6,600 kilometers from Finland to India - the Ballarpur Industries pulp mill relocation project
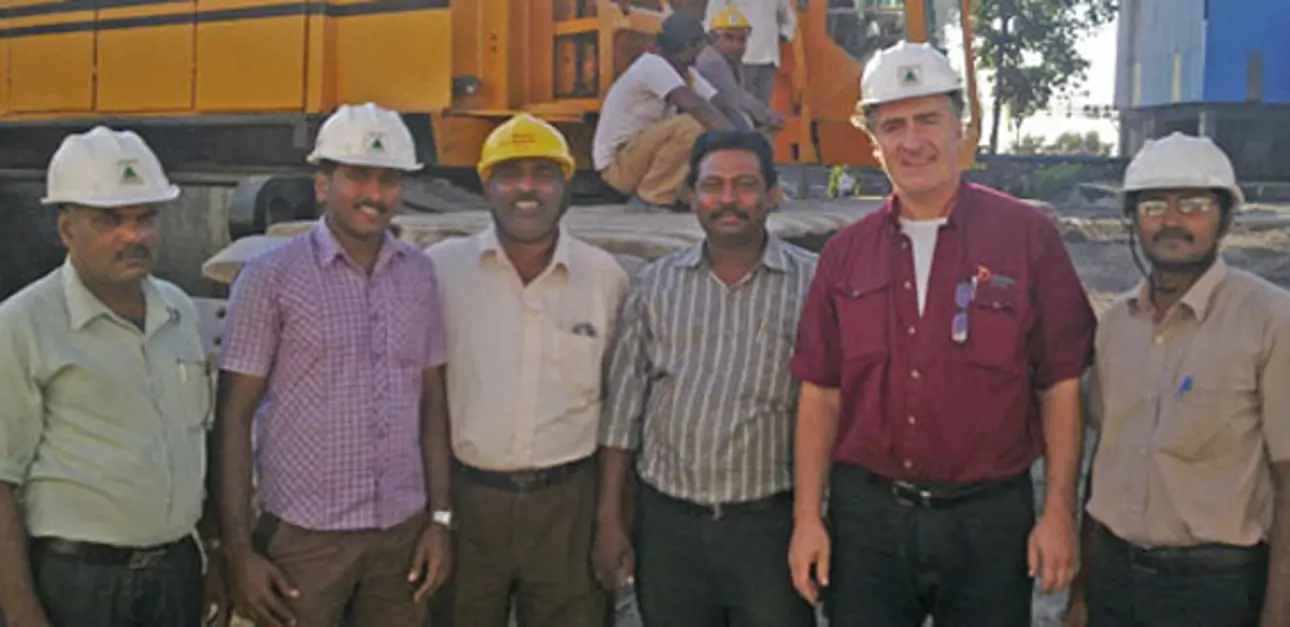
Happy project team after a successful relocation achievement.
Re-locating an entire pulp production line from one corner of the world to another is a sizeable venture. Ballarpur Industries proved that it can be done successfully by combining the right resources. A pulp mill that has been up and running in Finland for 40 years is now continuing to produce pulp in a new location in India.
How did it all start?
The pulp mill, the oldest one in the Metsä Fibre (former Metsä Botnia) group, was located in Kaskinen, in western Finland. In March 2009, after approximately 40 years of operation, the mill was closed due to low profitability level. Judging by age, the plant may have seemed old. However, many of the areas – e.g. the chemical recovery segment and, especially, the evaporator plant and the recovery boiler - had gone through many upgrades, including a major one in 2008.
Ballarpur Industries (BILT), a premiere group of companies and the largest manufacturer of writing and printing paper in India, were studying alternatives for expanding the pulping capacity at their Ballarpur plant. The main reason for choosing mill relocation was the decision to go for the capacity expansion at the lowest possible cost. The closure of the Kaskinen mill came up in a global study of pulp mills available for sale.
