Vacuum system improvements for board and paper making
Opportunity for energy savings by optimizing the vacuum system
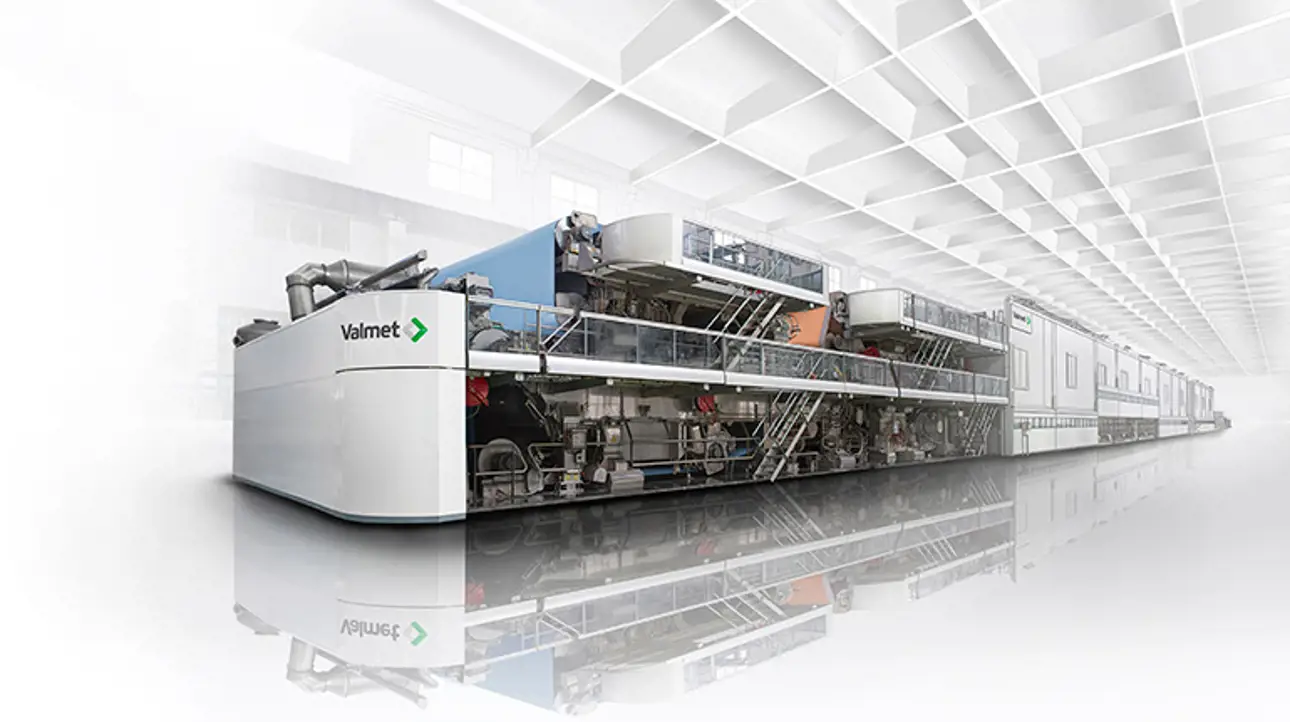
There is vast potential for energy savings in vacuum systems – more than 50% of all paper machines suffer from poor operating efficiency in their vacuum systems. The required modifications are often relatively small compared to the savings gained, and the payback time is short. Most vacuum systems are not designed to operate in current operating conditions – they are highly over-dimensioned and consume too much energy. The increased demand for recycled fiber has a strong effect on fiber quality and therefore presents a challenge to vacuum system capacity requirements. Many vacuum systems also use ineffective pumps. Valmet’s Vacuum System Optimization service reveals these inefficiencies and presents a plan to improve vacuum efficiency or replace the existing equipment.
Better efficiency and improved control
Reduced energy consumption
Immediate savings
Better efficiency, lower energy consumption
Vacuum System Optimization is a comprehensive solution for identifying and realizing significant energy savings in vacuum systems. The primary cause of efficiency losses in a paper machine vacuum system is control of the vacuum level, as efficiency losses can be high when the pump capacity does not match
the requirements of the paper machine. In these cases, the vacuum control logic needs to be updated. In a conventional liquid ring pump (LRP) system, the vacuum is controlled using bleed air, but similar losses can also occur in blower systems when there is a lot of variation in the air flow from the paper machine.
