Controlled and efficient water management solutions and technologies
Water management for board and paper
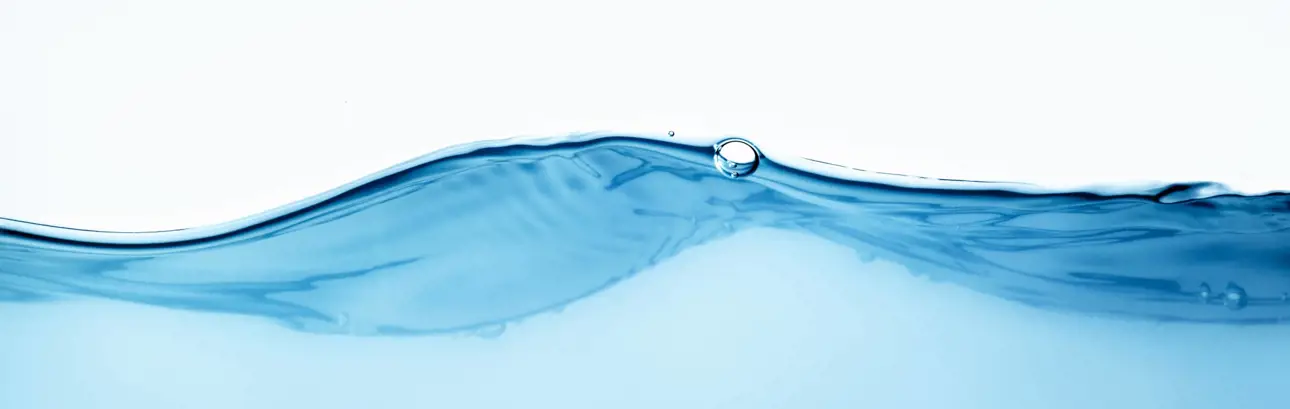
Effective water management is essential to driving quality, sustainability, and cost-efficiency in paper and board production. With Valmet’s water management solutions, you can minimize fresh water consumption, streamline wastewater treatment, and reduce scaling and energy costs.
Fresh water savings
Decreased operational costs
Reduced energy
Extensive water concepts for different needs
From reducing fresh water intake and optimizing internal water cycles to managing complex wastewater treatment, Valmet’s comprehensive water management concepts are designed to meet the diverse needs of paper and board producers across varying water consumption scenarios.
Effective water management is crucial in papermaking, as detrimental substances in the water can significantly impact production. These substances can reduce the effectiveness of additives, affect optical and strength properties, and cause issues with sizing, odor, drainage, and drying. For example, high salt concentrations can corrode machine parts and diminish the effectiveness of additives, ultimately affecting the paper’s strength. With advanced technologies and deep expertise, our concepts enable you to achieve reliable water quality, minimize environmental impact, and enhance overall process efficiency.
Examples of Valmet's water management concepts
Here, you can learn about three different water management concepts designed for board production processes. These concepts are based on the amount of fresh water the production line uses. To ensure the paper machine operates optimally, certain basic conditions must be met:
- Directing all fresh water to the paper machine
- Using the counter-current principle for all process water, ensuring water flows opposite to the product flow for maximum efficiency
- Moving all makeup water from clean to dirty, using cleaner water first
- Maintaining stable process conditions, avoiding variations in temperature or pH levels
- Discharging wastewater from the pulp mill, keeping it separate from paper machine processes
- Maintaining separate water loops for different departments to prevent cross-contamination and ensure efficient water use
- Efficiently washing pulp before it reaches the paper machine, using pulp presses
All our concepts include fresh water and effluent water treatment plants and sludge handling. The main difference between these concepts is the increase in hydraulic capacity of the wastewater treatment plant (WWTP) as fresh water consumption decreases. The less fresh water used in the mill, the more water must be recirculated back into production after various wastewater treatment stages at the WWTP to maintain water quality balance.
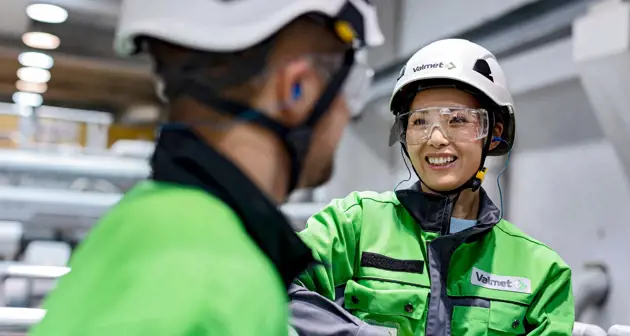
Want to learn more?
Valmet’s water management solutions are built to optimize every step of your water processes. When you partner with Valmet, you benefit from a complete water management solution tailored to meet the demands of modern paper and board production, unlocking efficiency, reliability, and a sustainable future.
