One year after the dryer reconstruction: the best technology behind ARAUCO Valdivia's pulp dryer
In mid-2022, an incident affected the pulp dryer at ARAUCO's Valdivia mill, damaging much of the equipment and making the mill's production impossible. In this context, ARAUCO contacted Valmet, a supplier of technologies, automation and services for the pulp, paper and energy industries, with the intention of obtaining technical support and making the necessary repairs to get the dryer up and running and reestablish the mill's production.
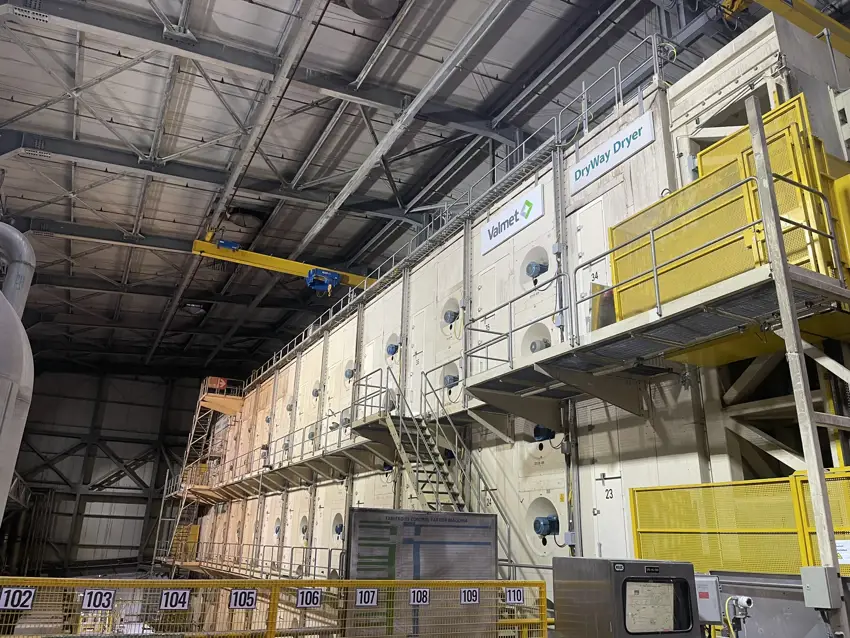
“After the initial assessment, it was clear the complexity of the work and that timing would be our challenge due to the plant's production shutdown. We quickly began to outline our plan to start the repair, dividing the service into two phases of work; the first, aimed at removing 100% of the damaged components, and through a by-pass solution, restarting production as soon as possible, and the second phase, aimed at manufacturing new internal components, installing them, and starting up the dryer,” said Felipe Floriani, Valmet's South America Services Director.
During the first weeks of work, professionals from Valmet Chile, Brazil and Finland, together with Arauco Valdivia, held recurring meetings to discuss strategies for restarting the mill, after which they began the first phase of the service, which was aimed at “by-passing” a section of the dryer, a solution never before executed, and which consisted of removing the damaged components, repairing and adapting the equipment for a reduced production capacity compared to its original design, approximately 75% of the capacity.
Following the positive result of the restart, the work associated with the second phase began, which started with the manufacture of the 6,048 hot air blowing boxes, of which 4,536 were manufactured locally at the Valdivia mill itself and 1,512 in Finland, in addition to 121 heat exchangers.
Later, during the 2023 General Mill Shutdown, the Valmet Airborne Dryer, designed to optimize drying airflows, increase production and operational reliability, was permanently repaired over a period of four months. Finally, the work associated with the equipment repair and renovation project ended in August 2023, with the first bale of pulp being obtained, culminating 120 days of work.
“This project turned out to be one of the largest dryer rebuilds ever performed in the world, a milestone that undoubtedly makes us proud as a team; the work was performed safely, with quality and within the committed deadlines. We put a great deal of effort into developing the solutions that made it possible to reestablish the mill's production, developing the entire project in close collaboration with the customer, in order to deliver not only a renovated dryer, but also the best drying technology. In that sense, Arauco was grateful for Valmet's quick response in a difficult and challenging situation like this one,” said Diego Gonzalez, Mill Sales Manager at Valmet.
“The incident at the Valdivia mill dryer forced the Arauco and Valmet teams to work on a common objective, which was the normalization of the dryer. With this objective in mind, a joint plan was developed that would allow, in a first stage, to operate with a reduced dryer, but maintaining plant production at an adequate level, within the stipulated quality parameters. Then, the challenge was to normalize the dryer to its original capacity, within the stipulated deadlines, but at the same time, with a clear strategy for start-up and enabling, which again, was solved and achieved with the work of both teams”, said Manuel González, Celulosa Valdivia's mill manager.
A little over a year after the project, and in the context of the PGP 2024, developed between October 2 and 16, the last adjustments and implementations were made, which included the installation of improvements in other substages of the machine process, highlighting the installation of cloth change devices, lower and upper, installation of new magnetic flowmeters, among others. All of them are state-of-the-art applications that provide the Valdivia mill's drying machine with the latest technology in the industry, something that only Arauco's MAPA mill has in Chile.