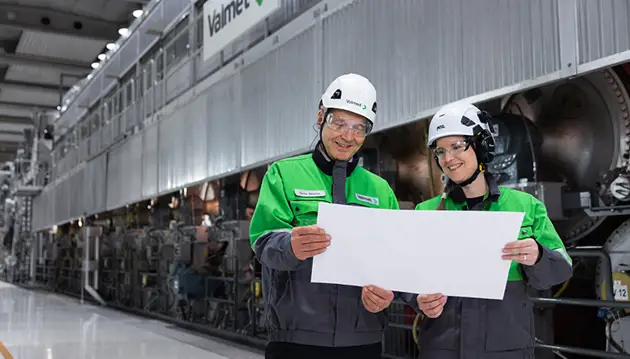
Do you want to know more about process upgrades?
If you wish to get further information like technical specifications, need a quotation, or wish to discuss different solutions, fill in the contact form and our experts will contact you shortly.
Contact us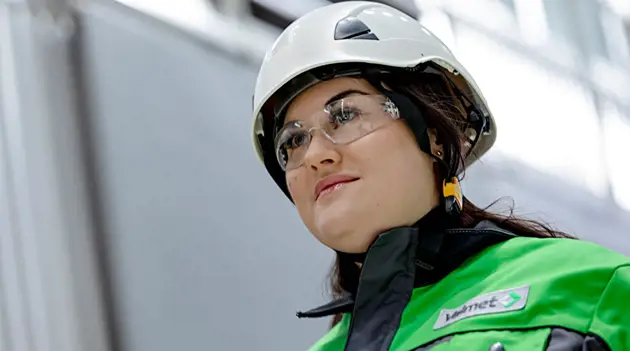
Cost savings with perforated Uhle Box Covers
Perforated Valmet Uhle Box Covers are an effective and straightforward solution for increasing dewatering and reducing energy consumption in the press section. There are two ways perforated covers can be applied: either by replacing the conventional Uhle Box Cover with a perforated one for increased dewatering, or by modifying the existing vacuum system to produce significant savings, and then replacing the cover.
Perforated Uhle Box Covers and the vacuum system study and modifications of Valmet’s Vacuum Optimization combine to facilitate considerable savings in production costs.
Customized on-site study and pre-engineering
Valmet’s vacuum system energy efficiency study begins with either a screening or a more thorough on-site study. The on-site study is used to create a two-phase action plan, with both phases taking a functional approach to optimizing energy consumption.
Rapid results can be obtained with relatively small changes such as optimizing the piping connections and running parameters, and installing new perforated covers. A more extensive approach is also presented that weighs the costs and benefits of long-term investments. As soon as a need for further action is identified, the engineering steps needed are initiated.
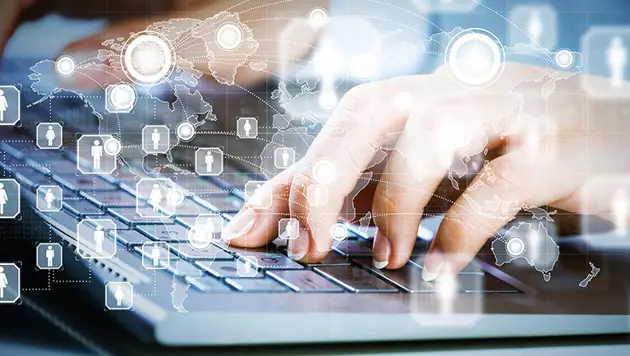
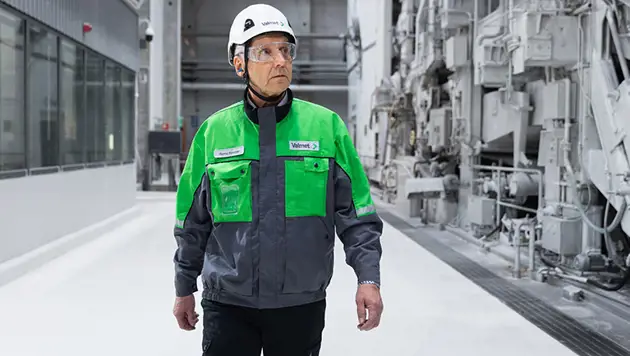
Vacuum System Optimization for energy savings
The vacuum system upgrade itself is usually carried out in two stages. The first stage involves modifying the vacuum controls and pump connections. The second stage, featuring new variable-speed drives, takes place later, as the operation of the vacuum system must be observed for at least two felt life cycles in order to estimate what additional energy savings potential exists. Alternatively, the second stage can employ blower technology to replace water ring pumps.
Vacuum System Optimization is suitable for all vacuum systems with LRP pumps and blowers, regardless of the machine supplier.
References and articles