OptiReel Linear
Safe one-level parent roll handling for trouble-free reeling
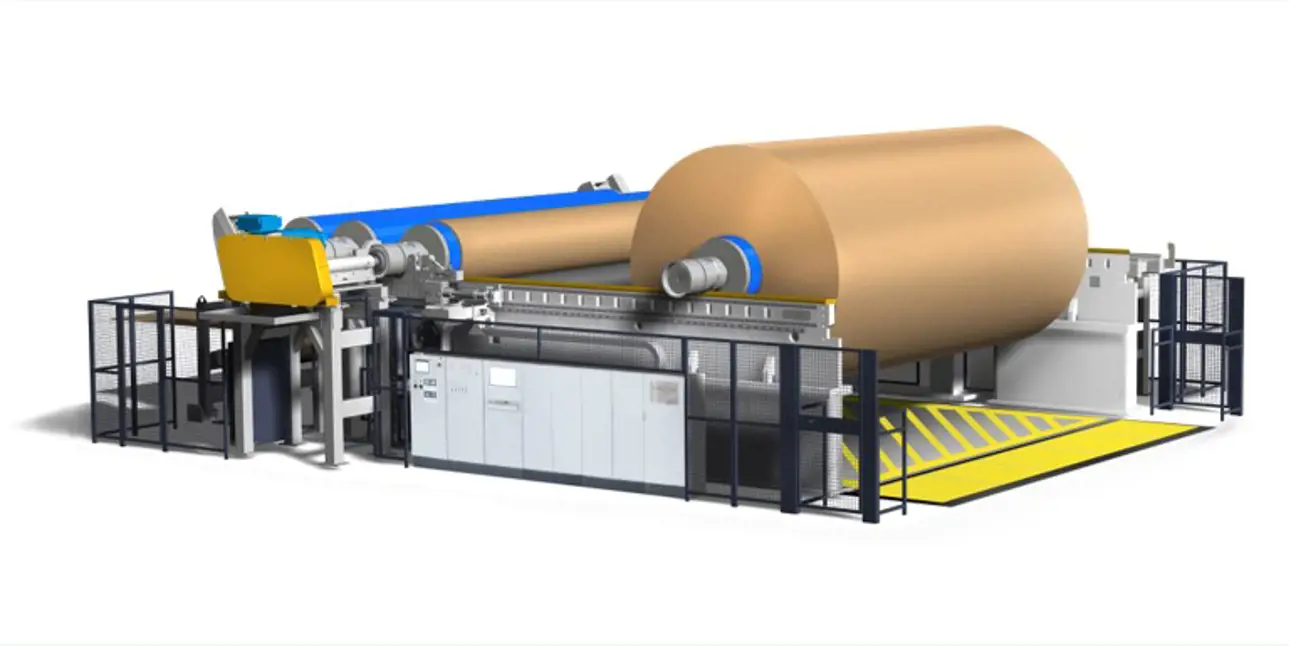
OptiReel Linear is a completely new way to reel paper machine parent rolls. Instead of having a high structure reel spool storage and lowering arms, reel spools and parent rolls are moved on solid rails resulting in a continuous and trouble-free reeling process.
More saleable production
Easy operation and maintenance
Improved safety and reliability
Lower investment and life-cycle cost
More saleable production
Getting more saleable production is a combination of a number of factors. An optimal parent roll structure is achieved by accurate measurements & controls for all reeling parameters. Improved reeling quality for the critical parent roll bottom is a direct consequence of the one-level reeling. Efficient turn-up sequence, fast web break recovery sequence and optional parent roll surface binding minimize the production losses.
Capacity is also increased with OptiReel Linear due to bigger parent rolls. The parent roll size has a significant effect on overall material efficiency and capacity in the finishing area. By maximizing the diameter, it is possible to significantly improve output.
Optional center drives have proven to be excellent for preserving coated board surface and sheet properties. Since they eliminate slippage in the nip and between coated board layers during reeling, it is possible to wind large diameter rolls without scratches, gloss variations, dust or mottling. Furthermore, the possibility to use low nip load level ensures a bulkier sheet and even smoothness values in the top and bottom sets.
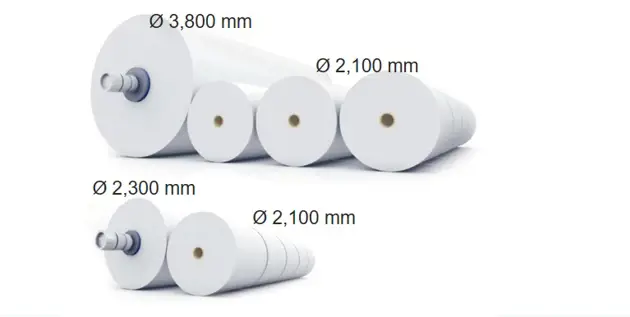
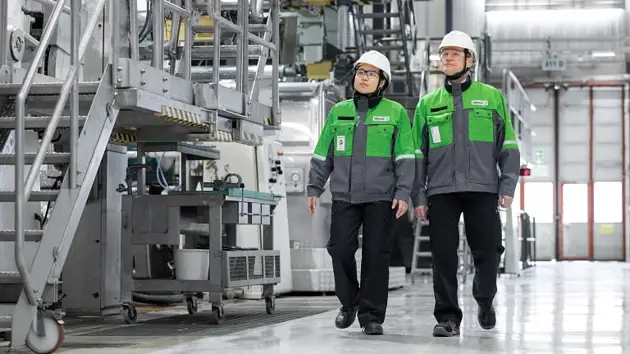
Want to talk to our reeling experts?
