to better dewatering, vacuum utilization was reduced by more than 20% (see graph).
A Uhle box with a slotted cover was also tested. However, it provided only half the dewatering capacity of a perforated cover. The felts were washed in connection with the installation of the perforated cover, which made dewatering somewhat easier.
A perforated Uhle box cover contributes to better dewatering as well as better machine runnability.
“The perforated cover now allows us to reach the same level of dewatering, but with 30% lower vacuum than before with two Uhle boxes,” says Peter Resvanis, Production Director, Propapier PM 2. The mill has taken the second Uhle box completely out of service.
“Better dewatering at the first press can also be seen after the press section. We have noted better dryness after the press section and lower steam pressure at the dryer section when dewatering with the perforated cover is maximized,” Resvanis continues. “A smooth moisture profile before the sizer is also very important, and we have achieved excellent profiles with the new cover.”
The performance of a perforated cover is based on a long dwell time and a consistent vacuum applied over the whole perforated area. In addition to better dewatering, a perforated Uhle box cover also contributes to better machine runnability.
Reduced vacuum saves energy
Propapier PM 2 used to employ two blowers to generate the required vacuum for the Uhle boxes. After installing the perforated Uhle box cover, the mill has been able to retire one of these blowers and thereby save energy. A reduced Uhle box vacuum also curbs friction and cuts drive power demand.
Reduced vacuum and airflow requirements have made it possible to further optimize the performance of the press section vacuum system.
Longer felt running times
The good felt support and conditioning performance of a perforated cover facilitate longer felt running times. The felt is fully supported and there are no slots in the cover for the felt to dip in. This helps in situations where the felt hair may be getting loose, for example, and good felt support is also gentler on seamed felts.
Dewatering and Uhle box vacuum at the bottom felt of the first press.
The better felt conditioning performance of perforated covers than slotted covers is based on a long dwell time over the perforated area. This better condi-tions to the vacuum system may also be required to take full advantage of the new cover. It is therefore advisable to follow up the installation of a perforated cover with a vacuum system audit and update. If the system’s pumps or blowers are controlled by means of frequency converters, the resulting savings will be immediate.
A Valmet Hard Coating Solid* -coated Uhle box cover can be installed on any box type. Installation is easy, and Valmet can provide coating inspection and recoating services as needed.
More than 20 Valmet-supplied perforated Uhle box covers are already running in paper machines around the world, with excellent results. Additional Uhle box dewatering was needed in most of these cases, with the remainder focusing on vacuum energy savings.
Many of these machines have adopted this cover solution for their other felt loops as well. Propapier also recently ordered a second cover for PM 2 and another for PM 1.
*earlier known as SolidCoat