Process upgrades for energy producers
Improved capacity with process upgrades for energy producers
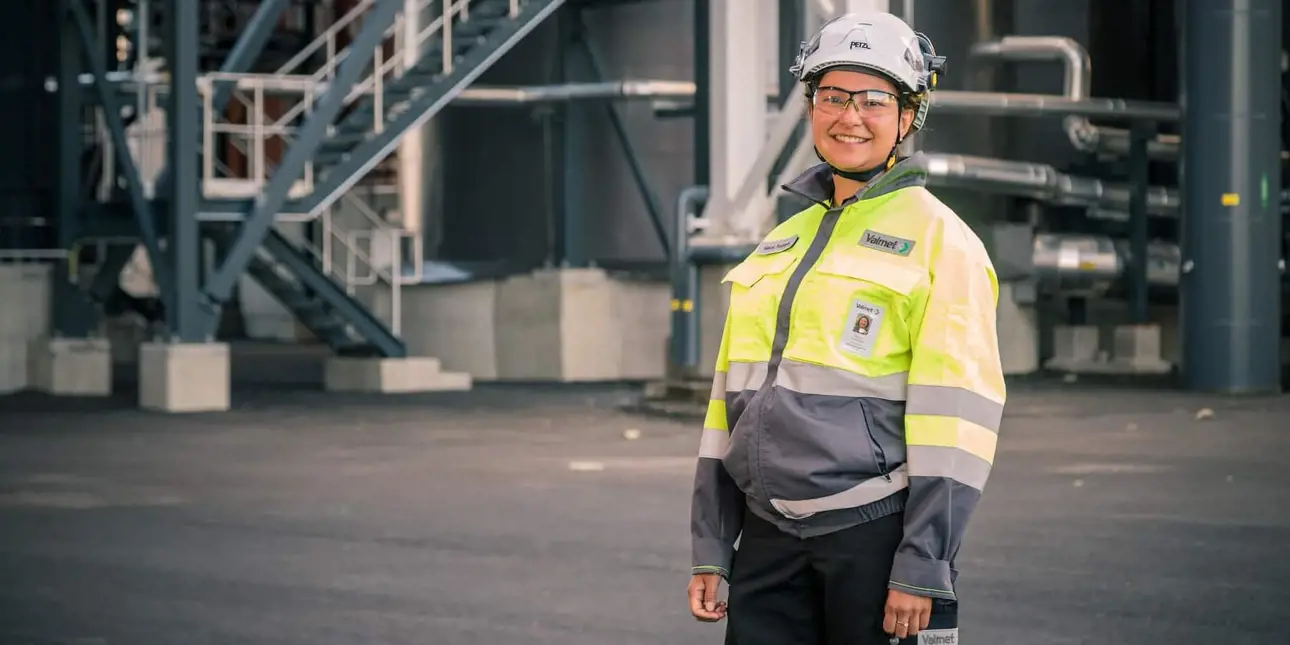
How to maintain the competitiveness of your core processes and to develop them throughout the lifecycle? We provide a wide range of solutions for upgrading and enhancing processes and machinery. The scope is always based on your specific needs and the solutions are tailored to maximize the performance of the processes. This can be a cost-effective way to improve capacity, reduce emissions or extend the lifetime of your equipment. As a leading technology expert in energy, we have extensive expertise and experience. This knowledge is incorporated in all our products, giving us exceptional insight into all aspects of upgrading processes and equipment.
Small investments to remove bottlenecks
With small or mid-size investments production bottlenecks can be opened or extend the original process design limitations. Typical process upgrade building blocks are design engineering, new components, rebuild and upgrades and process controls and efficient commissioning and start-up service.
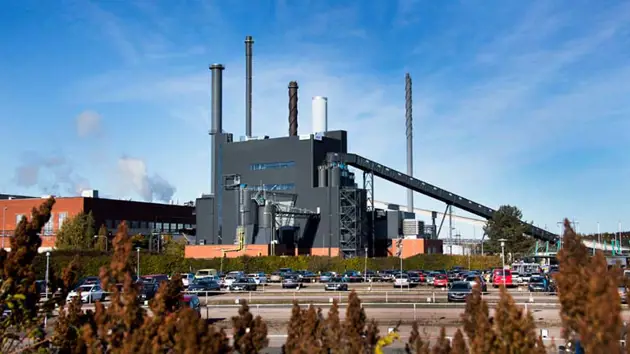
Fuel and combustion management for energy
Use low-priced fuels without increasing the risk of superheater corrosion with Valmet Superheater KCl Corrosion Management and reduce your yearly fuel costs. Alkali chloride induced corrosion is one of the major risks and reason for superheater maintenance needs in biomass and recovered fuel firing boilers in power generation industry. The corrosion rate can be very high and may cause non-predictable failures and immediate need for shutdown.
