一歩先を行くための "Shared Journey Forward"
メンテナンスは、あなたが実行し、計画し、生産から離れて発展させるような独立した作業ではない。工場メンテナンスの有効性とコスト競争力を分析するとき、利用できる度合いの目標を考慮に入れなければならない。Ahlstromとバルメットは、Ahlstrのメンテナンス方法を発展させメンテナンス効率を向上させるための仕事を共同で行ってきた。
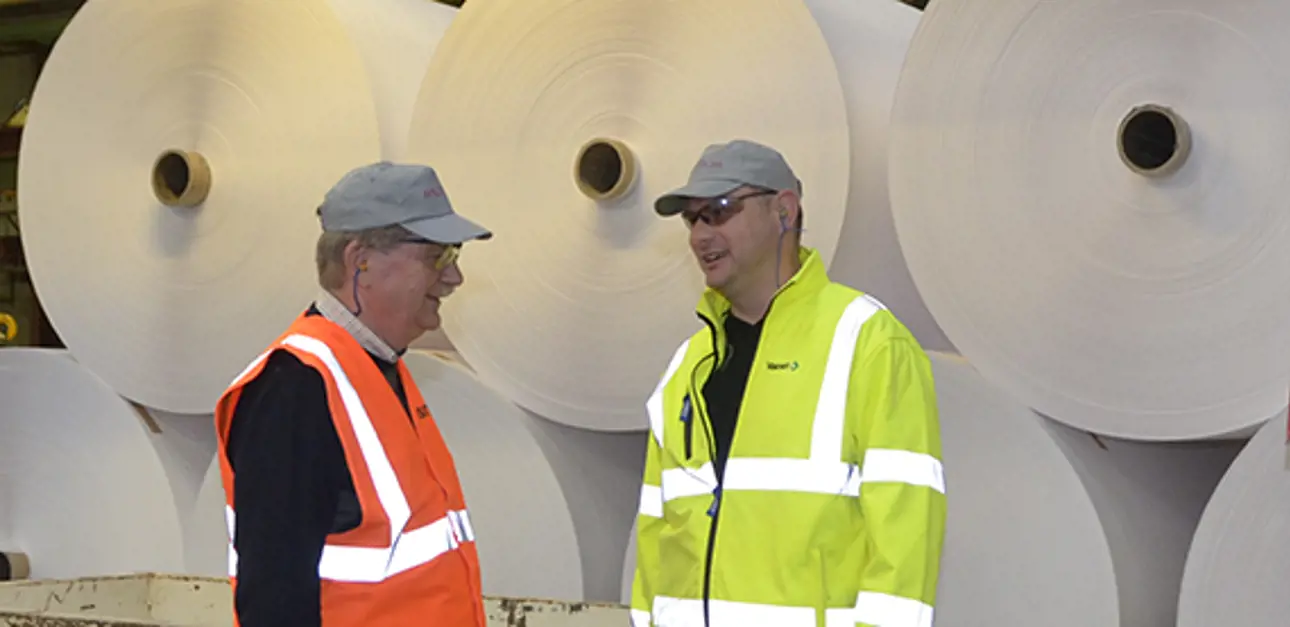
工場のメンテナンスを発展させるための提携契約
2年前、Ahlstromはメンテナンス方法を統一しメンテナンス関連のすべての損失を減少させるための 3年プロジェクトを開始した。目標は、系統的にメンテナンス効率を向上、発展させ、企業レベルの作業方法を見出すことである。
Ahlstromは、日常生活に関わる諸機能を持った革新的な繊維ベース材料の生産、例えばフィルタ、医療用ファブリック、生命科学・診断、壁紙、テープ、および食料・飲料用包装といった応用分野での生産を行っており、全世界に 28工場を有している。
2015年春、Ahlstromとバルメットは、選択的監査とエキスパート評価サービスを実施することによって、Ahlstromの工場でメンテナンスを開発する提携契約を結んだ。契約期間の途中、私たちはフランスにある Ahlstromの Saint-Séverin工場を訪問する可能性があった。この工場は何種類かの応用に供される特殊な高品質の耐脂紙を生産している。すべてのメンテナンス関連のロスは、社内で最小の部類にある。ここでの目標はそのような良い結果を達成するための別のやり方を見つけることである。
サービス契約担当のグローバルセールスマネージャーである Toni Mäcklinは、本プロジェクトにずっと携わっており、すべての工場で Ismo Uronenと共同で作業を行ってきた。ToniはAhlstromのプロセスのユニークさについて話す。「私にとって、これは胸を躍らせる旅でした。私は生涯を通じて製紙者でしたが、このプロジェクトによって私は静電塗工やナノ塗工のような特殊な技術を目にしてきました。これは同時にやりがいがあり、教育的であり、興味深くあります。アールストロームは非常にアクティブな R&D部門を持った革新的な会社であり、絶えず新しい生産技術を開発しています。」
Ahlstromは、その特殊な製品範囲のための特殊な生産プロセスを使用
すべての工場で最良の実践
Ismo Uronenは、このプロジェクトでバルメットと共同で作業する方法は常に発展すると説明する。
両者はプロジェクトの間に学習しており、これが新しい可能性を与えてくれる。「私たちが手がけた最初の 2, 3の工場では、何人かのバルメットの人と共に働らきました。そのときから、私たちは自分たちのシステムについて多くを学びました。それで、Toniと私の ノウハウは改善しました。そして今年は、私たち二人だけでこれらの工場の調査を実施してきました。」
