Valmet offers remote support with augmented reality during general shutdown during pandemic
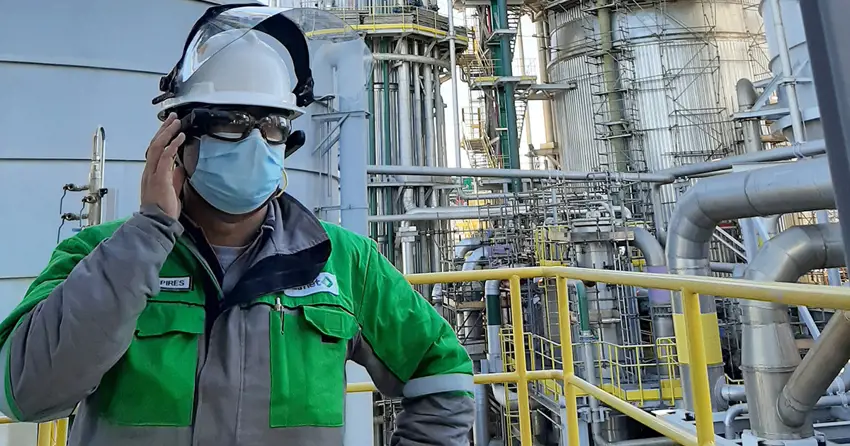
The human relationships have changed dramatically around the world since the start of the new coronavirus pandemic. During the routine of industrial work, companies had to adapt their activities so that safety protocols had priority, without the health of employees being endangered or essential services being interrupted. The use of new technologies has also been an ally in solving problems and optimizing processes through remote service tools.
In this challenging scenario, Valmet provided Industrial Internet solutions for CMPC's shutdown, a mega operation in Guaíba, Brazil, which held for 10 days during pandemic. The company implemented a strict prevention protocol for Covid-19 and used solutions that could remotely solve some of the mill's operational demands.
The augmented reality glasses used during the shutdown helped the field services technicians during the maintenance in Line 2 of the mill. The equipment enabled the detailed analysis of Valmet’s specialists without their presence being necessary. This solution provided professionals with more safety in the maintenance process and precision, since the cameras attached to the device showed the technicians the current and clear situation of equipment.
According to general director of CMPC, Maurício Harger, the technology provided great success of the operation, which brought together more than 2,400 people and 74 supplier companies. Right after the end of shutdown, the mill reached its historic record for pulp production.
“The AR glasses are an excellent tool, as they brought us the comfort of having the assistance of Valmet experts in real time, without them leaving their homes. On the same day, for example, a field service manager, who was providing remote support, attended a CMPC unit in Guaíba and another in Santa Fé, Chile. This was only possible due to the remote support. Perhaps the shutdown would not have been so successful in the schedule had it not been for the support of Valmet specialists”, analyzes Harger.
Fausto Pires, Valmet's Field Service Manager in South America, highlights all the joint work of the two companies to make the shutdown a success. Meetings and schedules were held months before the start of the operation. “It was a unique and challenging experience, but we had everything very well structured. From Valmet, we had 24 people totally dedicated to the process, in addition to the remote support of seven other professionals and a large support team. Altogether, we add more than 200 people with the responsibility of offering the service that CMPC deserves”, he points out.
For CMPC's industrial director, Dorival Almeida, the use of AR glasses was positive:
"The pandemic accelerated the adoption of other tools similar to the CMPC routine. Therefore, we need to look for a solution that would solve the problem and avoid the crowding of professionals. And the decision to use this technology was very correct. The impossibilities caused by the coronavirus in forced them to be even more dynamic and open to such solutions”, he points out.
For future, CMPC is already studying the adoption of augmented reality technologies in the mill's routine. “The Industrial Internet has a fundamental role in this transformation that we are leading in the Guaíba unit. It can help us create new scenarios that were previously unimaginable. In my understanding, these tools have the opportunity to maximize the work of our employees as we never imagined”, concludes Harger.