The solution provides tools to control the risk of alkalichloride induced superheater corrosion, save in fuel costs, increase transparency in power plant’s daily fuel and combustion management and gives real time estimate of the remaining lifetime of the superheaters.
Do you want to know more about process upgrades?
If you wish to get further information like technical specifications, need a quotation, or wish to discuss different solutions, fill in the contact form and our experts will contact you shortly.
Contact usMinimizing the CFB-boiler minimum load
With Valmet’s minimum load solution for CFB boilers, the operation range can be expanded downwards. Partial bed operation of your CFB-boiler allows you to reduce fuel costs and use less fossil fuels.
Partial bed operation is achieved by operating the boiler with a smaller fluidized bed area than originally designed. This ensures smooth boiler operation below the original minimum load point while meeting environmental limits. The solution only affects the low load operation, while the max load remains unchanged.
Partial bed operation enables you to:
- Operate your existing biomass boiler below the original minimum load.
- Use normal biofuels throughout the low heating season.
- Minimize the need to operate back-up boilers with fossil fuels when the heat demand is low.
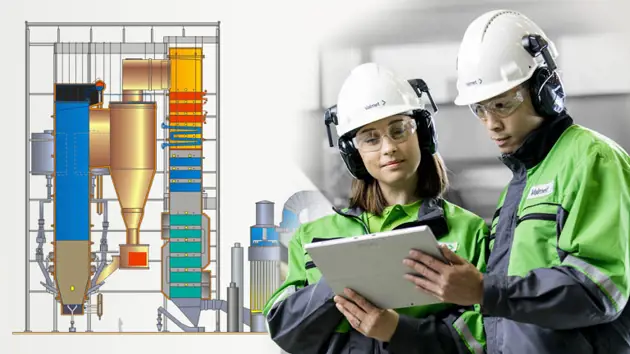
Explore our CFB and BFB boiler services offering
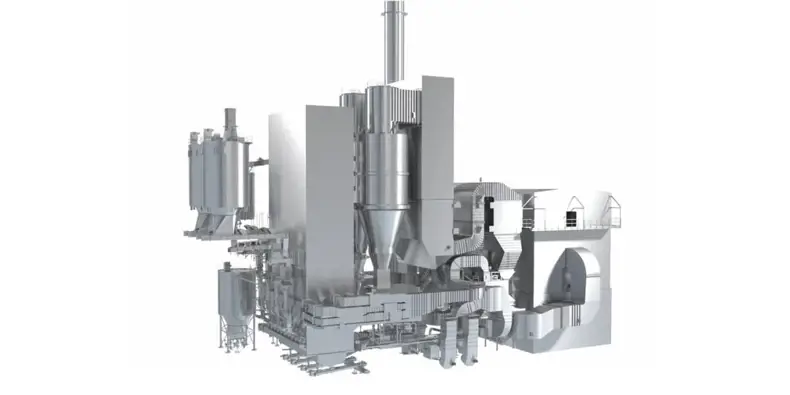
On this image
-
1 Boiler Inspections
-
2 Boiler Combustibility Study
-
3 Waste fuel feeder
-
4 Superheater KCl Corrosion Management
-
5 Energy spare parts
-
6 Services for air emission controls
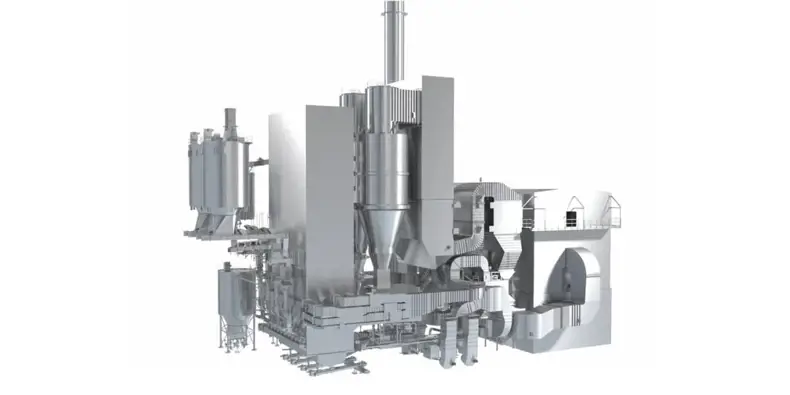
Boiler Inspections
Boiler Combustibility Study
Waste fuel feeder
Superheater KCl Corrosion Management
Energy spare parts
Services for air emission controls
References and articles
Related pages