Contact usCurrent standard level with low fresh water consumption (5 - 7 m³/t)
Nowadays, typical fresh water consumption of a paper machine with best available water technologies is around 5-7 m³ per produced paper tonne. Preconditions have been taken care of and the machine runs smoothly. There is still potential to reduce fresh water consumption further.
OCC liner fluting line with fresh water consumption of 5-7 m³/t (effluent water 3.5-5.5 m³/t)
Minor fresh water consumption (3 – 5 m³/t)
When using less fresh water, process water needs to be treated more effectively to remove contaminants before it can be reused or discharged. Otherwise, high concentrations of contaminants can negatively affect the cleanliness and operation of the paper machine. Therefore, we need technologies to keep the water clean and prevent operational risks.
Ultrafiltration and dissolved air flotation are the key technologies in paper machine's internal water treatment. Dissolved air flotation for press section waters removes fines and pitch improving runnability. Valmet Ultrafiltration W removes solids, colloids, microstickies and bacteria from the paper machine’s clear filtrate. Ultrafiltration permeate can be used in paper machine’s showers instead of fresh water. When fresh water consumption is below 5 m³ per tonne of produced paper, pulp presses must be used in stock preparation.
OCC liner fluting line with fresh water consumption of 3-5 m³/t (effluent water 2.0-3.5 m³/t)
Minimal fresh water consumption (<3 m³/t)
When water consumption is very low, risks increase and more water treatment is needed. For example, if water treatment is not properly managed, increased salt concentration (conductivity), especially chloride ions, can lead to retention issues and machine corrosion. Therefore, advanced treatment of biologically treated water is required when fresh water consumption is below 3 m³ per tonne of produced paper.
With the combination of dissolved air flotation, membrane technology, and activated carbon filtration in advanced treatment, we can polish biologically treated water to fresh water quality, thus eliminating corrosion problems.
OCC liner fluting line with fresh water consumption below 3 m³/t
Closing the water loops together: strategic partnership with Flootech
Valmet cooperates with Flootech to provide advanced and cost-competitive water treatment solutions to our board, paper, and tissue customers. Through the partnership, Flootech provides profound technical and commercial expertise to Valmet's customers.
The offering includes:
- water treatment and recycling solutions
- process water treatment
- effluent treatment and reuse
- sludge dewatering
- demineralized water treatment
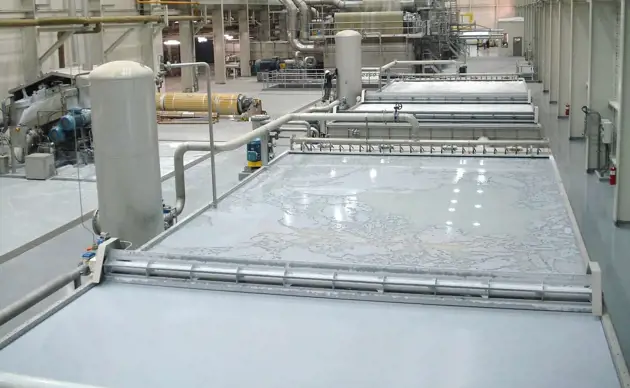
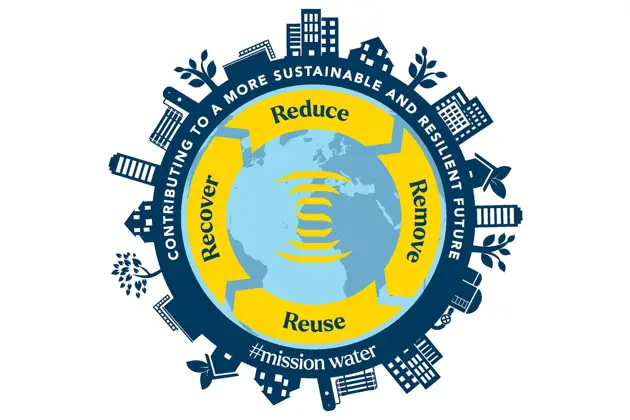
Learn more about Flootech
Do you want to know more about water technologies for board and paper? Valmet partners with Flootech and you can learn more about them from their own website.
Visit Flootech's website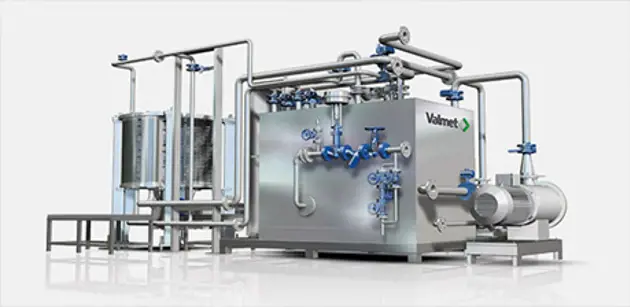
Read more about ultrafiltration
Valmet’s Ultrafiltration process is a solution for paper, board and tissue mills to produce colloid-free, bacteria-free, ultrapure water from white water. The main objectives are to reduce fresh water consumption, improve paper machine runnability, efficiency, and manage energy.