BILT involved Valmet in the Ballarpur project already before closing the contract for the Kaskinen mill’s machinery and equipment relocation in June 2010. Valmet made preliminary mill balance calculations for the mill expansion and committed to providing project execution if BILT were to purchase the mill.
The former Kaskinen pulp mill made a long journey from Finland to Ballarpur, India.
A trusted partner for a big challenge
Disassembling a paper or pulp production plant, shipping it to a new location, re-installing it and adding a new automation system successfully require deep process expertise and strong experience in global project management. Valmet’s way of working on an expansion project at another BILT mill in South East Asia had convinced BILT of Valmet’s capabilities.
BILT also appreciated Valmet’s modifications to the design to make the mill suit the local requirements in India. In addition, the local teams of the two companies had collaborated for more than 25 years, successfully handling several critical rebuild projects. Valmet’s commitment to providing full support in order to successfully relocate the mill to Ballarpur also supported the decision to choose Valmet.
Valmet’s scope covered dismantling supervision and re-engineering, as well as erection and commissioning services for the evaporator plant, the chemical recovery boiler and the recausticizing plant. The scope included all the necessary engineering and site supervision services for the dismantling work in Finland and shipping to India, and all the services needed to set up the plant in Ballarpur and get it up and running.
Key changes carried out:
Evaporator plant | Recovery boiler | Recausticizing plant | ||
Design changes to reduce the capacity from 500 TPH to 360 TPH to suit BILT requirements, including foul condensate stripper modifications (plugging of many trays in the existing stripper). | Design changes to reduce the capacity from 2,320 TPD to 1,150 TPD with a provision to fire 1,650 TPD in the future. | Design changes for reduced plant capacity from 5,500 m3/day to 2,750 m3/day, and integration with the existing causticizing plant, the capacity of which is 1,350 m3/day. The total causticizing capacity is 4,100 m3/day. Integration of the new modified plant to the existing plant. | ||
Conversion for the falling film design on one of the LTV bodies, and supply of minor critical equipment needed in this work. | Incorporation of both CNCG and DNCG firing systems. Standby flare burner design and specifications for new flare burner (supply by BILT). | New conventional clarifiers were installed in the tube filters: high-silica-content lime – as high as 5% - must be handled in white liquor filtration. | ||
A totally new mill layout in line with the Ballarpur plant layout. Many challenges were faced during the layout engineering due to the confined space. | Entire structural design, including a stress analysis in line with the conditions at the Ballarpur mill. New design for a new structure and integration with the old structure, and strengthening of the old structural material based on the results of the stress analysis to suit the local seismic conditions. | The tube filter from the Kaskinen mill was installed to operate as a white liquor polisher. | ||
Last-minute engineering support for a bigger-size evaporator cutting plan in line with the existing logistics constraints. | Design and specifications for missing and damaged pressure parts. Supply of critical missing and damaged pressure parts, including rebuilding the tertiary and quarternary superheaters and superheater bottom tubes with 310H material. | New conventional clarifiers were installed in the tube filters: high-silica-content lime – as high as 5% - must be handled in white liquor filtration. |
Project support
|
Putting the pieces together
The project involved an extensive amount of specialist work. Managing the relocation of an entire pulp mill was enabled by Valmet’s ability to provide the technology, services and know-how for the fiberline, recovery and automation. Seamless collaboration between the Valmet teams from India, Finland and Sweden, as well as Ballarpur Industries and a local consultant company ensured that the work could be finalized on schedule.
Project well appreciated by Valmet participants
Anshul Mishra, Sales Manager, Valmet, Asia Pacific, says: “As a global technology solution provider, we bring the best technology know-how to our customers to help them in achieving production targets without compromising on environmental performance.”
B Syam Sundar, Director Sales, Valmet, Asia Pacific, is very enthusiastic about the success of the project: “We are a global technology solution provider and our first mission is to understand the needs of our customers. While there is always a local way to do business, Valmet also brings the best of global practices and technology.”