If you wish to get further information like technical specifications, need a quotation, or wish to discuss different solutions, fill in the contact form and our experts will contact you shortly.
Contact our expertsCoated board handled with extra care
Center driven reels have proven to be excellent for preserving coated board surface and sheet properties. Since they eliminate slippage in the nip and between coated board layers during reeling, it is possible to wind large diameter rolls without scratches, gloss variations, dust or mottling. Furthermore, the low nip load ensures a bulkier sheet and even smoothness values in the top and bottom sets.
OptiReel Linear with primary center drive is the optimal application for medium-sized production lines. It is suitable for all paper grades and particularly to applications where large parent roll diameter is required to boost the dry end capacity. Parent roll hardness is directly affected by the center drives. See figure below.
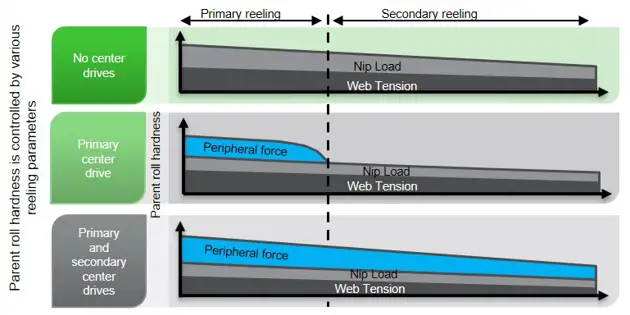
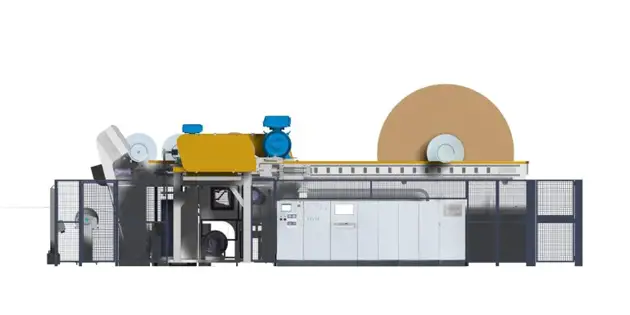
Safe and easy operation and maintenance
Low structure of OptiReel Linear enables easy access to operating and servicing positions. There are no high structures to complicate maintenance actions. Additionally, the constructions on tending and drive side are similar. Optional transfer rails for full parent rolls automate the moving of the parent rolls.
For soft cover reel drums, it is important the reel drum change is fast. In conventional reeling, changing of the reel drum change might take even one day, because the primary reeling device must be dismantled. With OptiReel Linear, reel drum change takes only a few hours. There is no need to dismantle anything from primary nor secondary reeling devices.
One level reeling brings a number of safety related factors: There are no high structures, big roll masses are always frame supported, crane lifting height is smaller, there is no need to elevate spool & parent roll and all the spool and parent roll movements are well controlled.
Interested in pilot trials?
Get in touch with our pilot trial experts to discuss how you could benefit from our pilot trial services.
Contact our pilot trial expertsHow do you plan a successful rebuild?
Rebuilding a paper or board machine can improve the competitiveness of your business and your processes. Download our e-book to learn more.
Download e-bookPlanning a grade conversion?
The world is changing fast; the consumption of papers is decreasing and boards increasing. Update your paper machine with Valmet to produce more profitable products.
Discover moreLearn more about the services and automation solutions for reels
Explore our latest board and paper press releases
- Mar 27, 2025Valmet to supply two winders to Wuzhou Special Paper in China
- Mar 6, 2025Valmet to supply a high-capacity winder to Jingxing Holdings in Malaysia
- Jan 21, 2025Valmet to supply an off-machine coater to a customer in Asia-Pacific
- Nov 12, 2024Valmet to supply a complete papermaking line to one of its major customers in Asia-Pacific
- Oct 21, 2024Valmet’s change negotiations completed in Finland in its Paper business line’s Board and Paper Mills business unit
- Oct 3, 2024Valmet to supply an OptiConcept M board making line to Anhui Linping Circular Development in China
- Sep 5, 2024Valmet to start change negotiations in Finland in its Paper business line’s Board and Paper Mills business unit
- Aug 16, 2024Valmet and Spinnova Plc sign a partnership agreement regarding process equipment for textile fibre production
- Aug 1, 2024Valmet closes the agreement to acquire majority shares in FactoryPal, a subsidiary of Körber
- Jul 8, 2024Valmet to supply operator training simulator to Graphic Packaging International in Waco, Texas, United States