彼は目標について続けて言う。「プロジェクトの目標は毎年決められます。私たちは、既に非常に高い効率を有する工場がいくつかあるのを見出しました。これらから、私たちは彼らの成果を学んで、そのノウハウを他の工場に伝達することができます。」
Toni Mäcklinは一例を挙げて話を続ける。「私たちが今年訪問した工場では、メンテナンス担当者と操業担当者のグループミーティングを持ちました。彼らは自分たちが観察した改善の必要性と可能性を書き留め、そして私たちは改善リストを作成しました。工場に利益をもたらすようないくつかの小さな事柄がありました。」
これは人に関係している
Toni Mäcklinはすばらしいメンテナンス結果をもたらす鍵についての明確なビジョンを持っている。「メンテナンス組織の性能はメンテナンス担当者の能力と献身に大きく依存することを、私たちは覚えておかねばなりません。メンテナンス費用は保険証券のようなもので、使えば使うほど、より良い利用可能性が期待できます。重要なことは、すべての工場で正しいバランスを見出すことです。高い利用可能性が必要であるときは、予防保全のためにより多くのインプットが必要となります。」
提携契約はまた人々にも関係している。Ismo Uronenはバルメットとの提携に非常に満足しており、とりわけ Toni Mäcklinには満足している。「Toniはバルメット側でのすべてをまとめました。彼のしっかりとした経験は私の仕事を容易なものにしました。私は正直に、適切な時に適切な場所に適切なバルメットの人員がいつもいてくれた、と言えます。バルメットは本当にこのプロジェクトに成功したと思います。」
工場の生産高はメンテナンス効率の最良の指標
Ismo Uronenは工場のメンテナンスについて学んだことを説明する。「これまでのプロジェクトからの鍵となる教訓は、メンテナンスや操業を個別に発展させるのでなく工場を1つのチームとして発展させねばならない、ということでした。結局は、メンテナンス効率の最良の指標は生産高です。これは、はっきりと示すことのできる唯一の指標でもあります。私たちの目標は、総合的な工場の発展です。」
バルメットのサービス契約担当グローバルセールスマネージャー Toni Mäcklin(左)と Ahlstromのエンジニアリング技術マネージャー Ismo Uronen氏
「私たちは今では類似する装置を持った工場のための共通する実施例、例えば消耗品の節約とかを見つけて達成していくより良い手腕を持っています。このプロジェクトの間、私たちのメンテナンス構造を正しい方向に、すなわちもっと計画的なメンテナンスと突発の休転をより少なくする方向に向かわせることができました。メンテナンスでの節約は単に費用をカットするということでは有り得ません。メンテナンス効率の改善が実際に節約をもたらすための投資です。」と Ismo Uronenは締めくくった。