Read moreImprove your existing production line’s water efficiency with Valmet’s services
Enhance the water efficiency of your board and paper making lines with Valmet’s services, even with minor investments. Our technological solutions in fiber process equipment and rolls offer effective options to reduce water consumption, boost production efficiency, and lower costs.
Benchmarking provides a comprehensive view of your water efficiency. We can help you developing your roadmap, knowing where you are, what you can improve and how much, and the actions needed to achieve these improvements.
Minimize water losses with upgraded shaft seals
Reliable shaft sealing is crucial for operating fiber processing equipment like low-consistency refiners, screens, or pulpers. Traditional packing box technology for shaft seals consumes a significant amount of sealing water, typically around 3,800 m³ annually. Standard mechanical seals reduce this to about 1,900 m³ annually. By upgrading to a closed mechanical seal, you can eliminate these water losses.
A closed system keeps the seal water pressurized, minimizing constant flow through the seal, saving energy, and extending the seal’s service life. This is especially beneficial when seal water quality is poor, as harmful particles do not accumulate. Overhauling a refiner, screen, or pulper is the perfect opportunity to upgrade the shaft sealing and improve water efficiency.
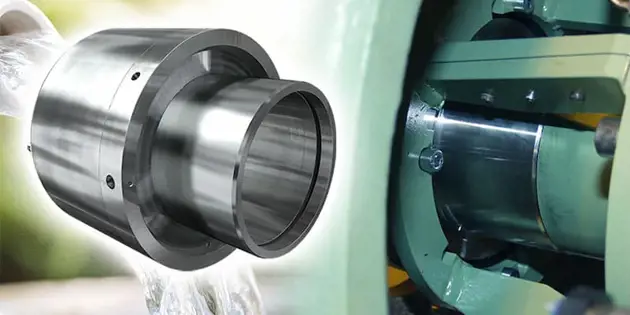
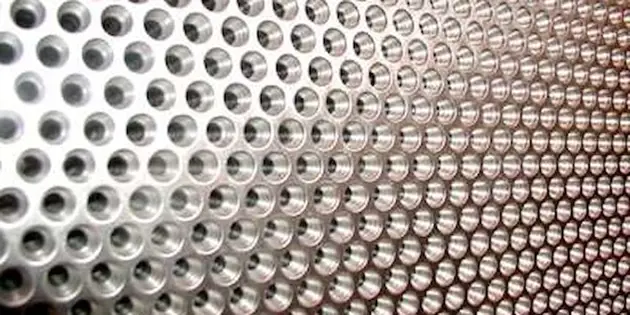
Significant water savings with suction roll upgrades
Valmet’s suction roll upgrades can significantly reduce water consumption while improving the cleanliness and reliability of suction rolls. The Valmet Suction Roll Upgrade Lock Seal relieves seal strips from the suction roll shell during operation, potentially saving up to 100% of axial seal lubrication water consumption.
Another upgrade, the Seal Flow modern axial seal lubrication shower, can achieve up to 50% water savings compared to traditional showers, with annual water savings of up to 30,000 m³ per suction roll machine position. The Shell Flow H upgrade keeps suction roll shells clean with minimal water consumption, saving up to 6,000 m³ annually per machine position when high-pressure showers are used for 10 minutes every eight hours.
Explore our latest board and paper press releases
- Jun 13, 2025Dr. Jin-Doo Kim awarded with a Medal for Extraordinary Achievement for decades-long work for promoting board and paper technologies
- May 26, 2025Valmet to supply a fifth Advantage tissue production line to Lila Group in Turkey
- May 21, 2025Valmet to supply a major paper machine rebuild to Sylvamo in North America
- Mar 27, 2025Successful start-up of Zhejiang Forest United Paper’s PM 6 production line
- Mar 27, 2025Valmet to supply two winders to Wuzhou Special Paper in China
- Mar 6, 2025Valmet to supply a high-capacity winder to Jingxing Holdings in Malaysia
- Jan 21, 2025Valmet to supply an off-machine coater to a customer in Asia-Pacific
- Nov 12, 2024Valmet to supply a complete papermaking line to one of its major customers in Asia-Pacific
- Oct 21, 2024Valmet’s change negotiations completed in Finland in its Paper business line’s Board and Paper Mills business unit
- Oct 3, 2024Valmet to supply an OptiConcept M board making line to Anhui Linping Circular Development in China